Unique Propping Design Suspends 400 t Heritage Clock 55 m High During Restoration Works
An innovative bracing and propping solution developed by TTW (Taylor Thomson Whitting) and Multiplex has just won an Australian Engineering Excellence Award (AEEA) 2020. Their unique temporary works solution was used for Brookfield Properties’ redevelopment of Sydney’s Shell House: a 1930’s commercial palazzo-style heritage building, formerly owned by Shell Oil Company.
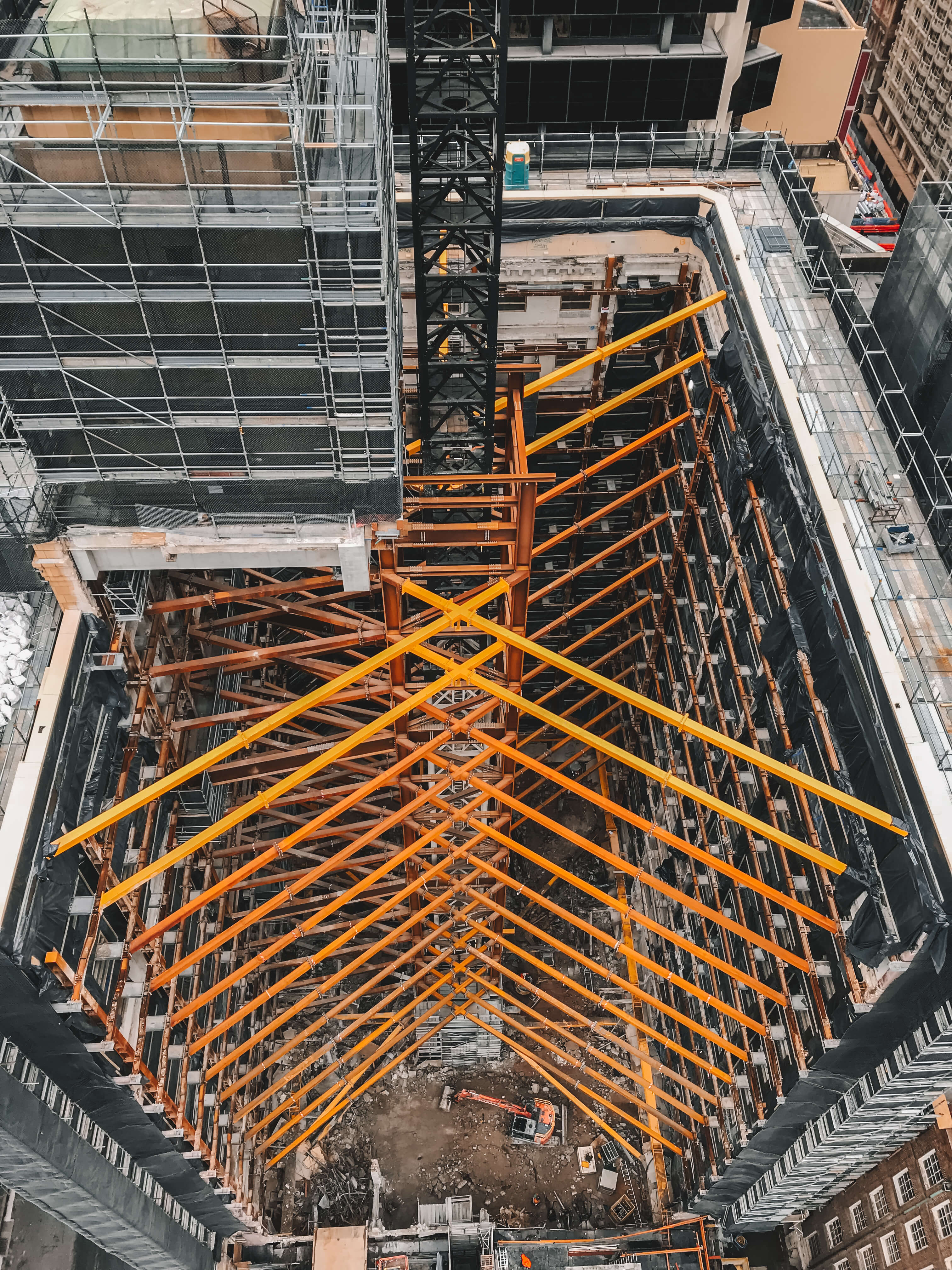
The intricate bracing and propping design enabled the building’s 400 t heritage clock tower to be suspended over the live construction site while the building is being restored.
The solution also allowed bracing of the 65.5 m heritage facade while Shell House was completely gutted and upgraded, including demolition of its structural system. Upon completion, Shell House will boast one of the tallest retained heritage facades in the world.
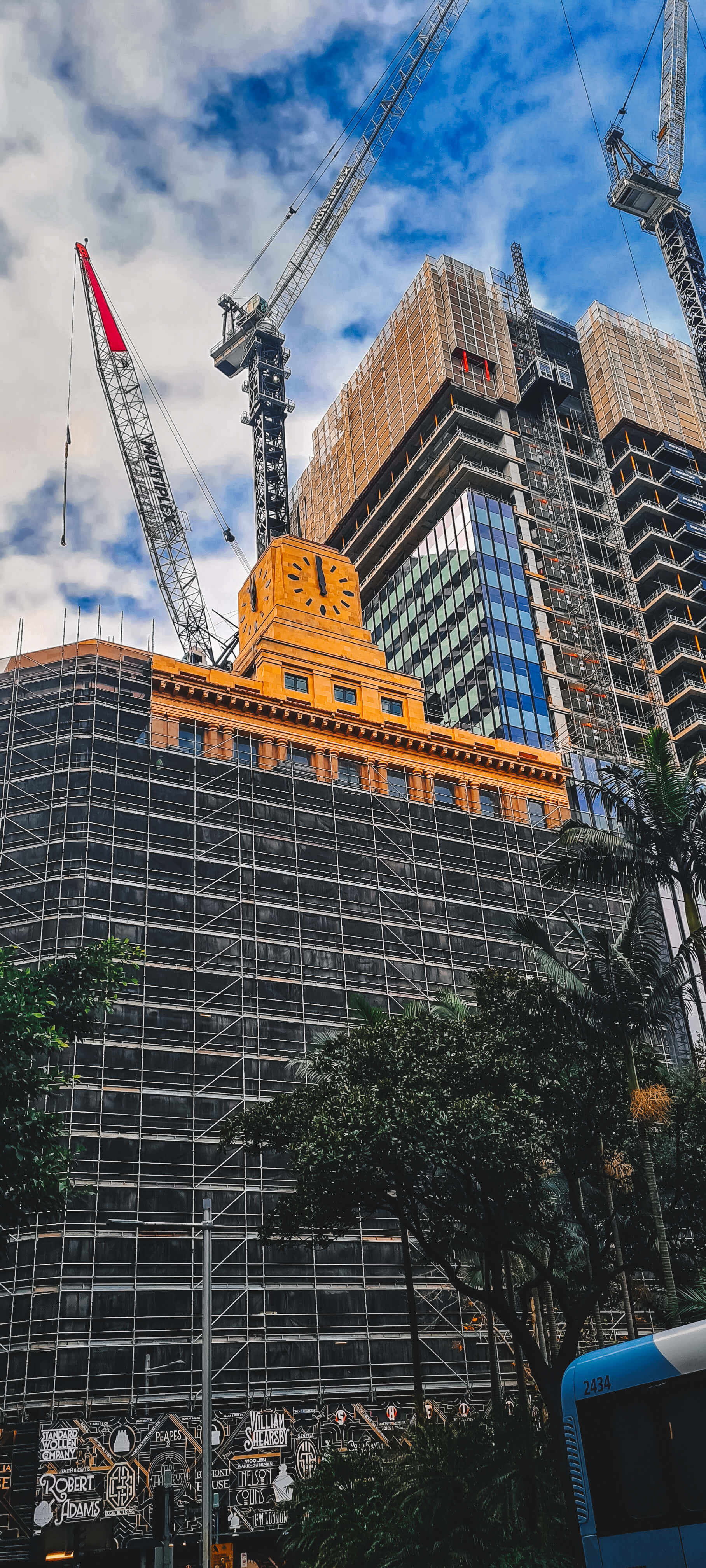
The works are part of the Brookfield Place Sydney project (formerly Wynyard Place) which also includes the construction of a 27−storey commercial tower at 10 Carrington Street and the upgrade of heritage-listed Beneficial House. The project is being developed by Brookfield Properties and built by Multiplex.
