Australia’s First Double Helix Bridge Opens in Sydney
Australia’s first double-helix bridge has opened in Sydney’s North Ryde.
The 170-metre steel bridge connects pedestrians from Landcom’s new 5,000-resident Lachlan’s Line development to North Ryde Metro Station by spanning across both the M2 Motorway and Delhi Road.
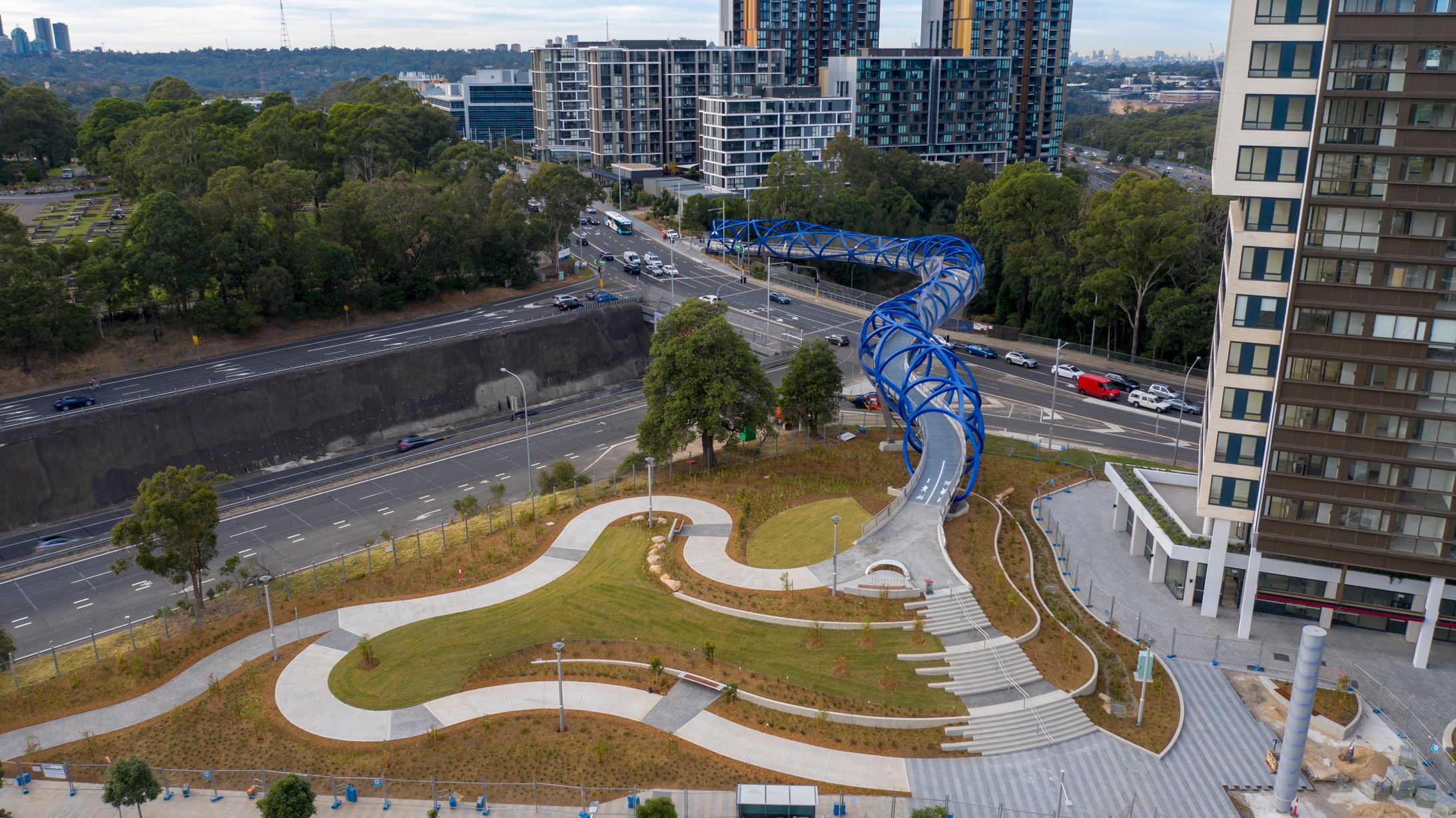
At a price tag of $40 million, the bridge was delivered by a joint venture between Daracon Group and Arenco with engineering design by Arup.
It’s the first double helix bridge in the world to have a dilating diameter - getting larger over the supports (where bending moments are higher) and narrower midspan (where moments are lower).
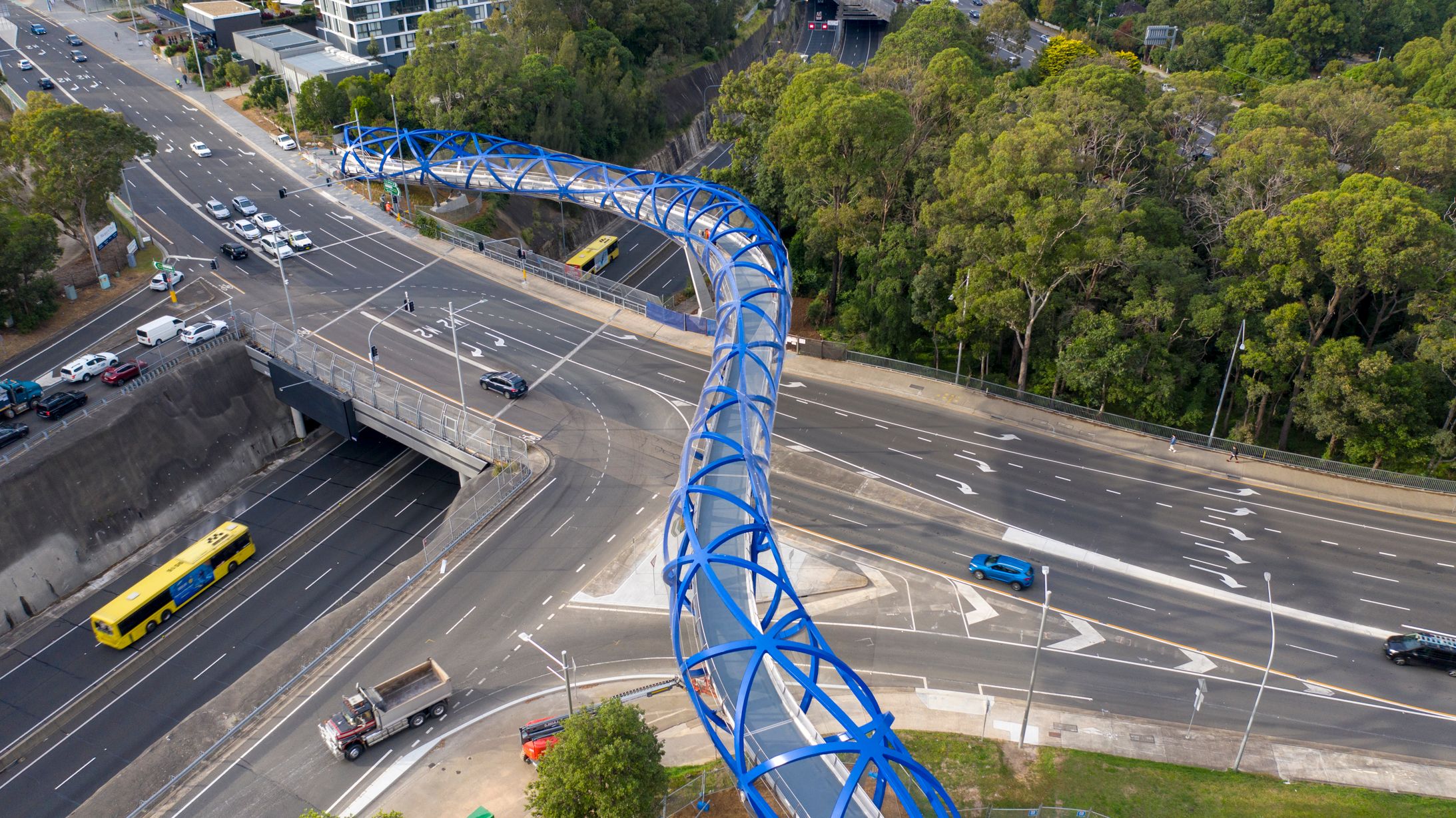
What’s great about this bridge is that its pleasing curves and unique features weren’t done just to look good, but out of necessity.
