Why Haven't Buildings Become Productised? An Exploration of the Possibilities and Barriers to Buildings of the Future
Peter Greaves is the buildings of the future leader at Aurecon.
Chapter 1: Design and construction in the 21st century
Why haven't buildings become productised?
Innovation in the construction industry has been a slow process. Despite advances in technology, and the emergence of industrialised construction some 60 or so years ago, we are still ‘swinging hammers’ on site, creating buildings that are all unique and bespoke. Why is that?
What’s missing? Why hasn’t industrialised construction disrupted the way we design and construct buildings?
The late Harvard Business School Professor and businessman, Clayton Christensen, coined a theory of disruptive innovation which explains this as the way in which companies enter a market at the bottom with a product or service that may be a less expensive and more accessible version of those at the top of the market. Through relentless growth these new entrants eventually move up to the top of the market, displacing the incumbents.
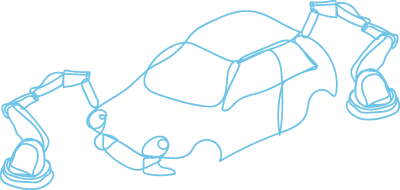
Taking this meaning of innovation, you could say that Henry Ford was one of the greatest innovators of the 20th century. Ford did not invent the automobile, nor did he invent the manufacturing process that enabled cars to become the ubiquitous machines they are today. He merely combined inspiration from the past with a vision for the future and a belief in the changing power of technology. He joined the dots of already existing components to transform what was originally a vehicle for the wealthy few, to a means of accessible transportation for the masses.
How did he do it?
As well as developing cars such as the Model T in 1908, he revolutionised the assembly line, driving down the cost of Ford automobiles to the point where the average wage earner, including his factory workers, could afford them. With the Model T becoming so commonplace, sidewalk gas stations started popping up, eventually bought by the large oil companies such as Shell, Esso and Texaco, with nozzles that fitted perfectly into the Model T’s tank, thus creating standardisation, accessibility and convenience of petrol to fuel the new wave of automobiles.
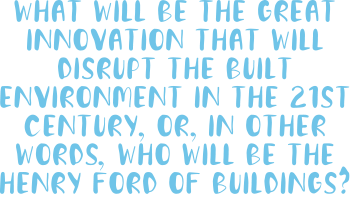
Mass manufacturing of cars only took 20-30 years and has become mainstream since the advent of Henry Ford’s moving production line. Now virtually all cars are constructed in this way.
While we have been doing variants of industrialised construction for 60 years, it still isn’t the norm.
What are the blockers?
Does the current design process involving architects and engineers working on bespoke designs prohibit efficiencies and scaling?
Are there fundamental differences between market maturity, customer expectations and supply chains for cars as opposed to buildings?
Will industrialised construction only have a role to play in emerging economies or large population regions?
Is there another newer technology that might leapfrog industrialised construction and pave the way for a different future?
How do we bring design and construction into the 21st century?
Design and construction have been luddites... but things are changing.
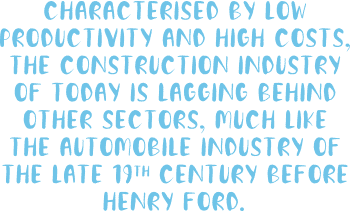
Design and construction in the 21st century is characterised by unique components being brought together on-site, resulting in supply chains, materials and processes requiring precise alignment to avoid cost and time overruns, and ultimately, gross inefficiencies.
The result is that while increasing populations and urbanisation are leading to rising demand for construction, pushing up revenues, both profits and affordability are decreasing. Cost and time are therefore becoming even more of an imperative for return on investment (ROI) and overall growth. In 2016, McKinsey & Co. estimated that 80 per cent of construction projects were over budget, and 20 per cent ran over time.
Compared to the auto parts manufacturing industry where the average return on equity (ROE) in the US is approximately 12.5 per cent, the engineering and construction industry ROE is 3.4 per cent as at January 2020.
Productivity in the construction industry is also lagging behind, not just manufacturing, but the total economy, and has stayed relatively static over the past 20 years, as demonstrated in Figure 1.