TTW produced an intricate interplay of bracing, columns, and beams to create a comprehensive support structure that is designed to account for the high risk of deflection in such a tall masonry building, with Multiplex providing numerous sequence and methodology revisions driving and refining the design. Belmore Engineering & Mulherin Rigging & Cranes supplied and installed 2400 t of permanent and temporary structural steel for the project.
“An external facade retention system is often preferred to keep the construction zone clear of obstructions,” says TTW associate and head of the construction engineering team, Martin Folan, “but it became clear that to construct a system with sufficient stiffness to control deflections and support the clocktower, the primary support structure would need to be internal.”
The solution involved the erection of a temporary stability core in the building’s lightwell, supported on plunge piles built into the foundations. 12 m long steel outrigger beams then connect this core to temporary and new permanent support columns for the clock tower.
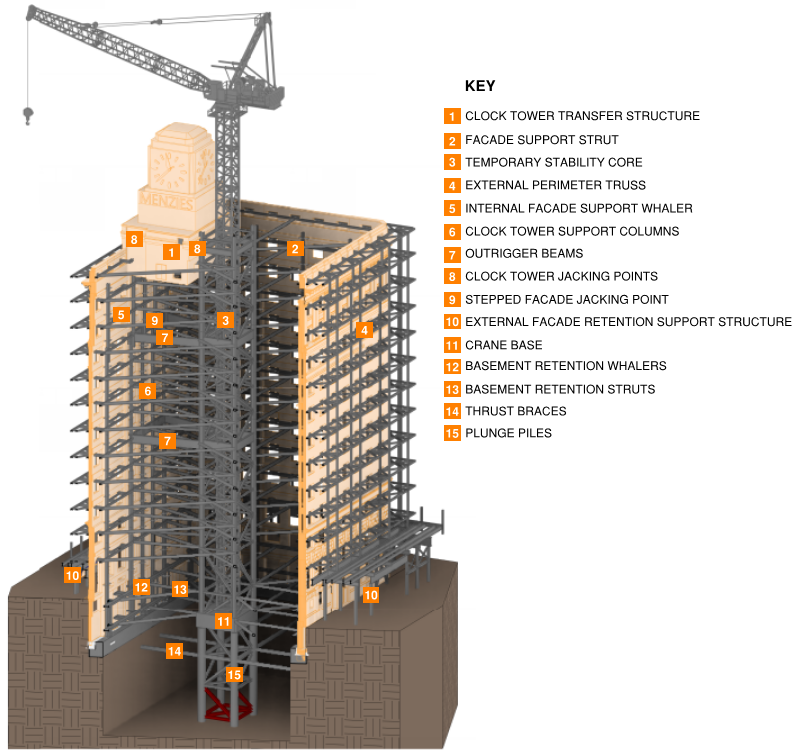
A 380 t permanent reinforced concrete transfer structure was constructed beneath the clock tower, formed off the existing building. Hydraulic jacks on the temporary support structure then took the weight of the clock from the original concrete-encased steel structure by ‘squashing’ the new support columns under the clock’s weight, supporting the clock without actually moving it.

The new temporary and permanent supports suspended the clock 55 m above ground while works continued below.
Martin Folan explains, “A steel corbel was developed and detailed to be torsionally stable and cantilevered off the stability core to support the clock tower. The design ensured eccentricities due to jack positioning and engagement could be accounted for in the load path back to the braced frames of the core.”
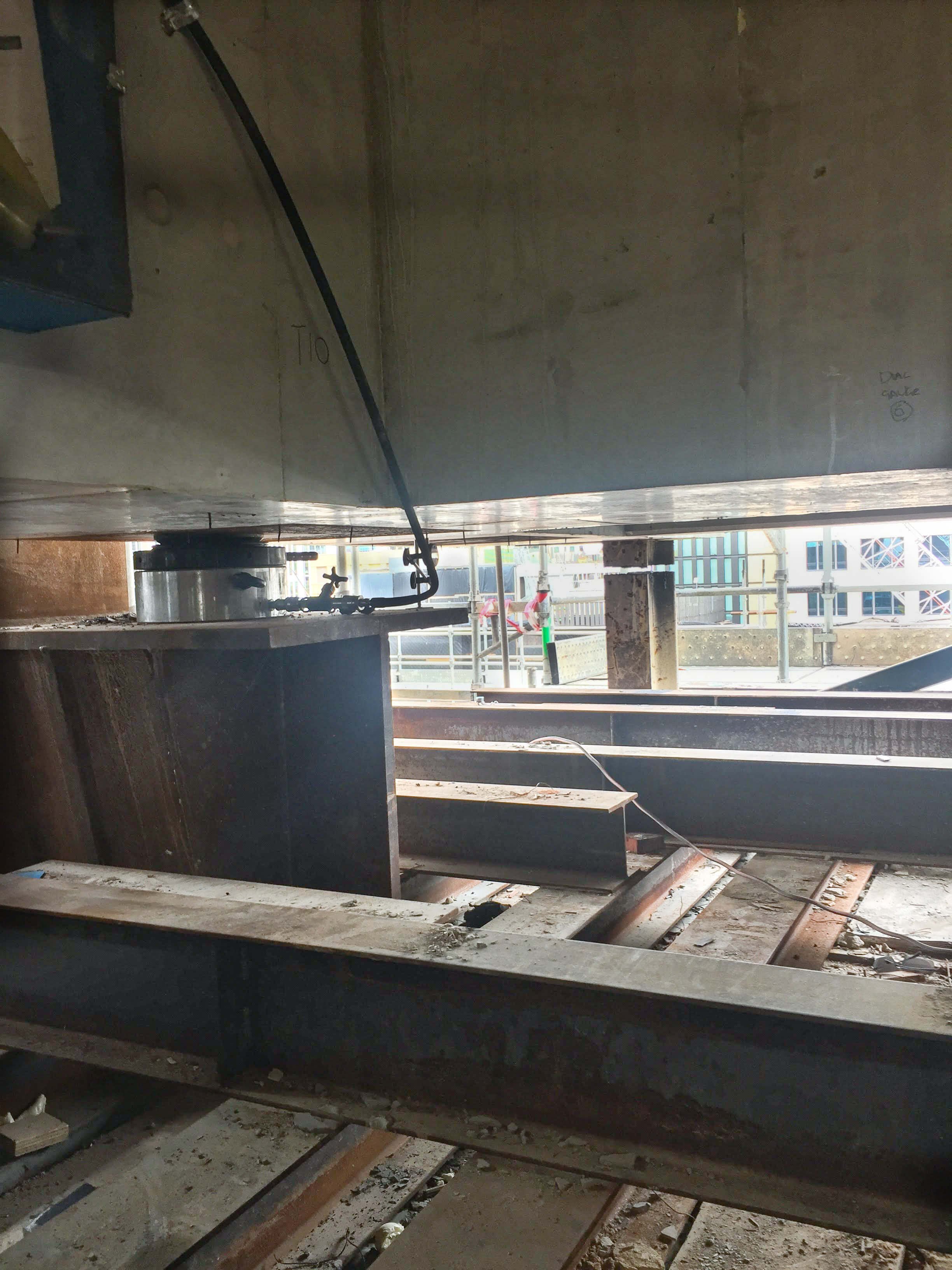
Axial elongation of the existing supports and shortening of the new supports had to be considered when the 780 t combined weight was lifted and transferred. Of critical concern was the impact of the column shortening on the facade connections.
“All facade connection stubs included vertical slotted holes to allow for axial shortening of the new columns but also axial elongation of the facade columns as the load was removed from them with each level of demolition,” says Folan.
Multiplex and TTW braced the facade on the external face using a series of horizontal trusses laid flat, which are supported vertically by a bespoke class B structural steel hoarding. On the internal face, walers provide internal support to the facade and are supported laterally by the central core.