“The double helix and sinuous design was actually derived from the structural parameters, not primarily for aesthetics as it may first appear,” says Andrew Johnson, Principal and Project Director at Arup.
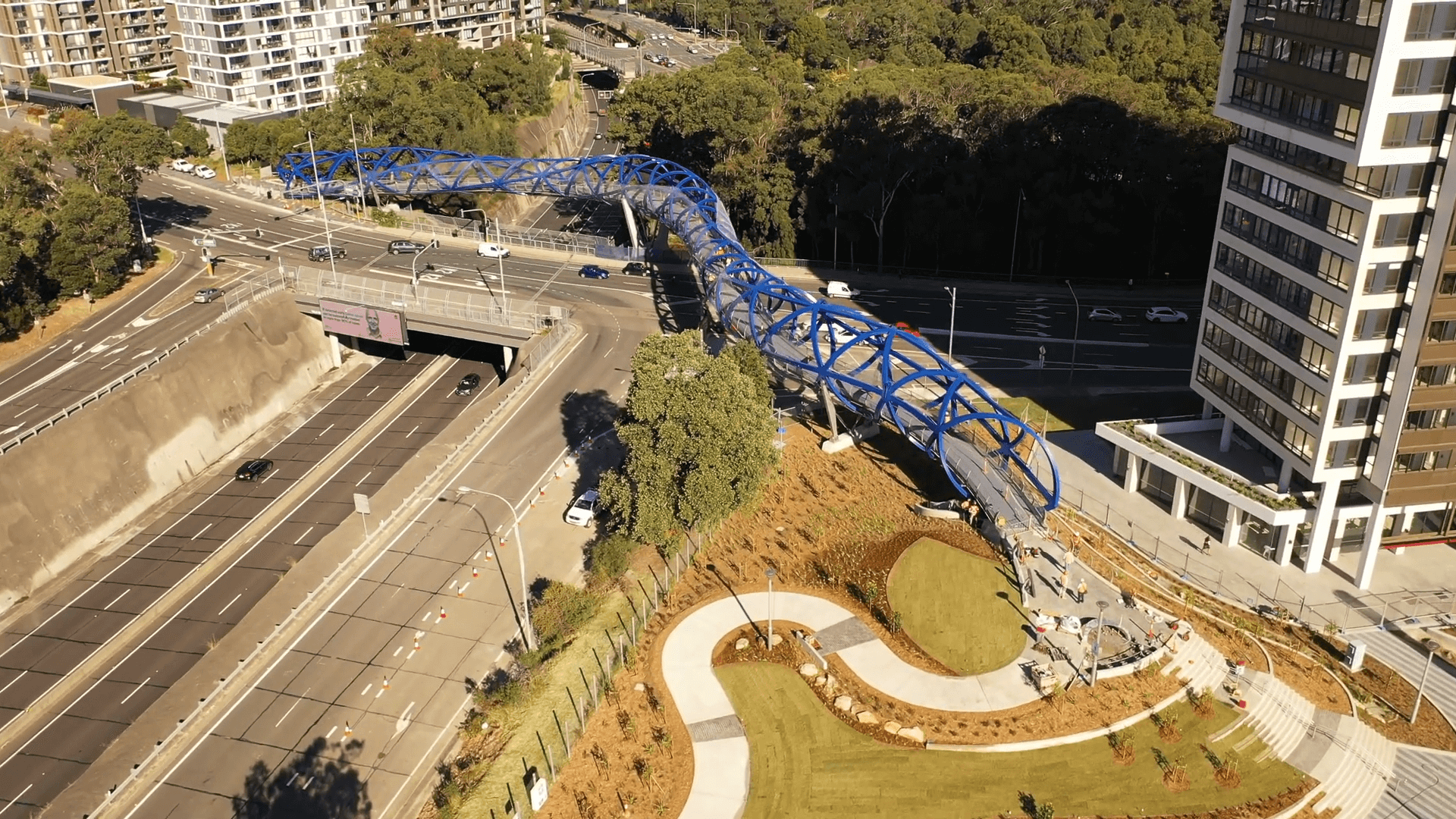
The curved formation you see on the bridge now was derived from the shortest spans possible.
The bridge geometry was always going to be complex. It needed to span 2 roads with limited free land space for the bridge entry points and piers. That almost made this bridge a non-starter. Many said it couldn’t be done.
But Johnson and the team, including structural engineer Xavier Nuttall, saw this complex set of design parameters as a challenge, not a showstopper.
“We had to be tenacious in our belief that it could be done,” says Nuttall.
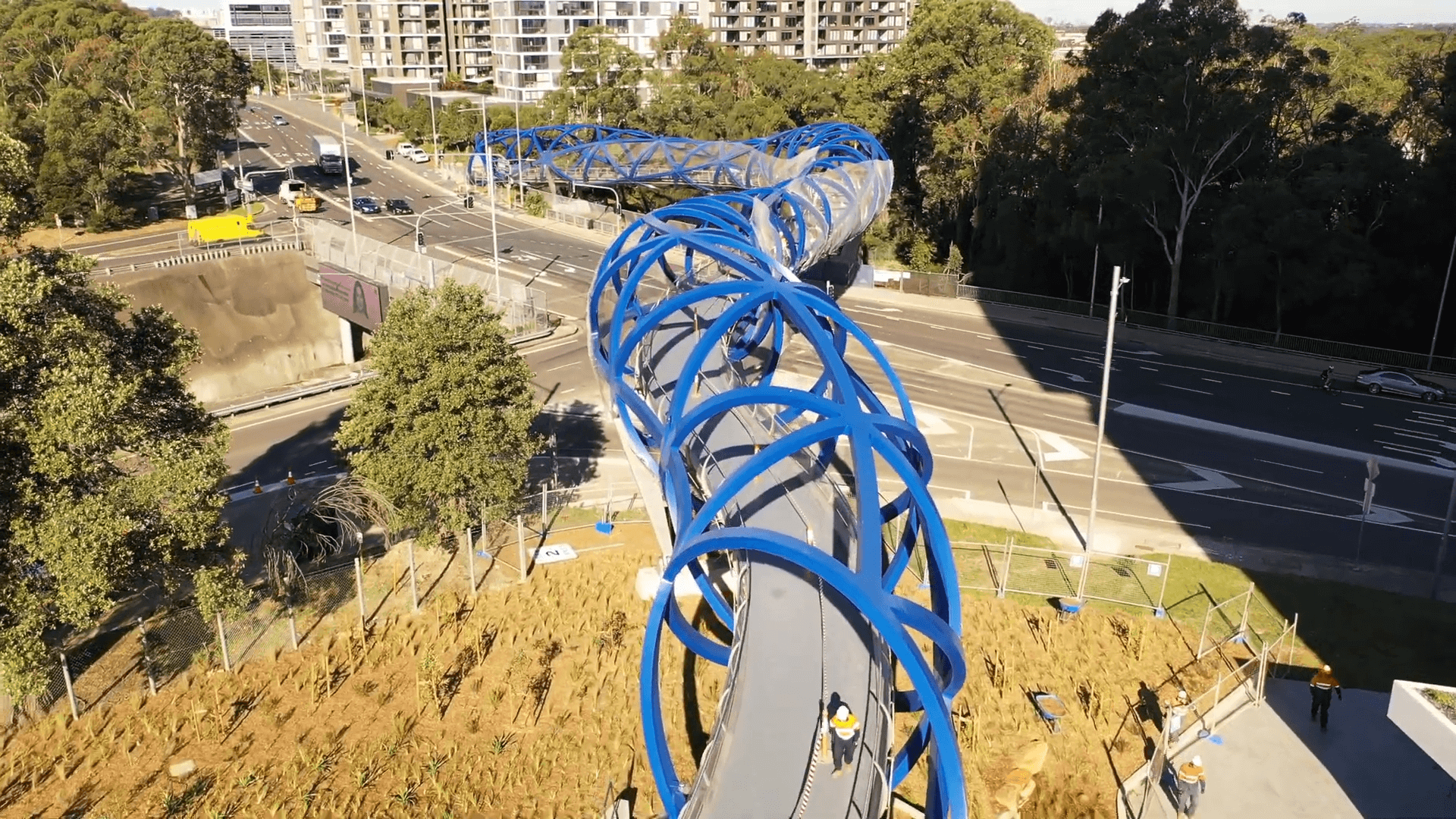
To make things easier and allow for quick design changes, the team developed a parametric modelling workflow using industry software augmented by Arup’s own internal programming and analysis software. This digital workflow allowed a change in one aspect of the design to automatically update the rest of the design to suit.