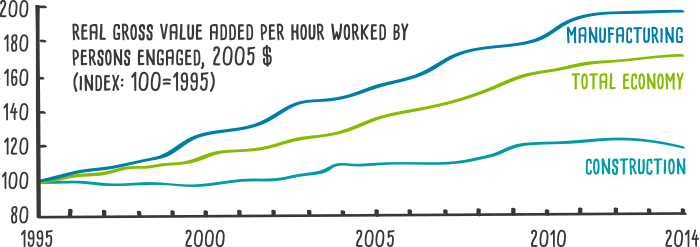
Affordability and accessibility of residential and commercial buildings is also not improving in most economies. Just like the automobiles of the late 1800s, housing, in particular, is becoming restricted to the wealthy few.
In the latest research from the International Monetary Fund’s (IMF) Global Housing Watch, house prices have grown faster than incomes in over half the countries surveyed, over the five years from 2015 to 2019, as shown in Figure 2.
Yet, if we need to build 10,000+ buildings a day to cater for a 10 billion world population by 2050, how are we going to achieve that without significant change in the way we design and construct buildings?
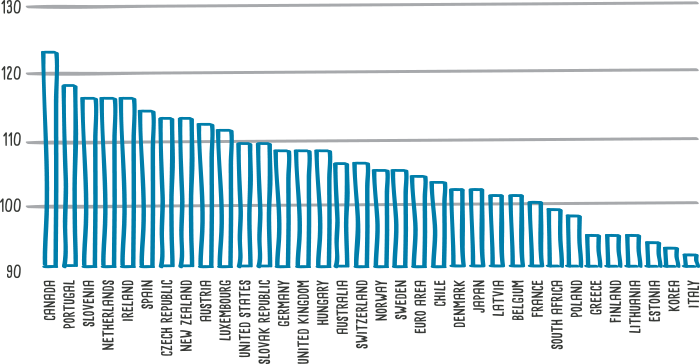
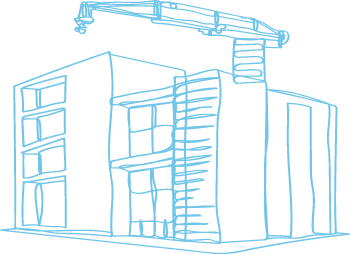
The World Economic Forum in collaboration with Boston Consultant Group in their paper Shaping the Future of Construction – Future Scenarios and Implications for the industry, identified global megatrends such as climate change, shifting demographics, the cost of labour in some regions, urbanisation, automation and digitisation as creating a burning platform for change.
The report showcases three extreme versions of the future:
- Building in a virtual world – where virtual reality touches all areas of life and intelligent systems and robots run the construction industry
- Factories run the world – a corporate-dominated world using modularisation and prefabrication resulting in the convergence of manufacturing and construction
- A green robot – a world of scarce resources and climate change, in which we rebuild using eco-friendly construction methods and materials
Alternatively, a hybrid of all three may emerge, enabled by blockchain’s self-executing contracts, or smart contracts, which can create trust and transparency between project partners, making the construction process easier, cheaper, safer and faster.
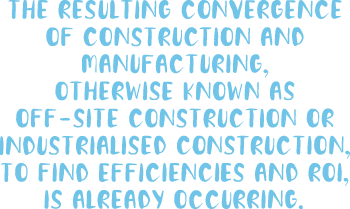
Case study: Buildings clipped together like lego and delivered to site - ModnPods
Modularisation has been around for some time, but finally gaining momentum due to new technologies and economic drivers. One example of buildings being clipped together like Lego in a factory, from standard components, then delivered to site, is ModnPods, designed and built on Australia’s Gold Coast. ModnPods are constructed using standard components such as shipping containers or a pre-designed steel frame. The build time is just eight weeks and each ModnPod comes complete with fixtures and fittings such as windows and doors, as well as all plumbing, electrical and mechanical components.
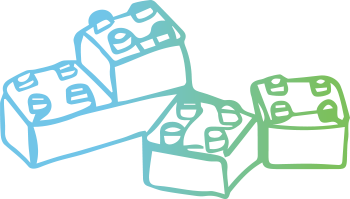
Customisation is also available in the form of ‘clip on’ extras such as timber decks. Sustainability aspects such as solar panels, grey water processing, wood panel composites (a blended composite of recycled PE bottles and used industrial pallets or other woods) are also available. Marketed as ‘backyard’ homes or offices, multi-unit developments and caravan parks, the pods range in size from a 3x3.4 metre studio for AUD 29,600 up to a 12x3.4 metre two-bedroom house for AUD 99,000. With a commitment to giving back, ModnPods donates a portion from the sale of each pod to third world countries, to provide more affordable housing and schools.