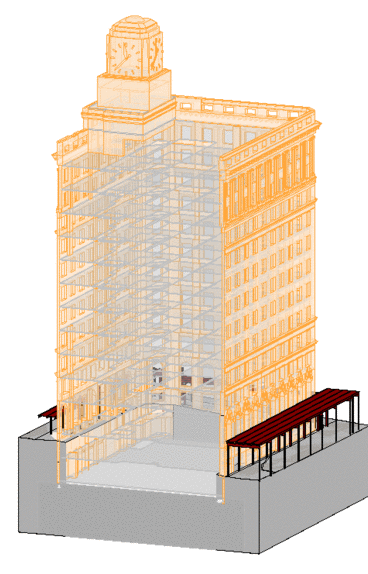
“The design of the facade retention support structure required stringent vertical deflection tolerances to mitigate the risk of additional loads on the existing facade, including under accidental damage/removal of any one of the street level columns ” says Folan.
Inside the structure, a unique arrangement of diagonal bracing tied back to the core provides additional lateral stability, which was designed to weave through the building’s original column grid and facilitate construction of the new concrete core and columns.
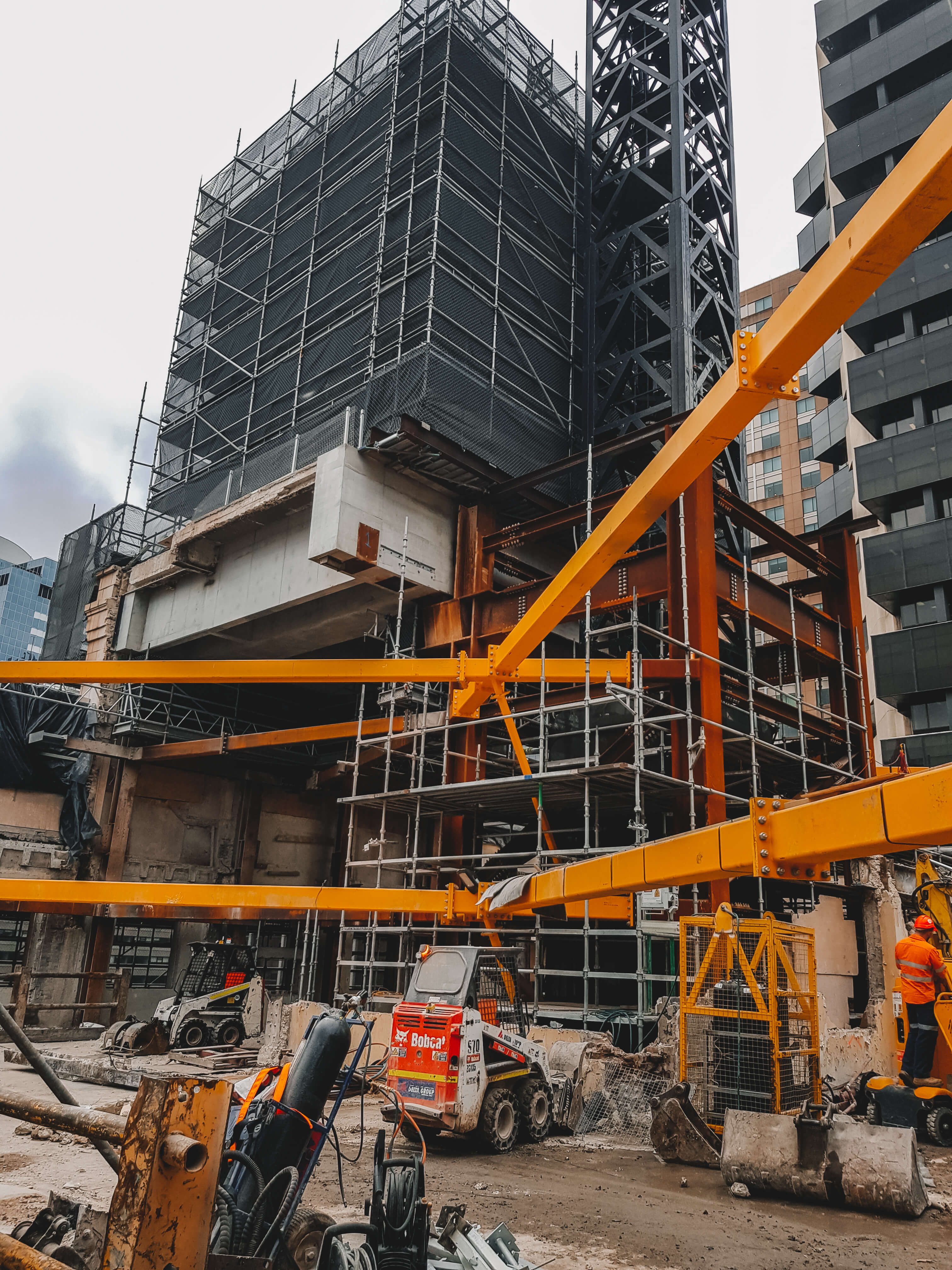
“The level of the facade retention system relative to the existing floor plates was located to provide a minimum 2 m head clearance to allow people and equipment to operate on the existing floor plates unrestricted,” says Folan.
TTW adopted stringent criteria to ensure the integrity of such a fragile structure in the presence of significant forces would not be compromised during the tedious procedure. Global out of plane displacements were limited to H/750 whilst analysis of in-plane strain limits was undertaken to predict the onset of visible cracking of masonry.
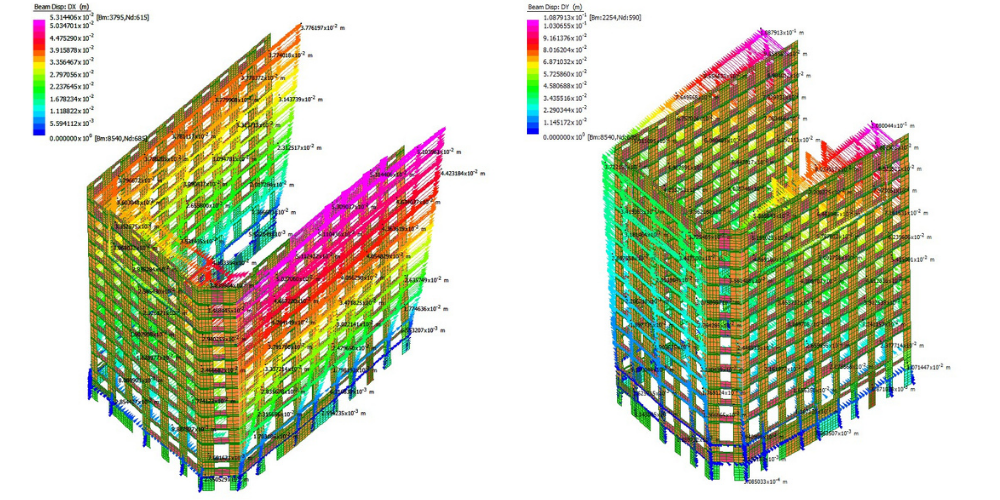
Live movement monitoring supplemented by traditional survey methods were deployed throughout the demolition, excavation and construction phases. The live monitoring system provided real time data linked to preset trigger levels at specific locations on the facade. Traditional surveys provided a method of verification for any live monitoring triggers and were scheduled weekly as a standard operating procedure for the site.
The project also saw the top-down construction of an additional 15m of basement below the existing basement level and adjacent to the existing MetCentre tunnel running parallel to the Carrington Street facade. Lateral support was provided to the central core through a bespoke system using thrust braces.