The steel double helix was chosen by Arup for its high torsional strength to accommodate the spans - the longest being 70 m over the M2.
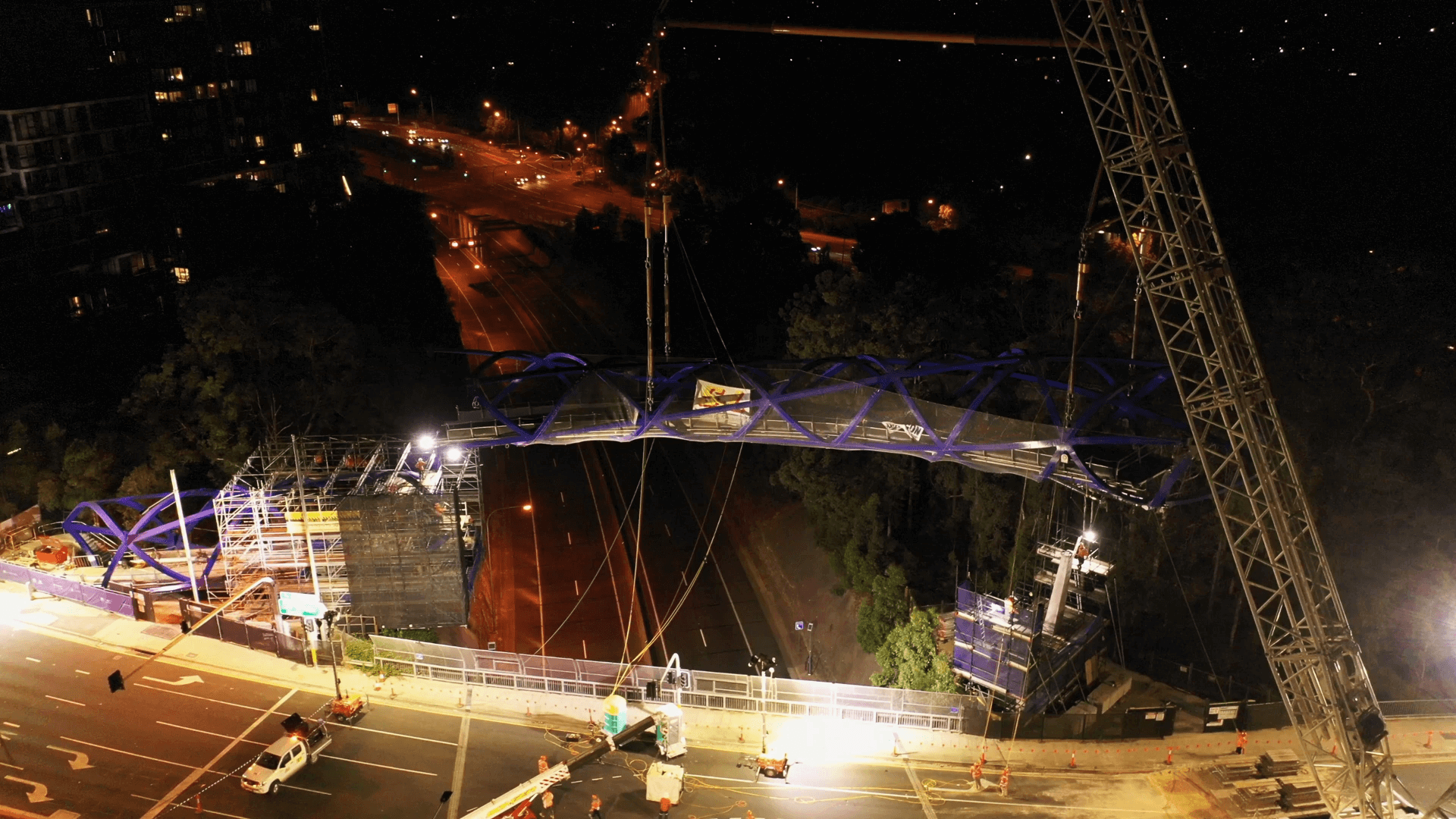
The use of hollow box sections (also a world first), allowed optimisation of the plate thickness which wouldn’t be possible with a tube section. Each plate varies in thickness depending on structural demand.
This means the steel plates are no thicker than they need to be at any point, reducing steel consumption and dead weight in the structure.
Of all the 3,600 steel plates used to fabricate the 335-tonne structure, no two are the same. This made for a complex fabrication project for Glendenning-based steel fabricator, S&L Steel.
A 1:5 prototype was produced to make sure the design wasn’t just theoretically possible, but physically viable. Then, a trial assembly was undertaken off-site before being dismantled, trucked to site and erected in 4 separate spans using a 500t crawler crane from Delhi Road.