Prefabrication and the impact on construction
Prefabricated construction and automated technology, such as robotics to install these prefabricated construction materials, and additive printing, are all construction technologies that can be implemented to make not only construction but also building maintenance easier – driving down short- and long-term costs. Starting at the design stage, buildings with standard designs and pre-fabricated components are cheaper and faster to build.
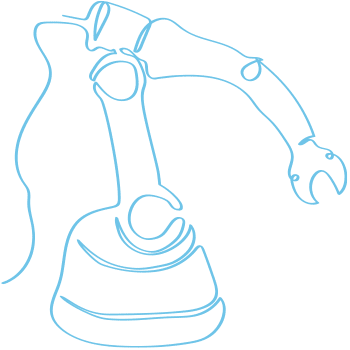
These buildings are highly accurate, with small tolerances. They achieve a high-quality finish throughout any storey level and can be fully planned and documented very quickly. Because they are manufactured, not built, there are reduced weather delays and waste, and carbon generation and site time are reduced. This safer way to build requires only low or semi-skilled labour for fast onsite assembly/installation.
However, this still involves transporting very large components to a construction site, often at high cost.
Case study: A tale of two identical buildings
In 2017, Aurecon designed two nearly identical buildings in two different cities in Asia. Building 1 did not utilise any BIM and pre-fabrication in design and delivery, while Building 2 did. The information regarding the impact on construction is provided below:
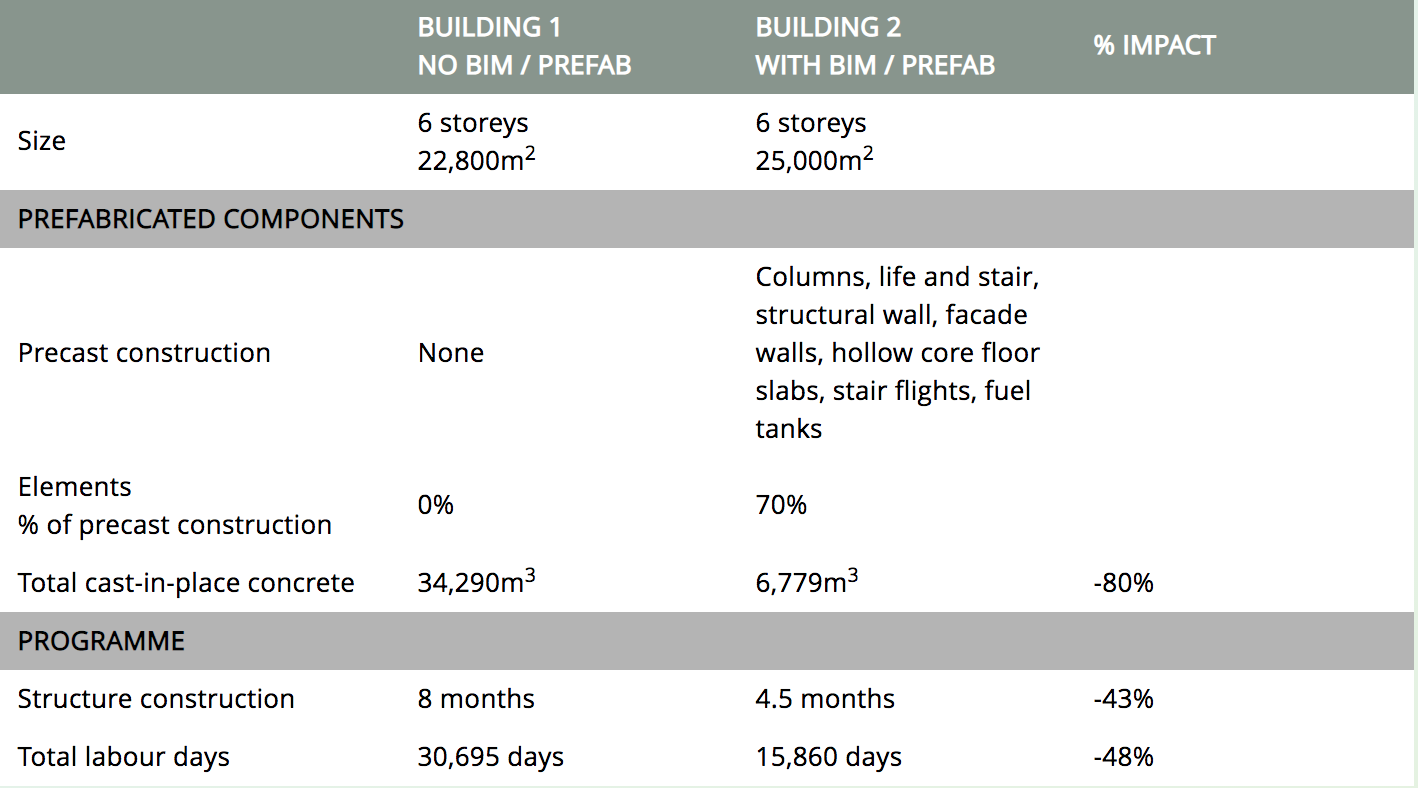
Taking this one step further, construction companies like Katerra and Mace are exploiting opportunities to create factory-like conditions on-site to construct a building in an assembly line manner, using a building platform. As buildings can’t physically move along an assembly line, the idea is to take the ‘assembly line’ to the building site. Standardised, pre-fabricated components are assembled on-site to create a building or precinct, in a Lego-like fashion, as shown in Figure 3.