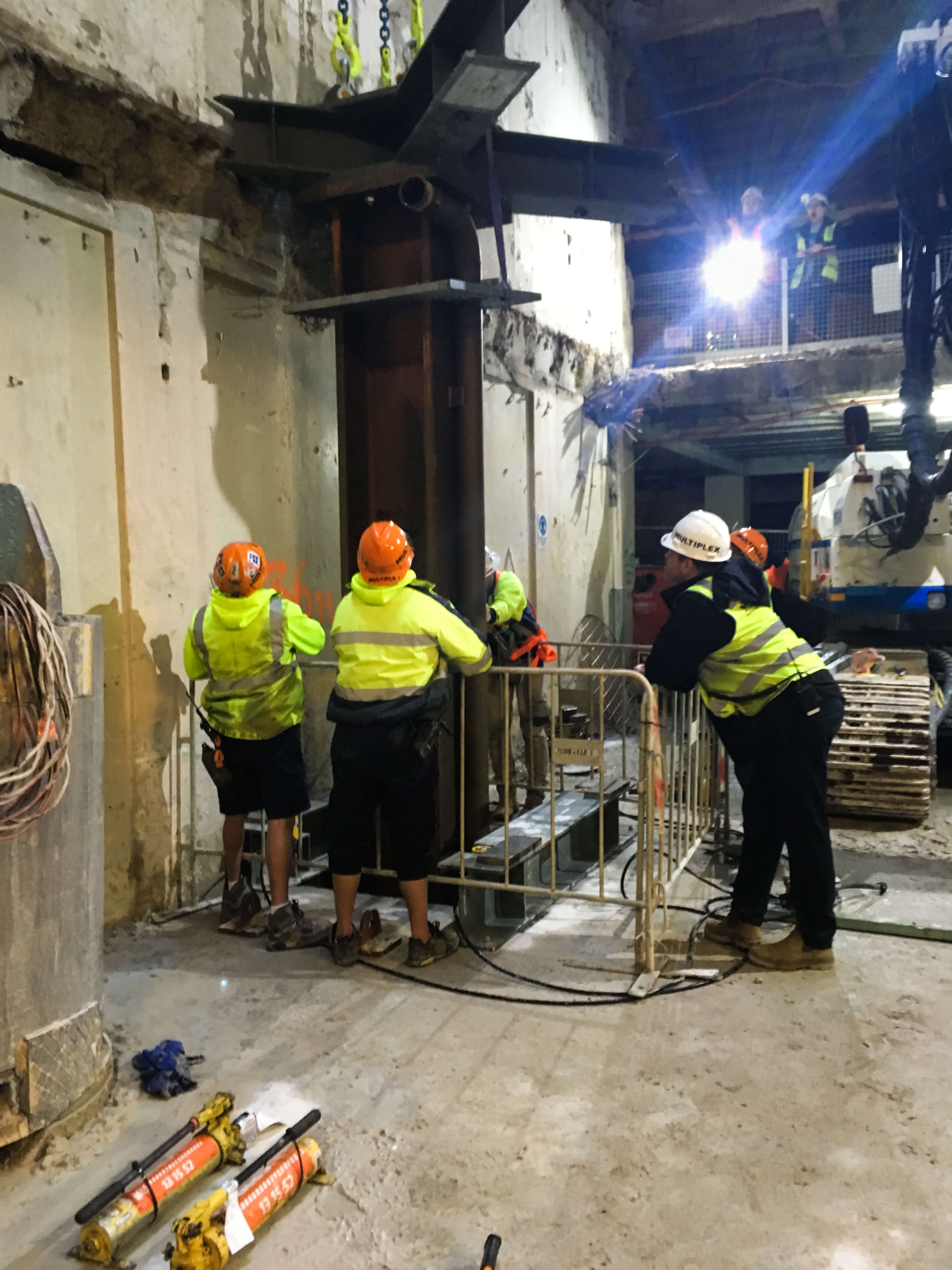
Geotechnical advice predicted up to 13 mm of rock relaxation at the top of bulk excavation level. Accounting for this rock relaxation would have imparted significant load on the thrust braces, well in excess of the resistance required to support the temporary stability core.
“Rock relaxation occurs progressively as the excavation depth increases and so every increment of excavation after the thrust braces were installed would push a compressive load into the braces,” explains Folan.
To solve this, TTW developed a bespoke interlocking friction plate connection that allowed slippage at high load (due to rock relaxation) to shorten the thrust brace member, whilst still maintaining the design resistance required for basement retention loads without slippage.
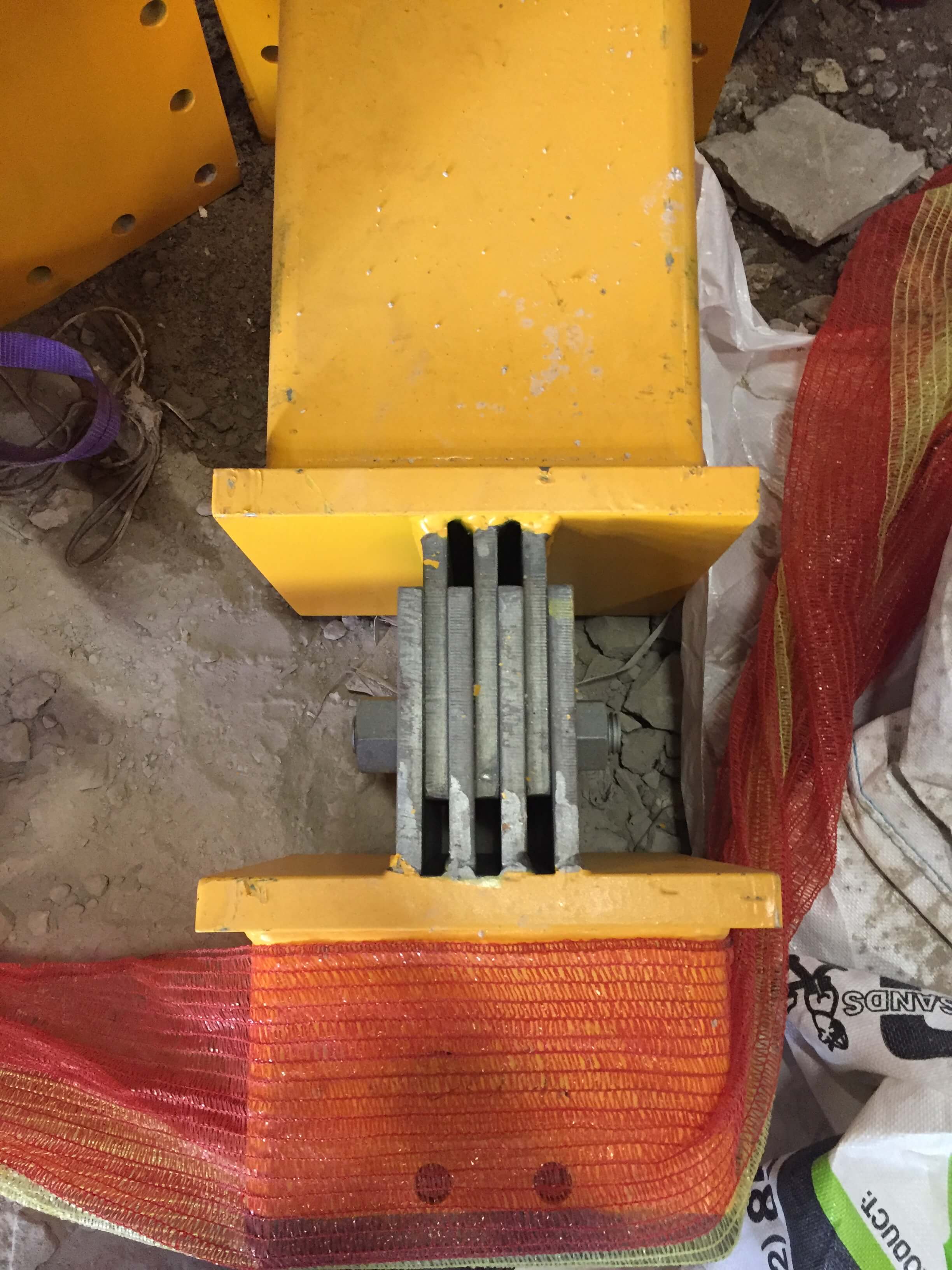
“Due to the range of friction factors possible we undertook a sensitivity analysis of upper and lower bound friction factors to test this connection and its impact on the core structure. This also meant that these connections did not need to be accessed again after installation,” says Folan.
Brookfield Place Sydney was designed by MAKE Architects in conjunction with Architectus. Once completed, the 134 m, 27−storey development, will provide 69,000 m² of boutique 6-star Green Star office space, 7000 m² of high-end retail, a revitalised Wynyard Lane and a revamped George Street entrance to Wynyard Station, which connects to a grand multi-level transit hall and public concourse.