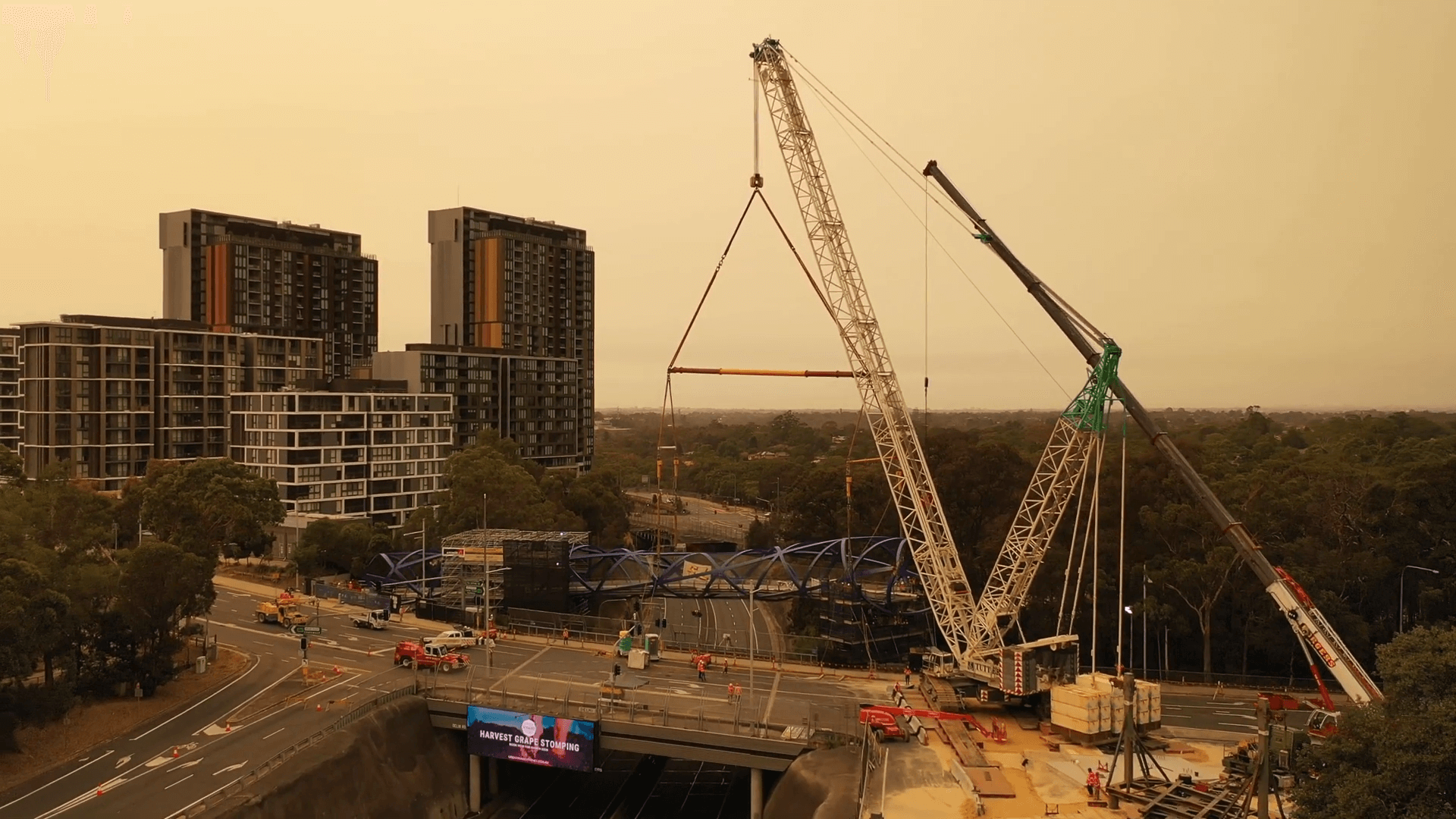
Designed in conjunction with urban design and landscape architecture firm KI Studio, this bridge truly has a user experience like no other in Sydney. It draws you in and encapsulates you as it gently curves its way over one of the busiest intersections in Sydney.
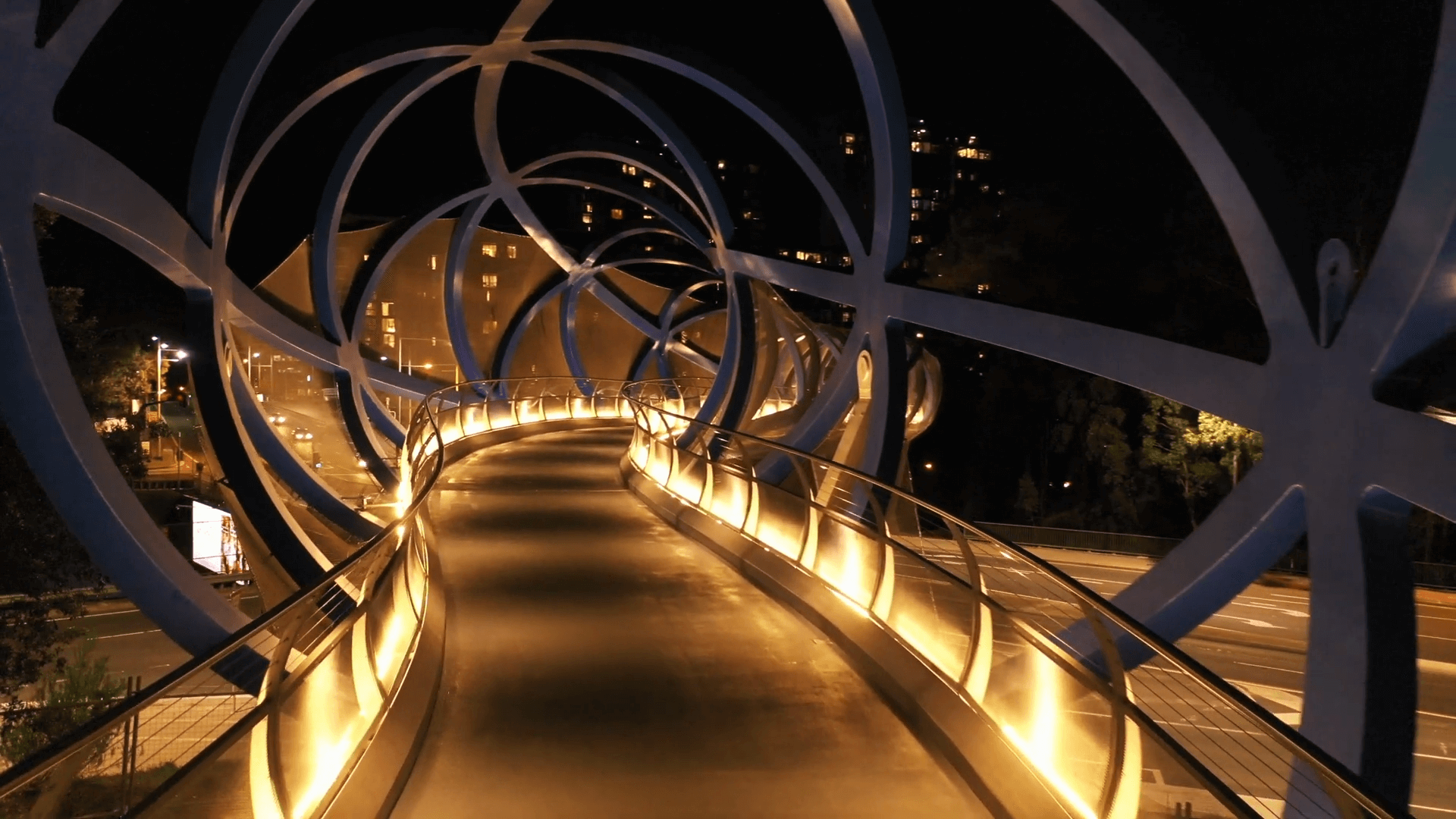
“There were lots of times we asked ourselves whether it was worth it”, laughs Johnson, “but in the end it looks like it fits. The bridge feels natural and complements the landscape whilst being functional, unique and elegant.”
It’s not very often that a pedestrian bridge reminds us that engineering is in fact an art form afterall.
You can read more on the design of the bridge at Arup’s website.