This form of design and construction is already occurring in cities like Dubai, Tokyo and Singapore where fast population growth is forcing new ways of working to achieve economies of scale.
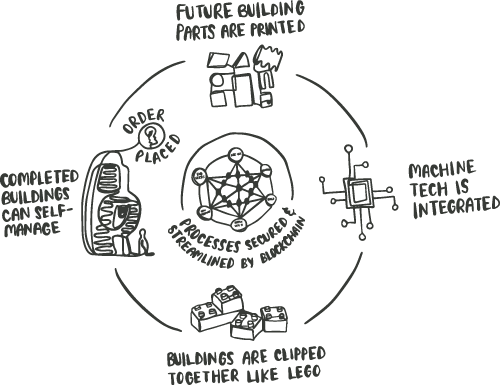
Case study: Are 3D printed buildings the way of the future? Dubai and Saudi Arabia think so...
By 2025, 25 per cent of Dubai’s new buildings will be made using 3D printers. The aim of the 3D-printing strategy is to reduce labour by 70 per cent and cut costs by 90 per cent as well as solve the emerging homelessness crisis.
The city’s fascination with 3D printing in the construction industry was showcased as early as 2016 when the world’s first 3D printed office was created. Only one technician, seven installers and 10 electricians and specialists were required to build the office of the future. Labour costs were reduced by 50 per cent and it took just 17 days to print and two days to install on site. The total cost of the building was USD 140,000. It is now home to the Dubai Future Foundation, which was set up to provide a strategy and showcase for innovative design.
Saudi Arabia is now owner of the world’s largest construction 3D printer, which can design and construct 12x27x9 metre buildings and three storey structures with 300m2 floor plates. As part of its Vision 2030, the Saudi Housing Program aims to deliver more affordable housing in faster time to the majority of its population.
Chapter 2: A step-change needs to occur
How do we create a significant step-change towards industrialised design and construction?
So, with all these efficient design and construction methods already in practice, what else needs to occur and why isn’t it more widespread?
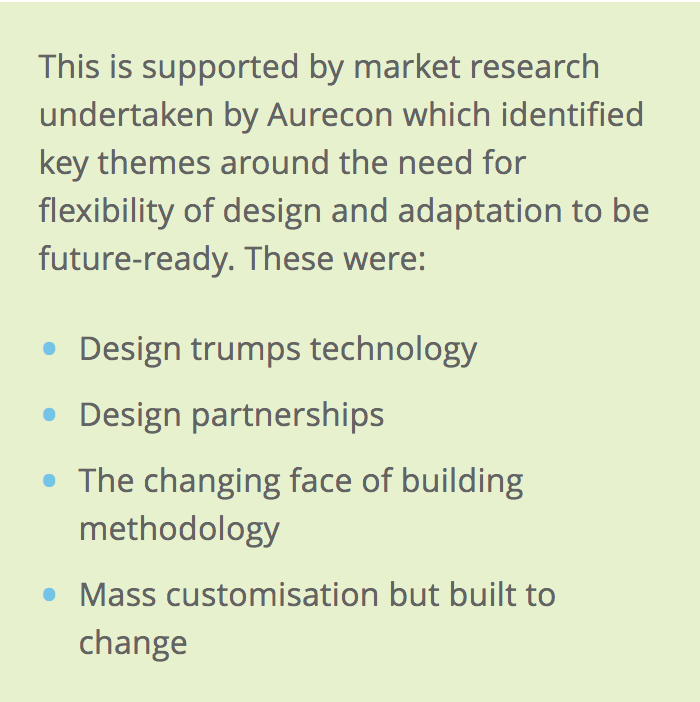
In the World Economic Forum and Boston Consulting paper on the future of construction, six transformation imperatives are identified as being vital for design and construction companies to future-proof their business in this changing environment:
- Recruit new talent and develop required skills
- Integrate and collaborate across infrastructure and urban development industry
- Embrace advanced technologies at a scale that will have significant impact
- Leverage data and digital models
- Review product portfolios and identify new opportunities
- Enable change and adaptation
The benefits of modularisation and industrialised construction
The advantages of modularisation and industrialised construction are well known and documented. In various research reports, including the 2019 McKinsey report Modular construction: From projects to products, these are defined as:
- Reduced construction time by 20–50 per cent
- Potential to reduce costs by 20 per cent
- Increased safety on site
- Increased speed to market which can lead to increased revenue potential
- Ease of construction, particularly in urban and/or congested areas
- Reduced waiting time in sequencing of construction
- Reduced wastage
- Avoids possible delays and quality issues due to weather – the controlled environment of the factory improves precision and certainty. The move to robotics would improve this further.