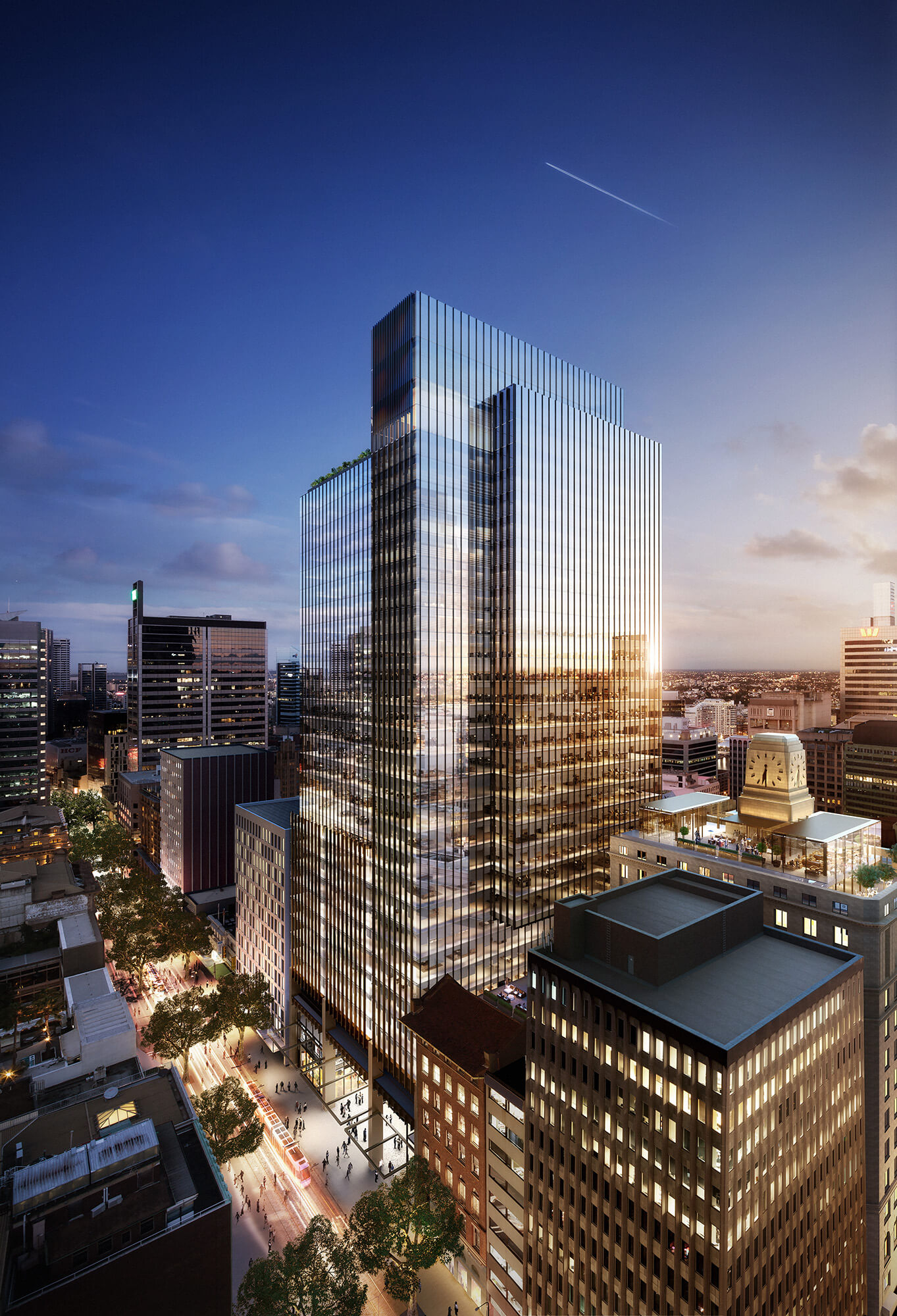
Completed in 1938, Shell House was the Sydney headquarters for the Shell Oil Company. It was the company’s fifth building erected in an Australian capital city. It was designed by Australian architects, Spain & Cosh, and constructed by Howie Moffat and Co in the 1930s.