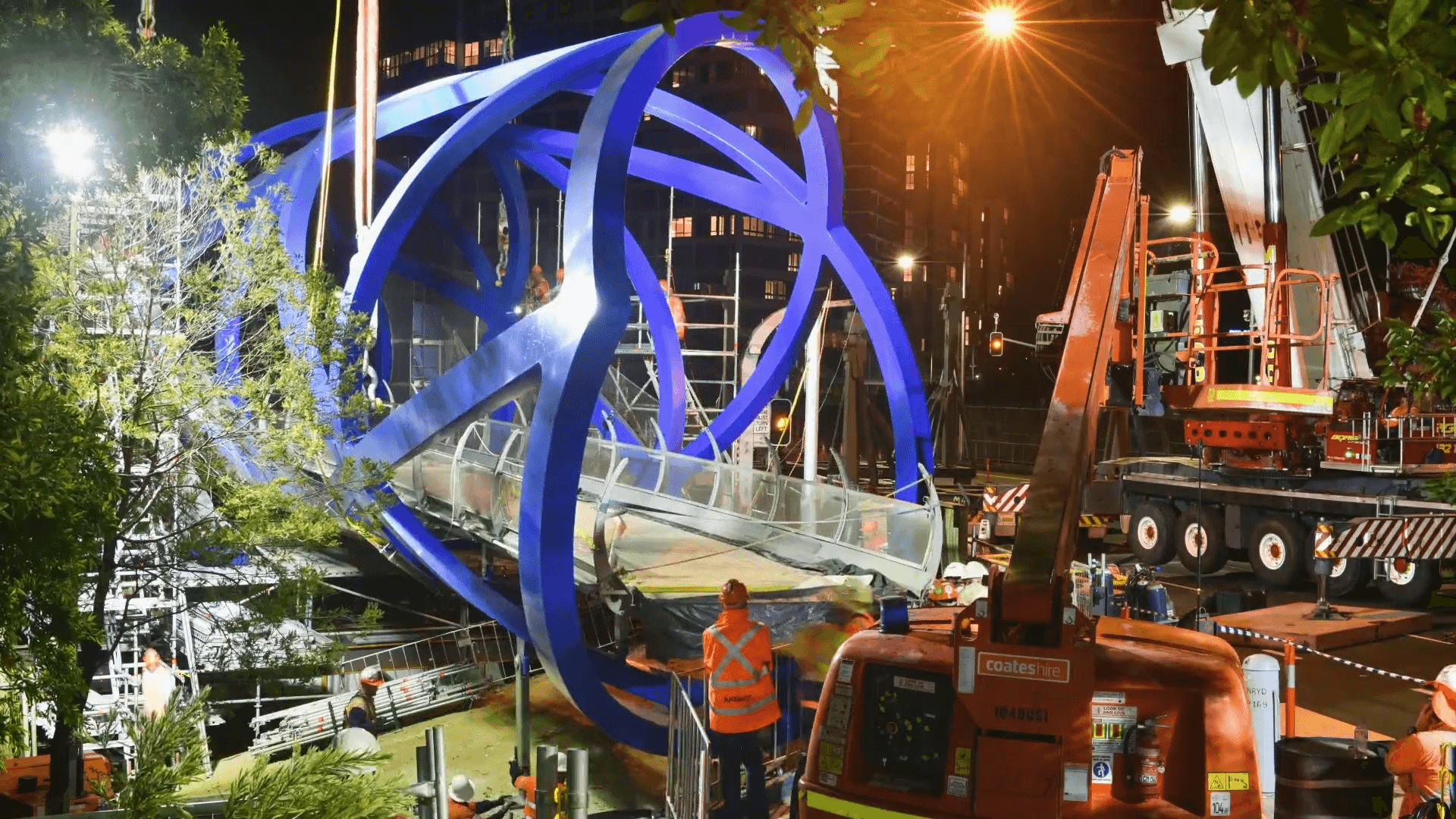
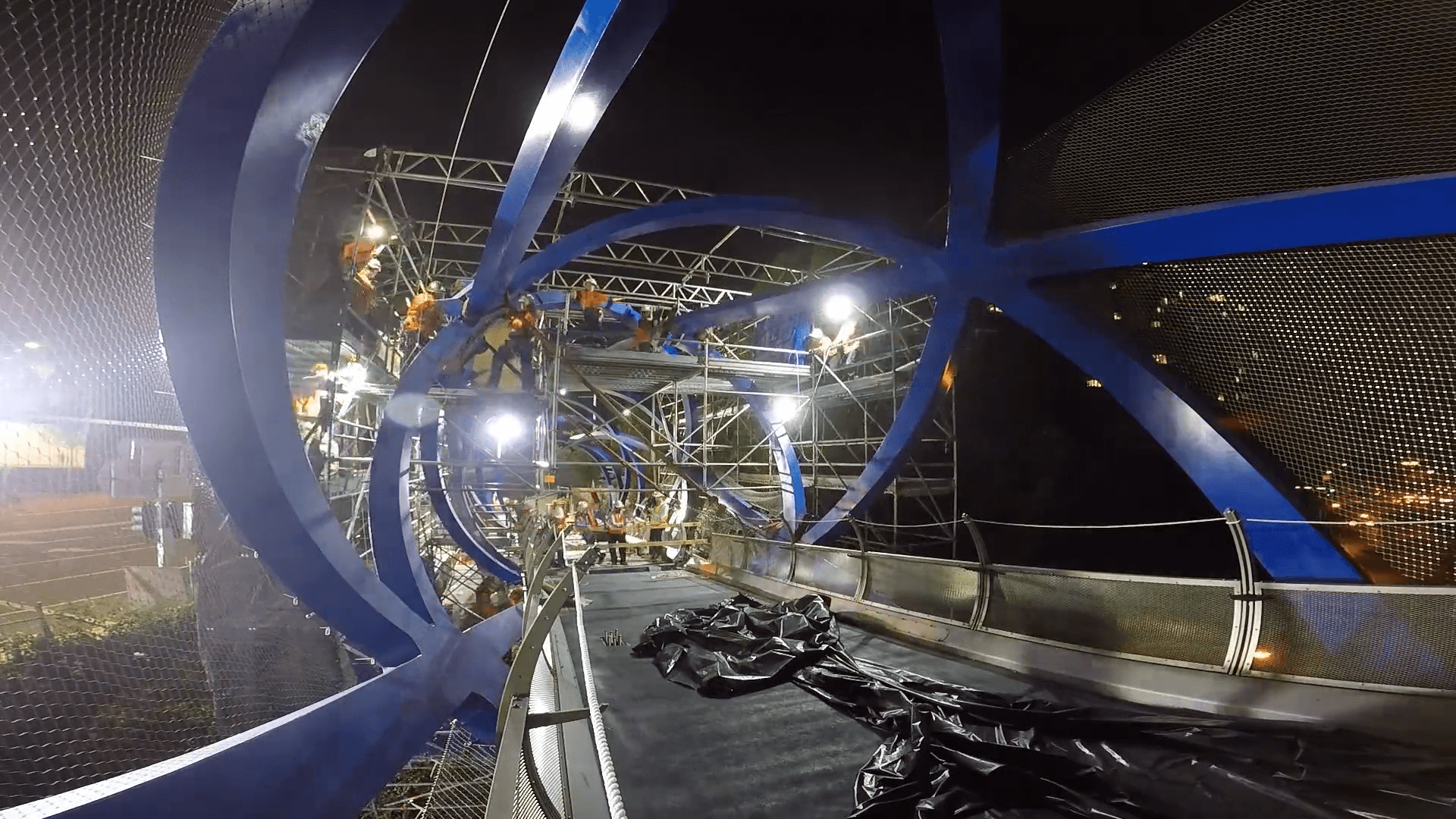