- Increased certainty and reduction of rework
- Improves opportunity to use alternative materials which would otherwise be difficult to transport to site
- Opportunities for repeatability particularly for buildings that lend themselves to standardisation such as schools and hospitals
- Increased precision in off-site manufacture can decrease lifecycle operating costs. The McKinsey report quotes one client claiming 25 per cent on energy costs after a move to modular construction.
- It can be the best option in areas of high cost employment or lack of skilled site labour and high demand
Modularisation can vary in complexity from 2D elements that require more assembly on-site to 3D (eg. panels) to 3D units that are fully-fitted off-site (eg. fully fitted-out house, including services and finishes). Wood, concrete and steel are used separately or in hybrid.
The less modularised the more design flexibility and ease of transport to site; the more modularised, the more standardisation, repeatability and cost savings.
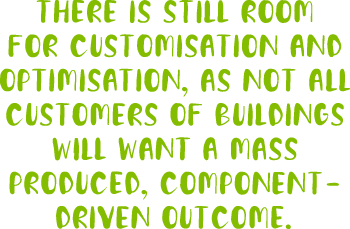
For example, RAD Urban modular supplier is looking to move 85–90 per cent of labour off-site into factories where productivity is higher and costs are cheaper. This could lead to 20–30 per cent cost savings on mid to high rise office developments. The move to automation is next with a predicted 10x efficiency gain.
While a move towards a manufacturing-style approach to design and construction of buildings is an imperative for sustainable growth, and is already occurring, there is still room for customisation and optimisation, as not all customers of buildings will want a mass produced, component-driven outcome.
Technology is allowing for the transition from an environment where work is a craft and can only be done by ‘professionals’ to a use of standardisation and prescriptive solutions, to systemisation which is a situation where the ‘craft’ work is actually done by technology, and professionals are the gate keeper between the public and the knowledge. This is described by Richard and Daniel Susskind, in their book, The Future of the Professions.
So, with all these benefits, why isn’t modularisation, off-site and industrialised design and construction occurring more broadly across more markets and regions, and at a faster pace?
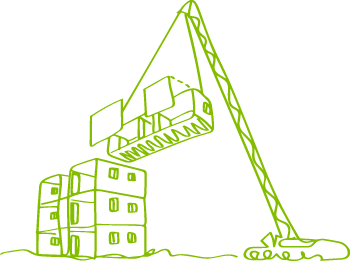
Why isn't change occurring more broadly and faster?
In their full report, Modular construction: From projects to products, McKinsey identifies seven factors influencing modular construction, as shown in Figure 4:
- Labour shortages
- Ability to service demand
- Regulation
- Access to materials
- Supply chain and logistics
- Quality perception
- Local site constraints
Without these factors, modularised construction may not meet the economic goals of companies and jurisdictions and the needs of consumers.