The restored clock, made by Gillett & Johnston, will include a new digitally controlled time-keeping mechanism, with the original to be extracted and made available for public display inside the building.
Shell Oil Company operated out of the building until the 1970s when it was converted into The Menzies Hotel. It is the only remaining Inter-War commercial palazzo-style building in Sydney that is clad in glazed terracotta tiles.
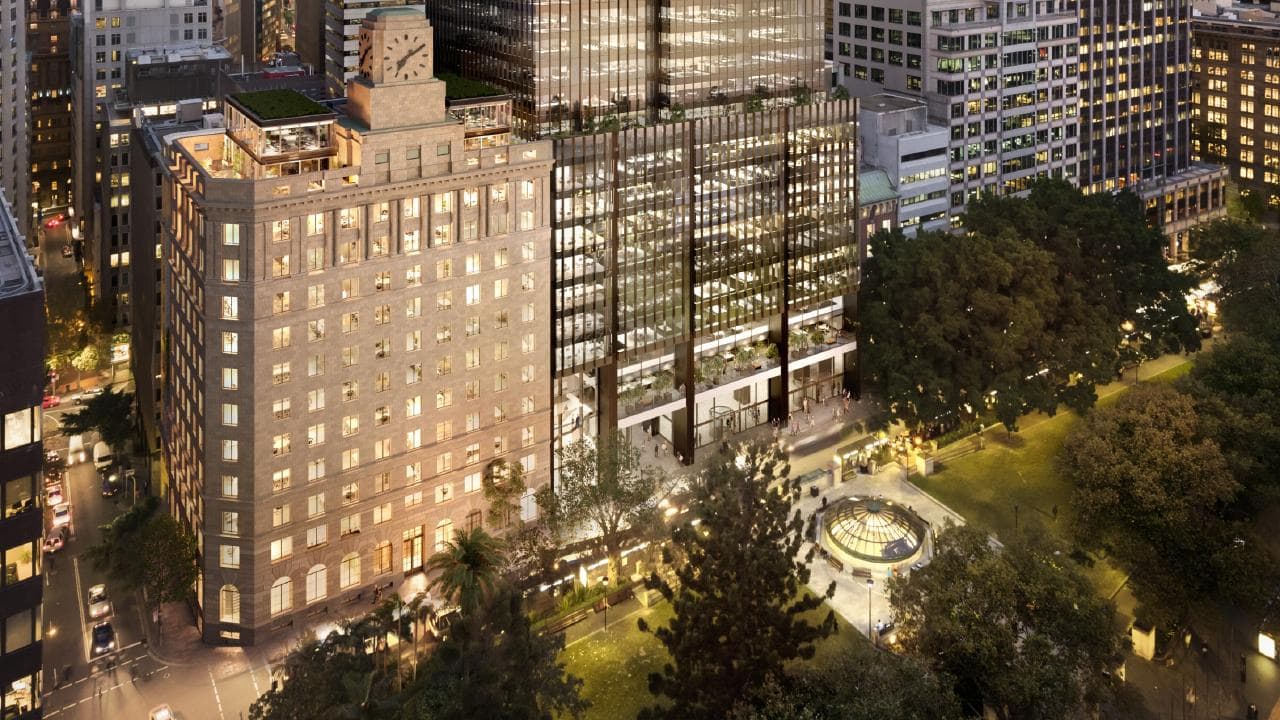
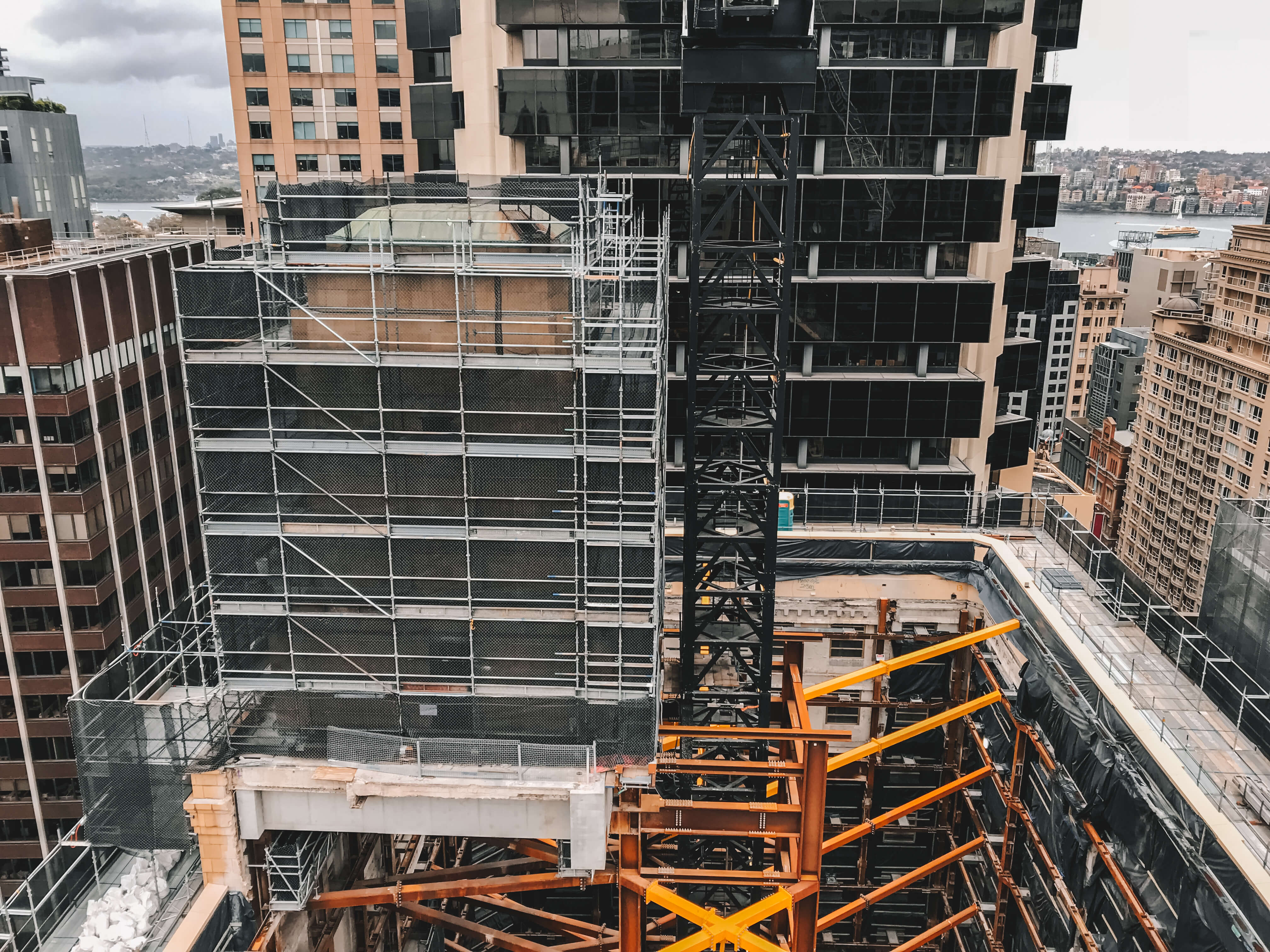