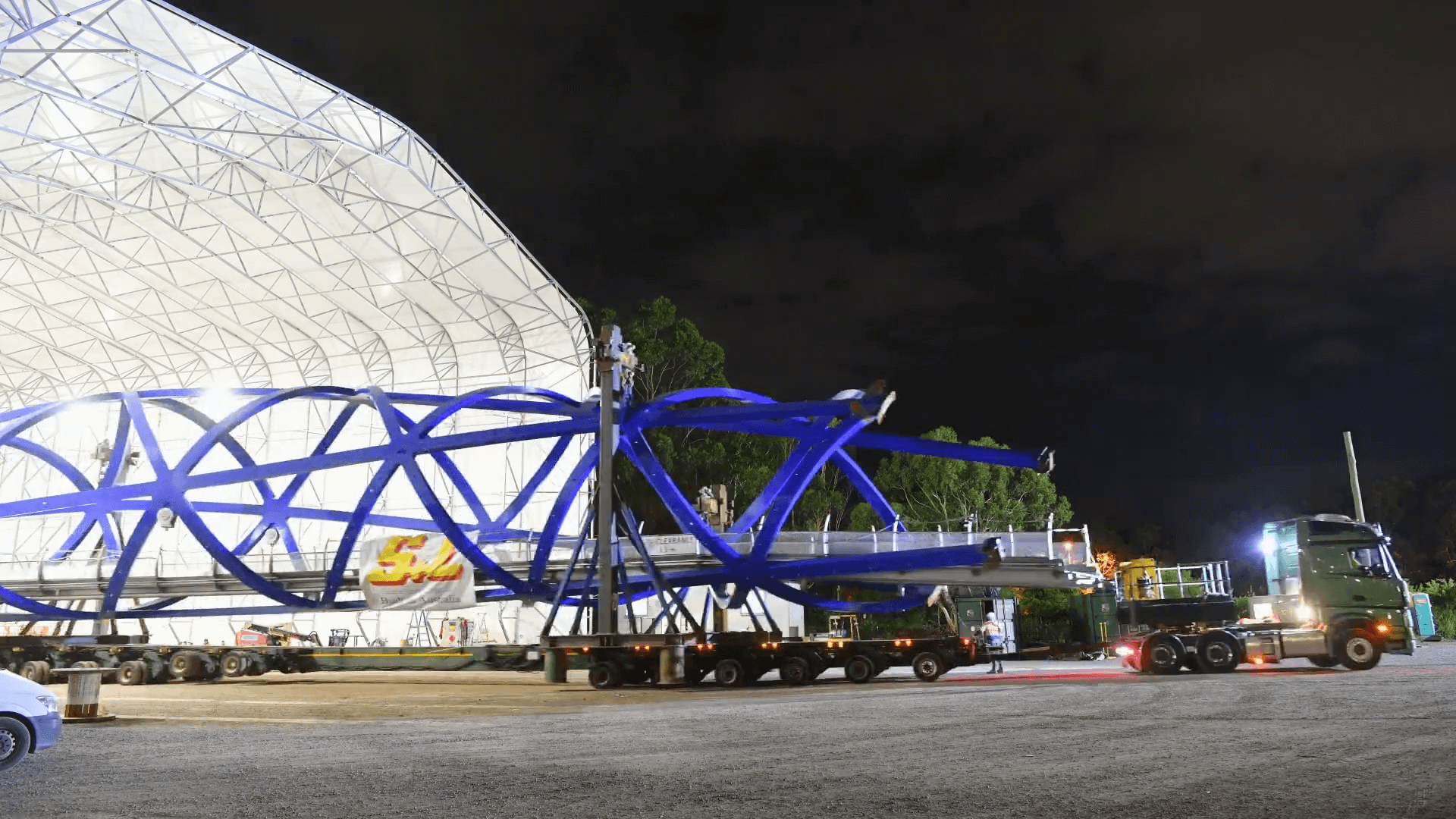
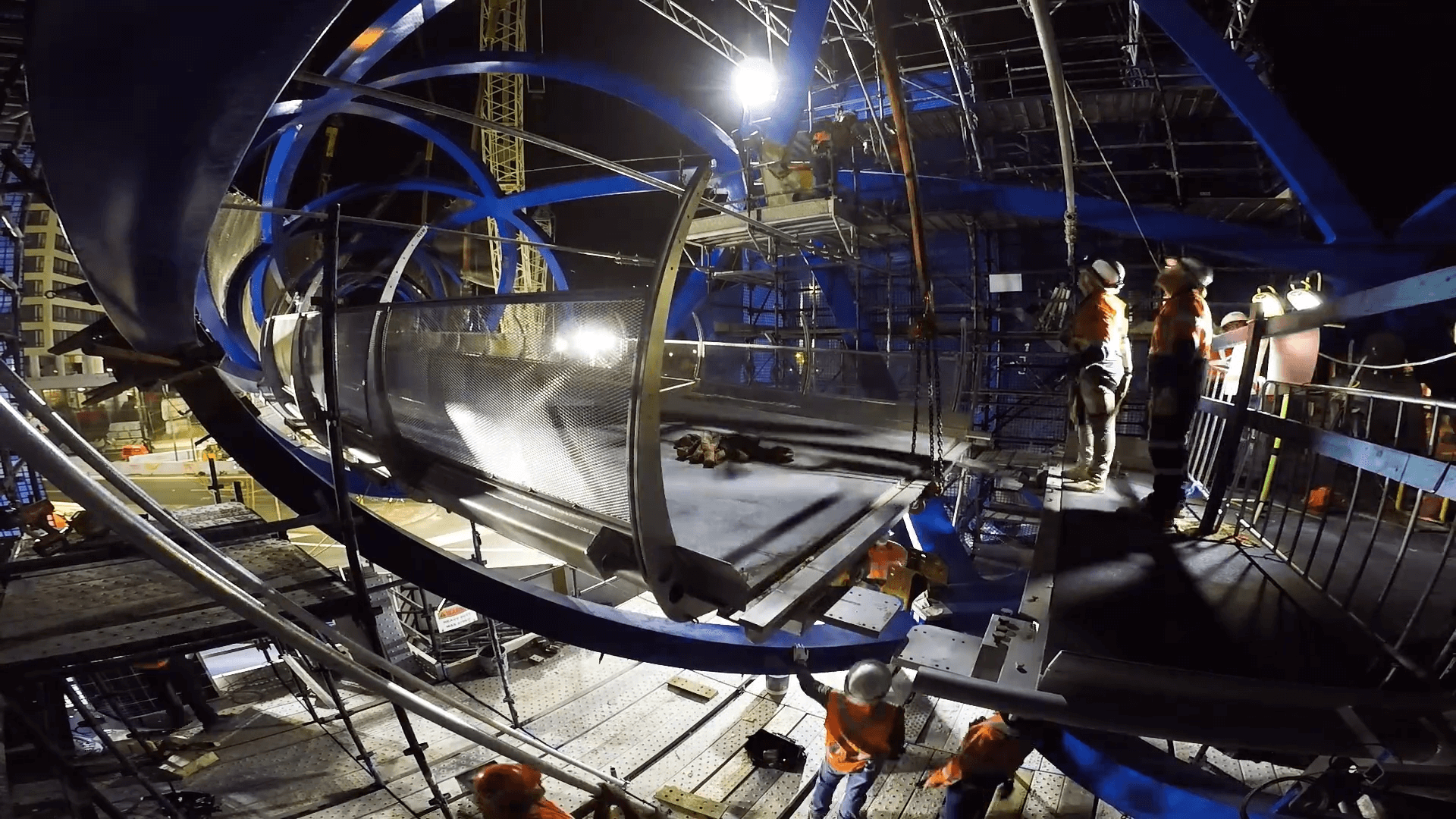