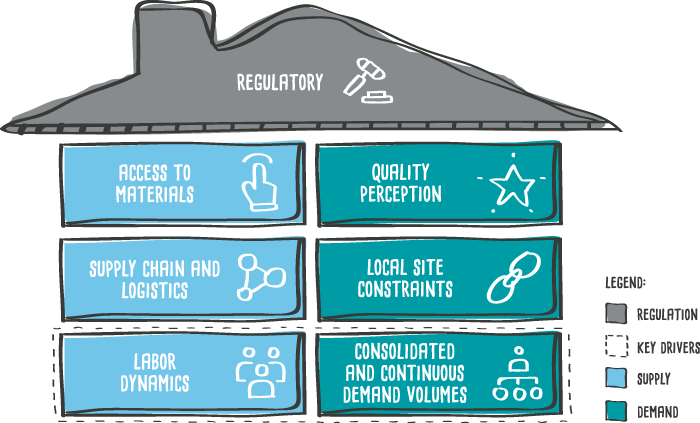
The McKinsey report emphasises that all participants will need to change to create a significant impact. These include:
- Manufacturers – modularisation will need to scale and optimise
- Developers and investors – will need to understand options for productisation and investment opportunities, and choose industry partners
- Materials suppliers – will need to shift products to more repeatable components with an efficient ‘go to market’ strategy
- Public sector – opportunity to bundle projects and may need to look at changing building codes
- Engineering and construction firms – will need to understand what commoditisation will mean for the industry and make decisions about where they will ‘play’
Richard and Daniel Susskind, in their book, The Future of the Professions, argue that the final stage of significant change and innovation is externalisation when access to the technology is available to the general public without the gatekeeper being needed, as shown in Figure 5.
A simple example of this is the travel industry where the use of a travel agent is now optional and not used by the majority of the public. To what extent could this happen in design and construction? Could the general public design and 3D print their own homes or offices based on standardised components?
While commoditisation and standardisation can be valid in many situations, there is little scope for differentiation. We shouldn’t ignore opportunities for customisation and optimisation. Designers can start to create ‘customised’ modular libraries to help decrease time and cost of design and move towards more ‘design for manufacture’ approach, but this won’t be suitable for every situation.
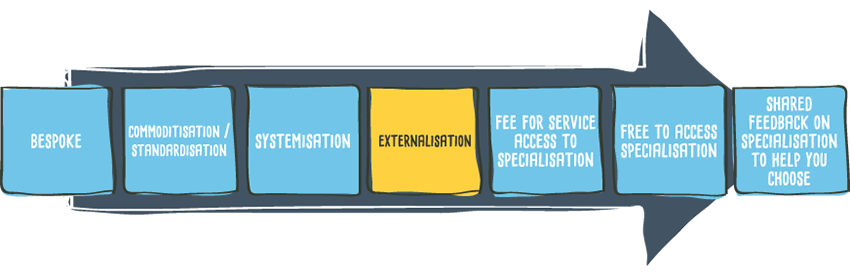
What needs to be true for change to occur?
There are some concerns that increased modularisation, robotics and automation, as well as a move to niche customisation and optimisation, will lead to job losses for traditionally-skilled construction labour and professionals undertaking work which can now be undertaken more efficiently by robots. This will no doubt be the case, but the accompanying increases in productivity, combined with ongoing increasing demand, could mean that more projects could be designed and built, hence labour will still be required.
As Christensen espoused in his theory of disruptive innovation, change needs to occur at the bottom of the market, typically with a new entrant offering a significantly lower cost alternative to the masses. He continued that the focus should be on ‘the job that needs to be done’, rather than the product or service itself. Applied to design and construction, this means that a house, office, school or hospital, need to fulfil the need of the customer to live, work, be educated or receive healthcare, as opposed to be objects of high design value.
So, what precedents need to exist for significant change to occur in the design and construction of buildings?
If we look at history, disruptive innovations have occurred when:
- There is a burning platform for change eg. the post-war construction of housing estates in the UK and Europe to cater for thousands of displaced citizens or the current global trends of population increases and urbanisation
- Affordability has become an issue for the majority so a significant customer base is ripe for a disruptive product or service – as in the case of automobile ownership in the early 20th century or ridesharing in the 21st century
- New technologies are enabling change – for example 3D design, 3D printing and ‘on-site factories’
- New materials are creating opportunities – such as the emergence of mass engineered timber (MET) and precast concrete which are enabling off-site, modularised construction of standardised components
- Supply chains are aligned to enable ease of delivery of components to create cost-effective and fast manufacture, as achieved by Henry Ford with his optimised assembly lines
Where these factors converge, innovation will occur. This may mean that the significant step-change required for more efficient and cost-effective design and construction to gain momentum, may occur in situations such as regions where housing is at a crisis point, and inexpensive, and fast construction could make a significant difference, for example in emerging economies or countries devastated by natural or man-made disasters such as tsunamis, earthquakes, war, or as we have seen in China where a hospital was constructed in 10 days, due to the coronavirus outbreak.