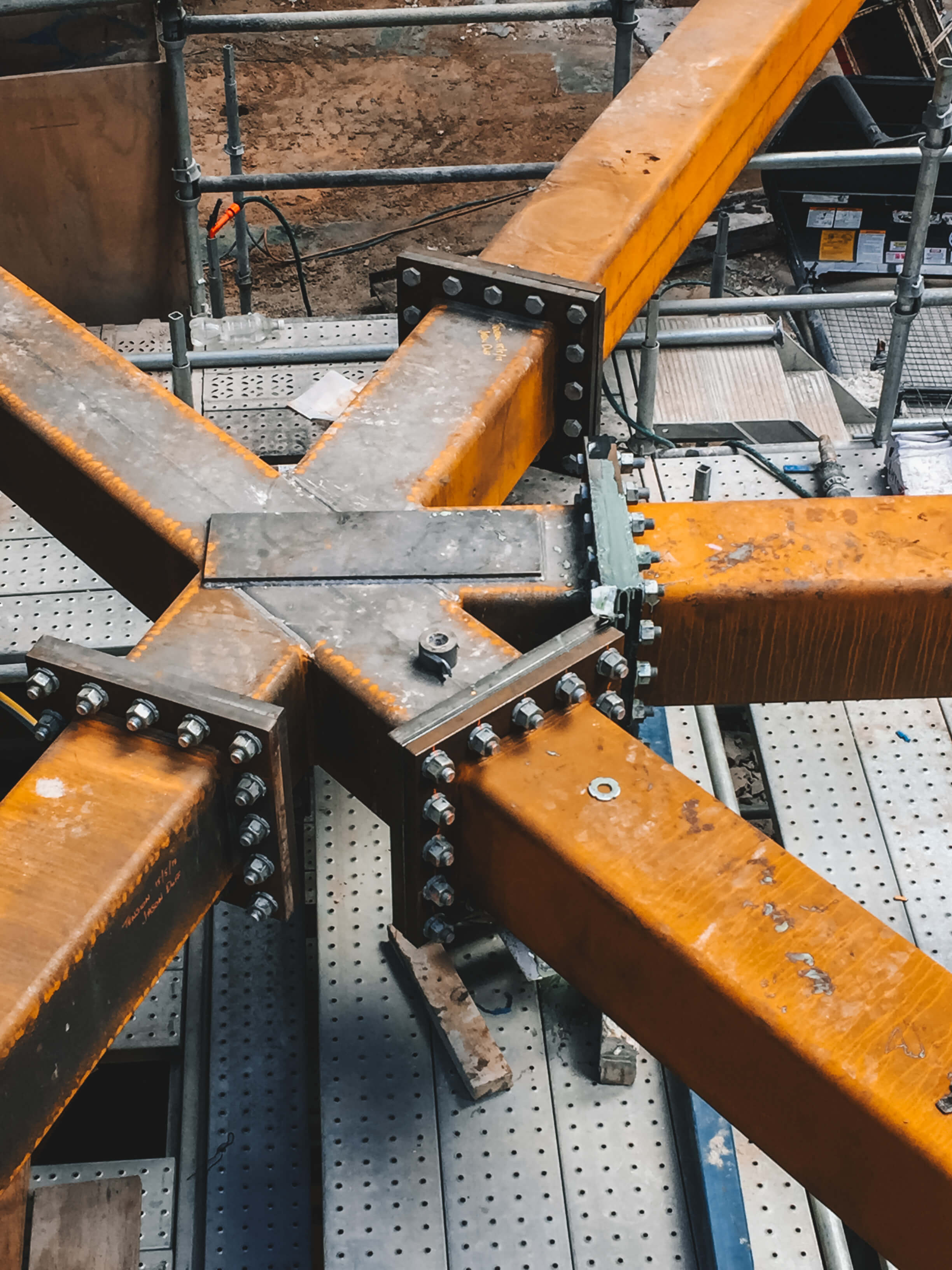
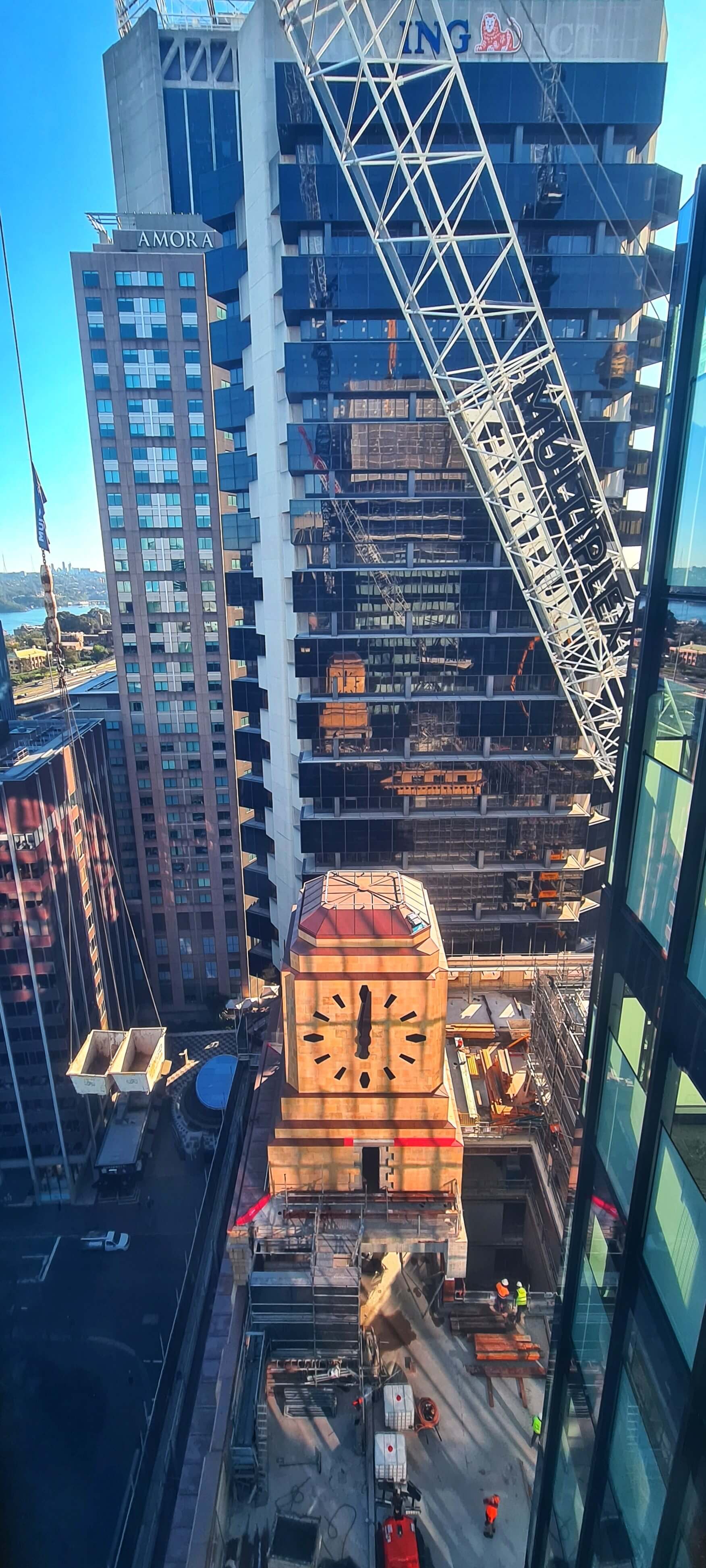
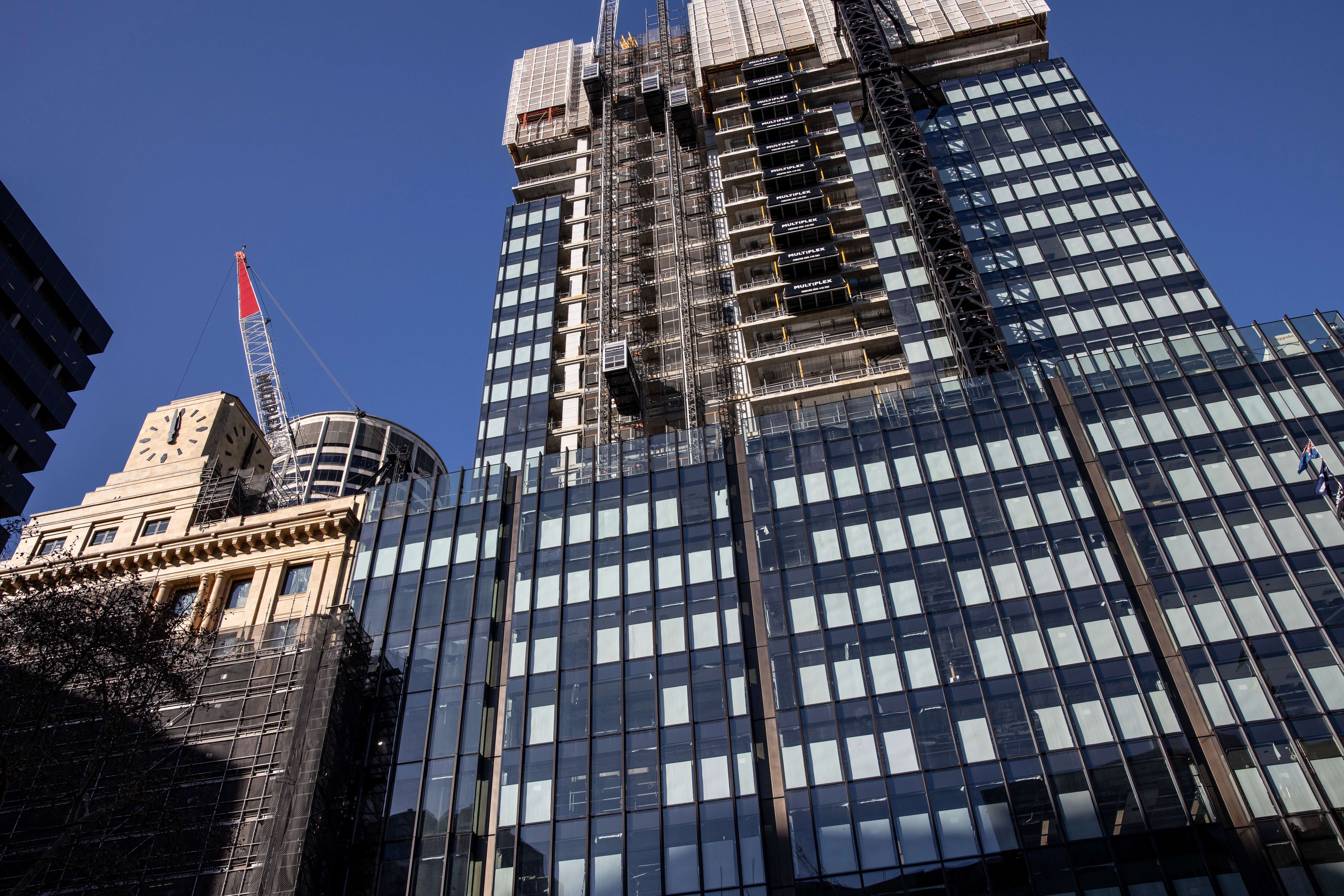
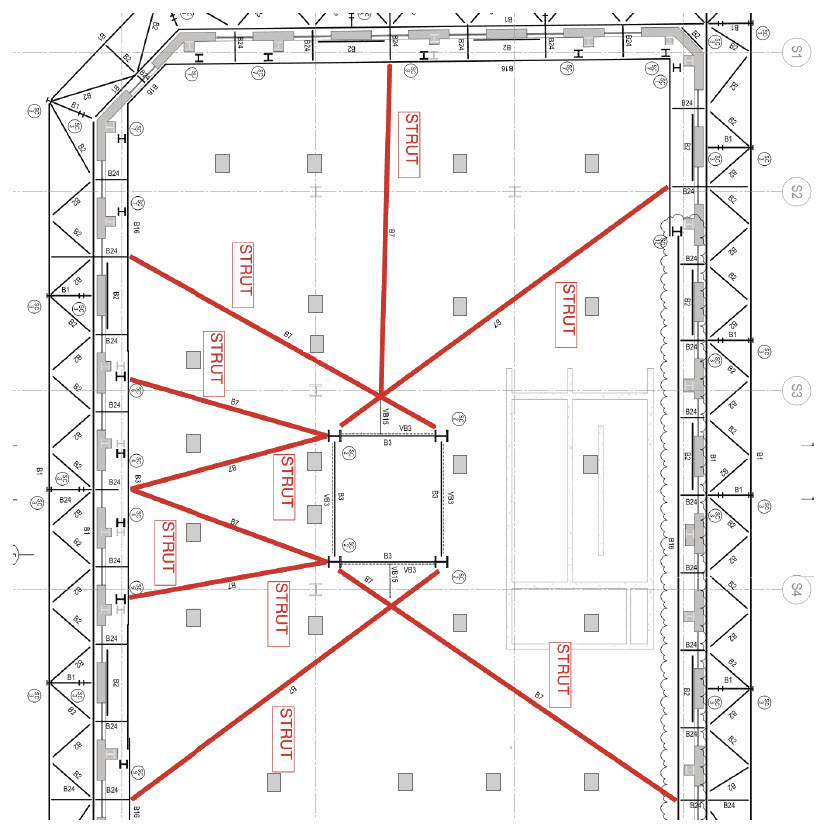
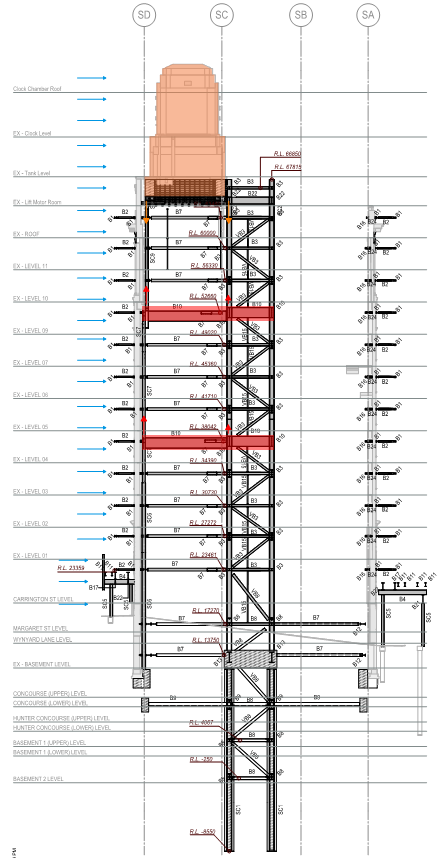
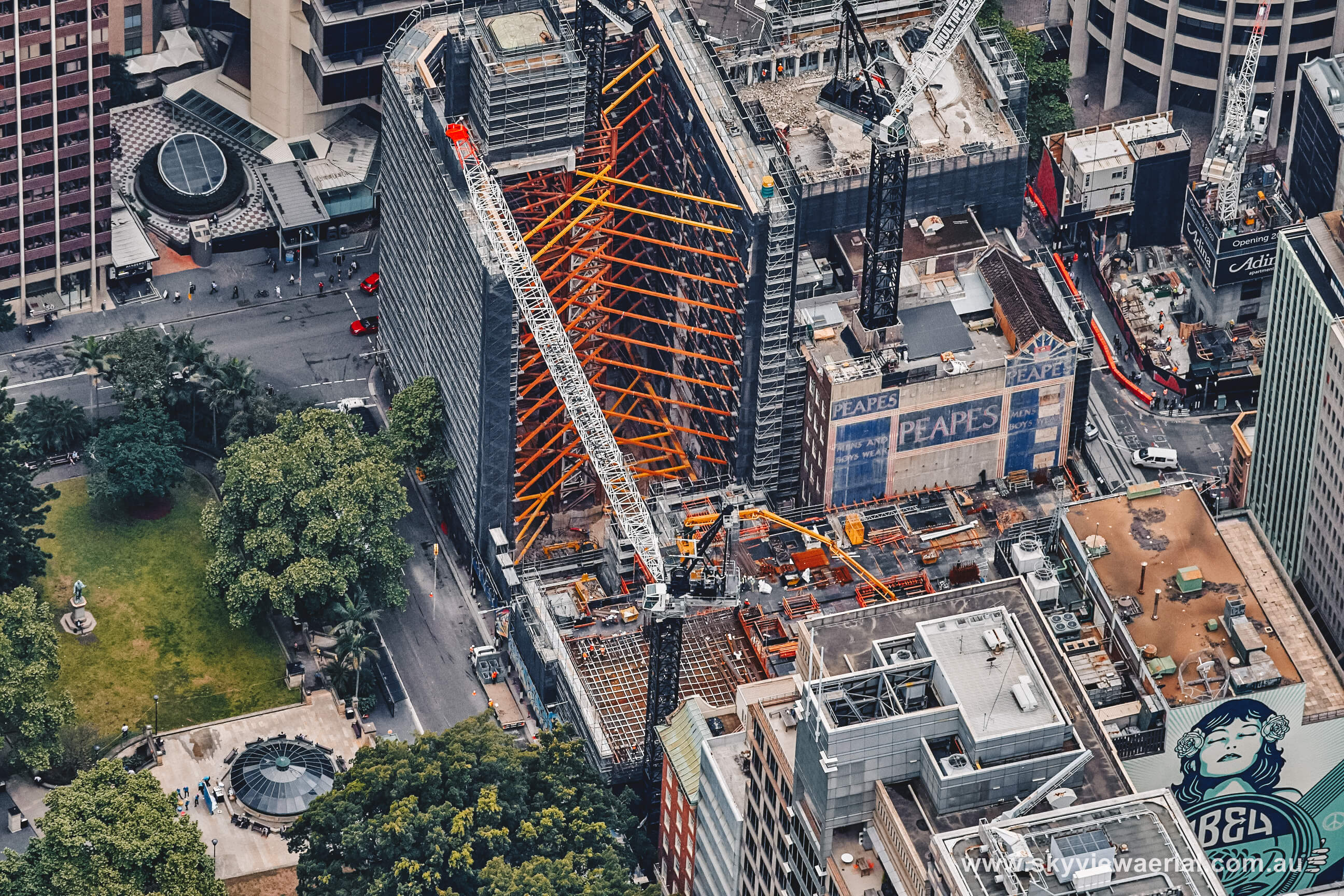
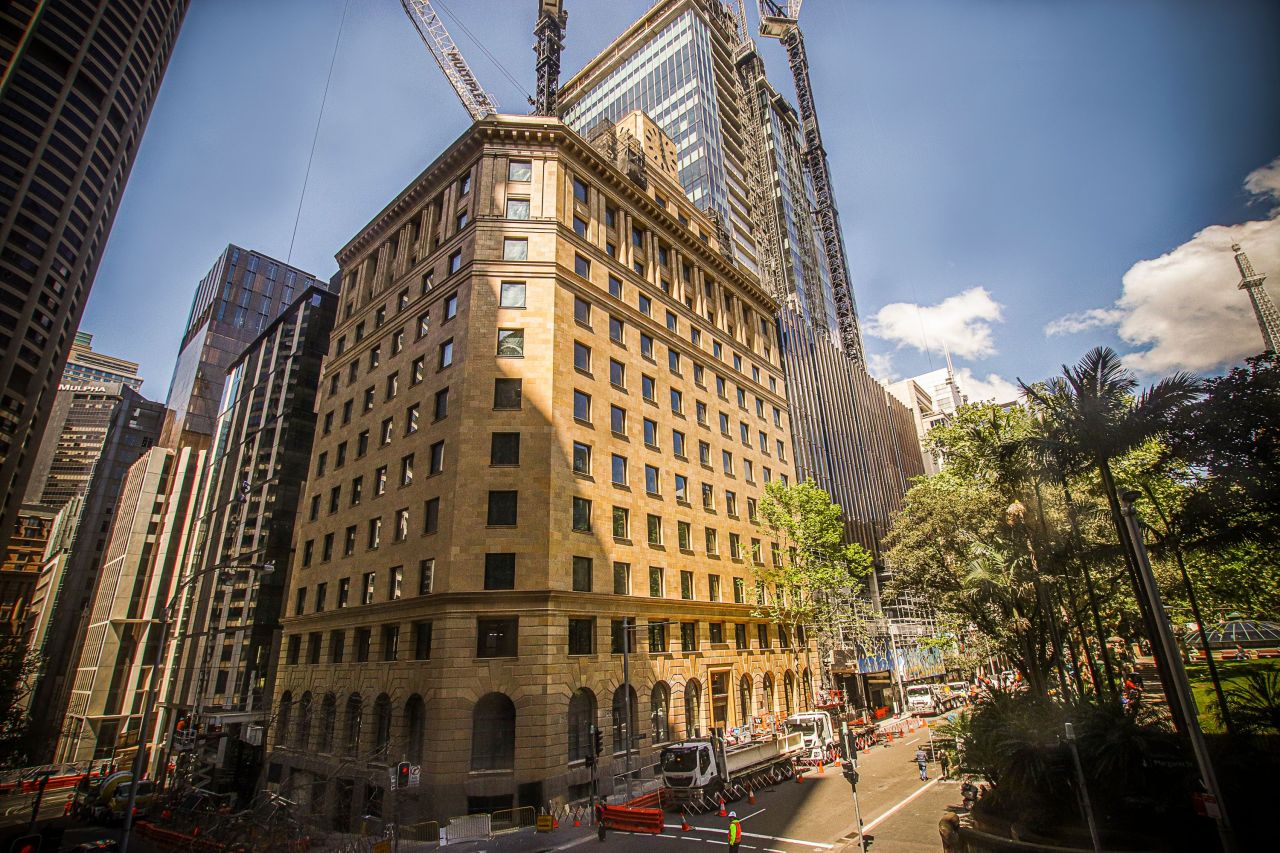