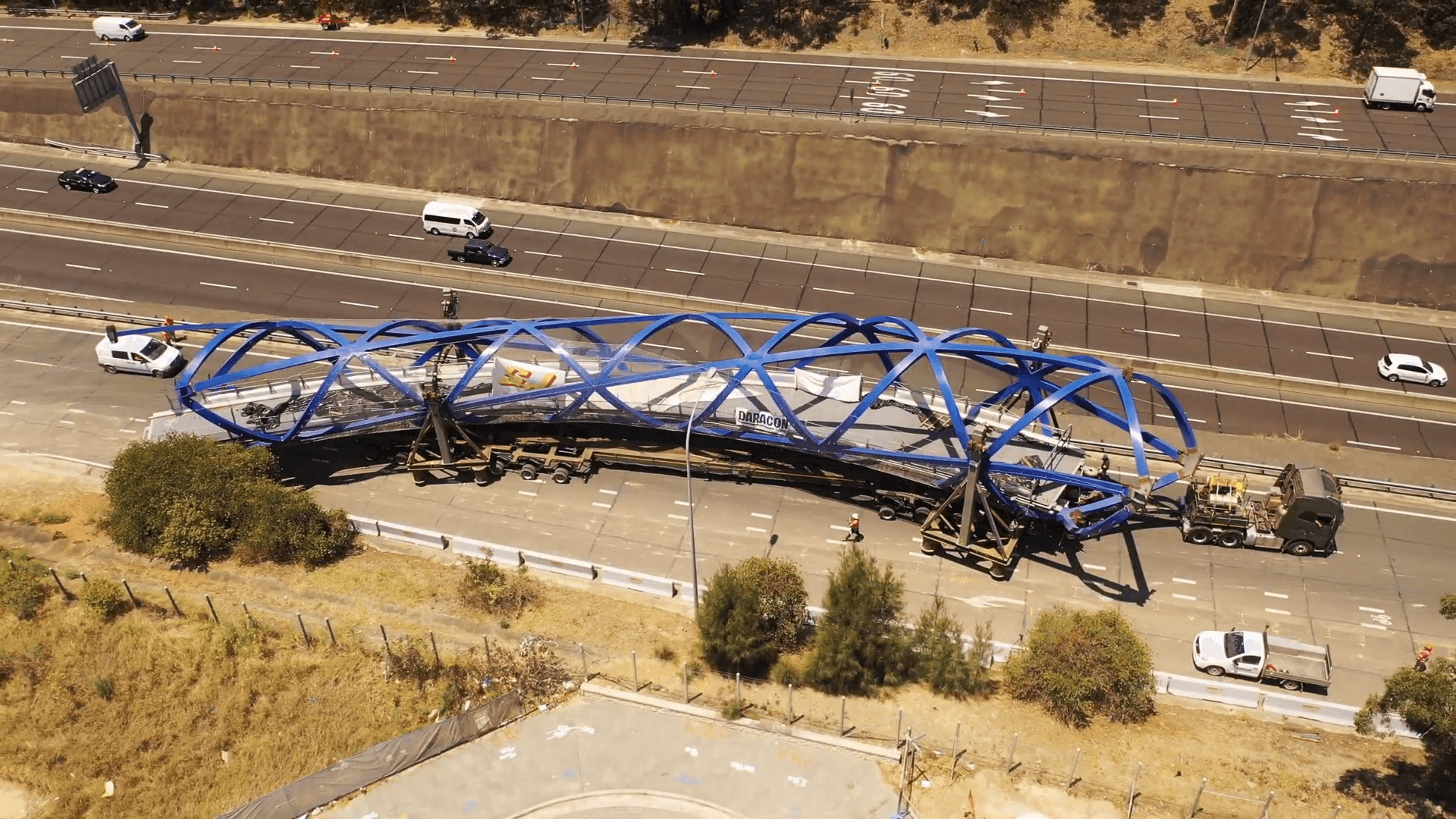
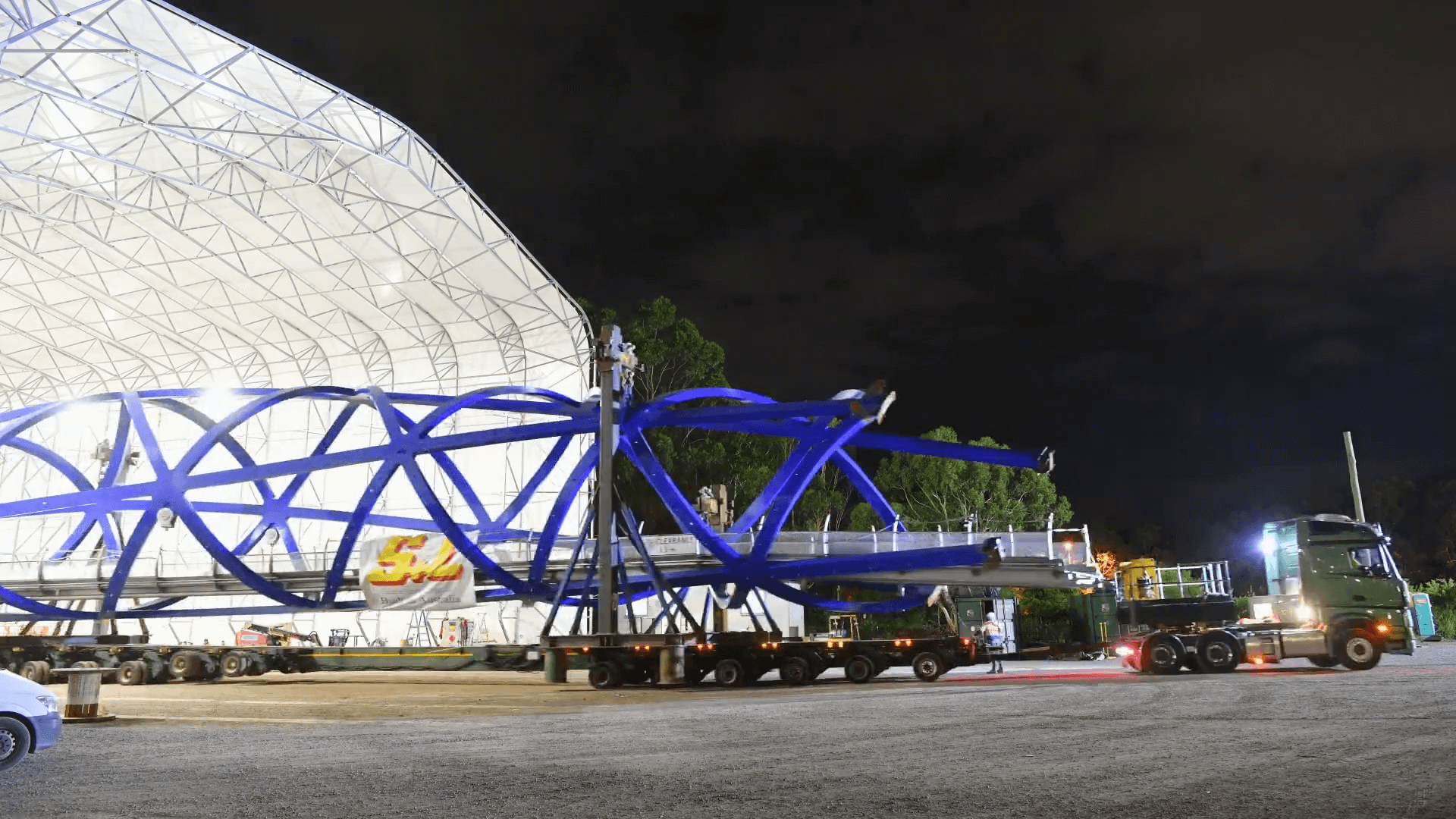