It will be necessary to develop clear protocols for when commoditisation and standardisation are appropriate – that is, buildings that have low design value and can benefit from repeatability. This may represent the bulk of the ‘new world’ of design and construction. This will still enable customisation and optimisation to flourish – this is appropriate for buildings with high design values and that require customisation for differentiation. Design and construction firms will gravitate to one of the two extremes as well as some sitting across both, as shown in Figure 6.
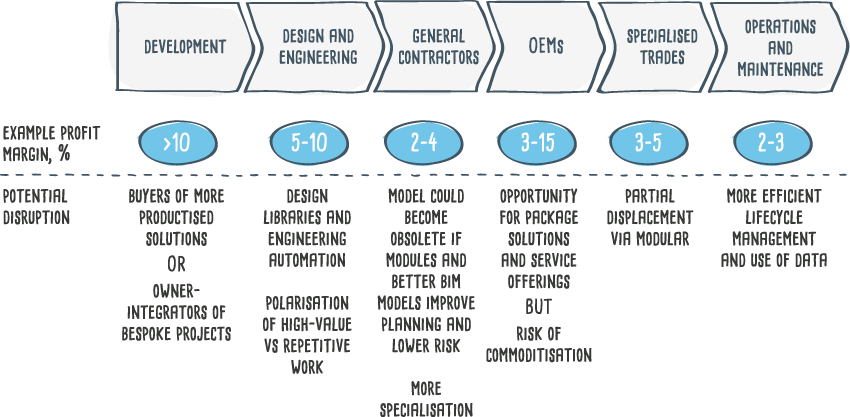
Ultimately, someone, or something, needs to emerge, as did Uber and Airbnb in the transportation and travel industries, and Henry Ford before them, to disrupt design and construction in a way that will change the landscape forever.
Designers and developers will need to assess options and priorities in terms of appropriateness of approach, cost, time, location and differentiation, as demonstrated in Figure 7.
Once the options are understood informed decisions can be made about how to move forward with a project. It will be necessary to consider all aspects of a project from design, through supply chain and construction to operation, to decide the best approach, and ensure the most appropriate team to design and deliver a project.
For example, Japan and Sweden have made significant inroads into modular construction due to many factors, including quality of build and resistance to seismic activity (Japan) and short daylight hours for on-site construction (Sweden). The US and UK have utilised off-site construction after major wars when speed of construction was an imperative, but this has since waned.
As McKinsey suggests, it may be time to revisit this approach now due to advances in technology which has made digital design and many automated processes ideal for fast, efficient design and construction.

Case study: Aurecon's data centre configurator
Aurecon conducted a Data Centre Development Sprint, bringing together programmers, data centre specialists, designers and leaders across the Aurecon business to create a configurator to enable fast and efficient automated design of a data centre.
This prototype is currently being tested with clients.
Chapter 4: What other questions should we be asking?
What about the ethics? While industrialised construction and the increasing use of automation and robotics to build our communities of the future, is a more efficient, cost effective, faster, safer and practical move forward, what about the ethics of a displaced workforce?
Where will the site labour of yesterday and today fit into the automated construction world of tomorrow?
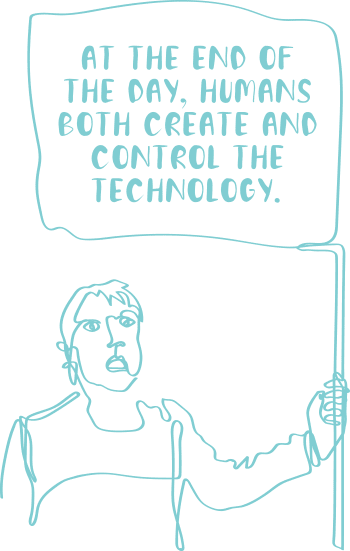
In a paper presented at the MIT Technology’s Review EmTech Next Conference, the Vice Chancellor for Research at the University of California, Pramod Khargonekar, and Associate Vice Chancellor for Research at the State University of New York, Meera Sampath, address this issue.
Entitled Socially Responsible Automation – A Framework for Shaping the Future, they identified four levels of progress towards automation:
- Level 0 – cost-focused automation where technology is used solely for financial benefit
- Level 1 – performance-driven automation where technology is often used to do the ‘heavy lifting’ with humans still required to provide skills to fill in the gaps
- Level 2 – worker-centred automation where the business goals are both worker development and performance optimisation
- Level 3 – socially responsible automation where automation is use to drive improved opportunities for humans
Will our unique human 'craft' skills be lost?
A 2017 study by Gartner Research predicted that while 1.8 million jobs would be lost worldwide by 2020 due to automation, 2.3 million new jobs would be created. As history has taught us, any new processes or transformations result in temporary job losses, followed by a readjustment as new opportunities emerge, and researchers believe that automation, particularly when combined with the human skills required to drive new technology, will be no different.
The key is upskilling and job enrichment. As machines increasingly take over low-level, mundane and heavy-lift tasks, humans will be required to hone their skills even further, developing new, smarter ways of working.
While it might mean that robots take over some of the traditional ‘crafts’ we have seen in construction, such as carpentry, bricklaying and electrical wiring, skills in programming, coding, detailing, customising and optimising will come to the fore.
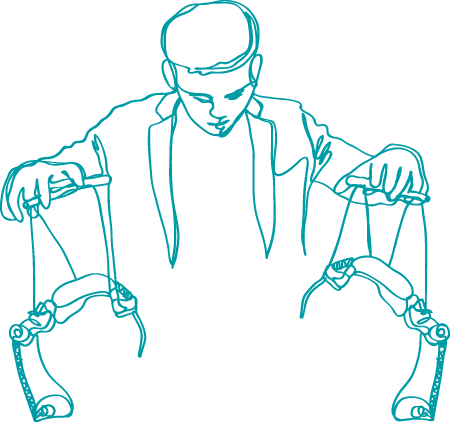
What should we be asking?
- What needs to change in the current design process to allow the wider adoption of industrialised construction?
- How can the digital documentation the design industry produces be enhanced?
- How will industrialised construction create a place of belonging in cities and communities?
- What new business models will be required for industrialised construction to accelerate?
- How do industrialised construction and design flair co-exist?
- Do we need to integrate more technology into the process to enable it to scale?
- Is there a place for a hybrid version of industrialised construction in the industry?
Conclusion
There is a burning platform for change in the design and construction of our built environments. Increasing urban populations, rising demand for residential, commercial, social and public buildings, escalating costs and declining profits, means a step-change needs to occur to create a democratic and sustainable sector for the future.
While prefabrication, modularisation and industrialised design and construction in general is occurring in pockets around the world and has been for decades, it is not occurring broadly, and not at a fast-enough pace for significant change.
Drawing on Christensen’s theory of disruptive innovation, the time is ripe for a new entrant to emerge at the bottom of the market, creating a maelstrom of change akin to what Henry Ford achieved with the car industry in the early 1900s and Uber and Airbnb have delivered to transportation and travel in the 21st century.
Low cost, commoditised products available to many through construction robotics and 3D printing systems, with minimum human interface on the actual construction site, is the only way in which we will meet the global need for buildings of the future. New processes, technologies and materials are enablers already in place to assist with this transformation.
All that is now required is a mindset and behaviour shift of designers, developers, owners, suppliers, governments and endusers, towards a new breed of buildings that are built by robots, standardised, commoditised and affordable. While not likely to cater to all, there will still be room for customisation and optimisation. Questions of ethics and craft will also need to be addressed, to ensure a smooth transition. The gains will need to be greater than the losses, for customers to make the shift.
But as Christensen points out, the ‘job that needs to be done’, in this case, hiring an affordable and functional building to provide a house, office, university or healthcare facility is a far more relevant opportunity for widespread innovation than merely tweaking an existing product or service hoping to meet ongoing customer demand.
The buildings of the future may arrive on-site via a 3D printer in a factory or may in fact be assembled in-situ by robotic processes.
They may take weeks rather than months or years to be constructed, and their cost may be a tenth of what they are today. Entire communities could be assembled cheaply and quickly, providing homes and public buildings for currently homeless populations, or at least those for whom home ownership is beyond their reach. On the other end of the scale, high-end buildings featuring customised designs could still be available for those with the means to purchase them.
There is a lot for us to consider - we don’t have all the answers now, but as long as we keep asking the right questions, solutions will eventually emerge.
This article first appeared here: https://www.aurecongroup.com/markets/property/buildings-of-the-future/productised-building-design