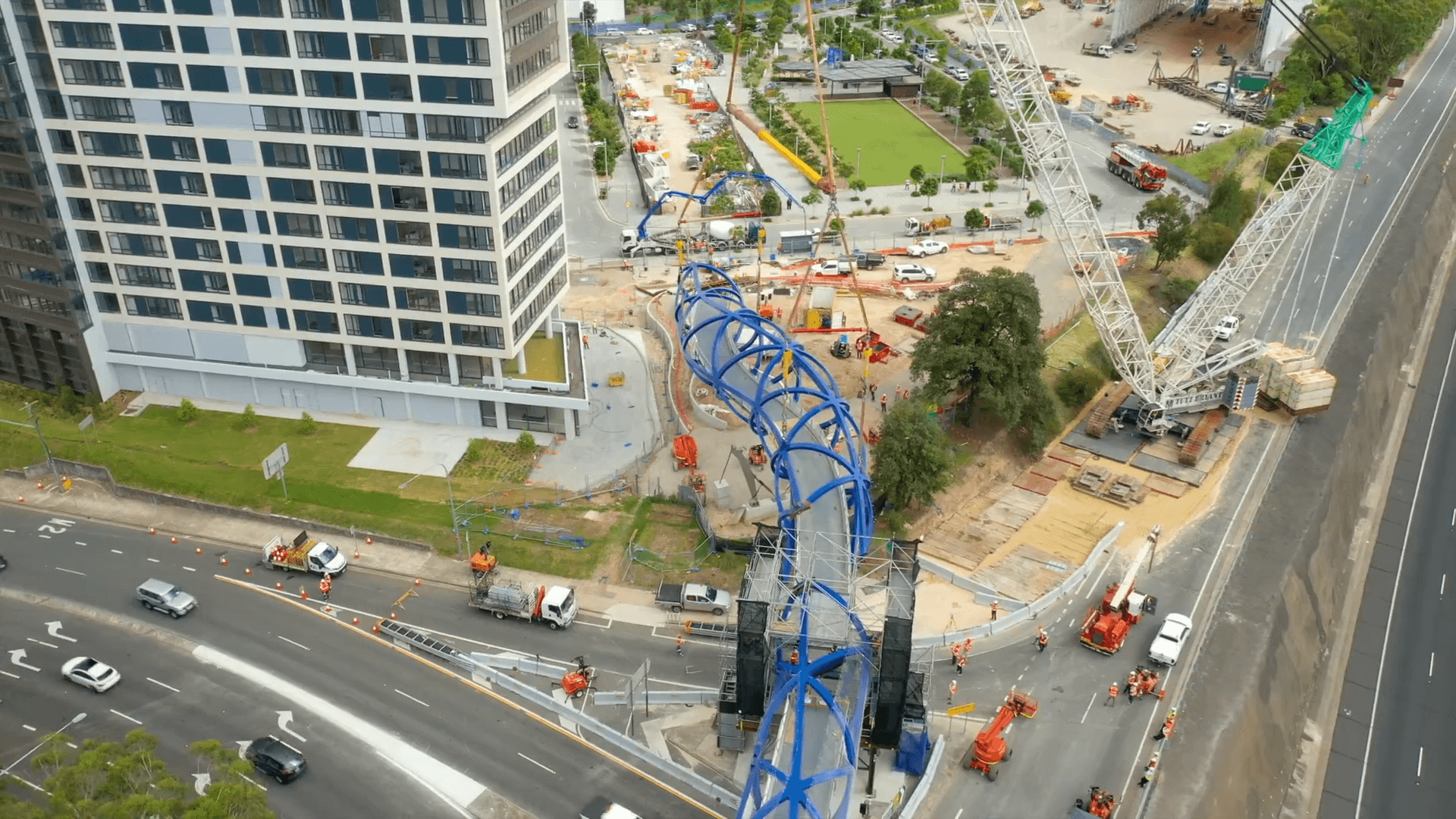
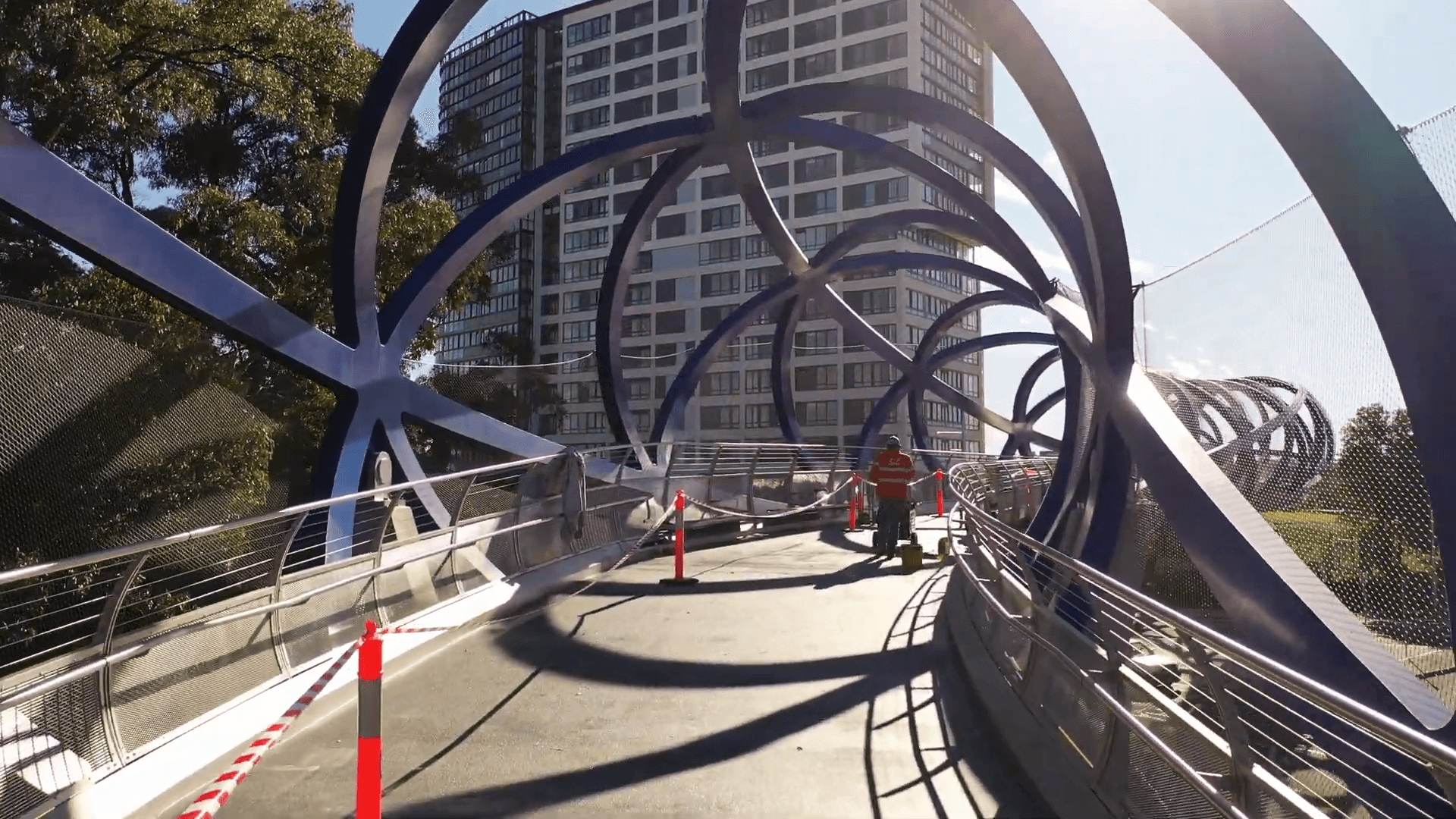
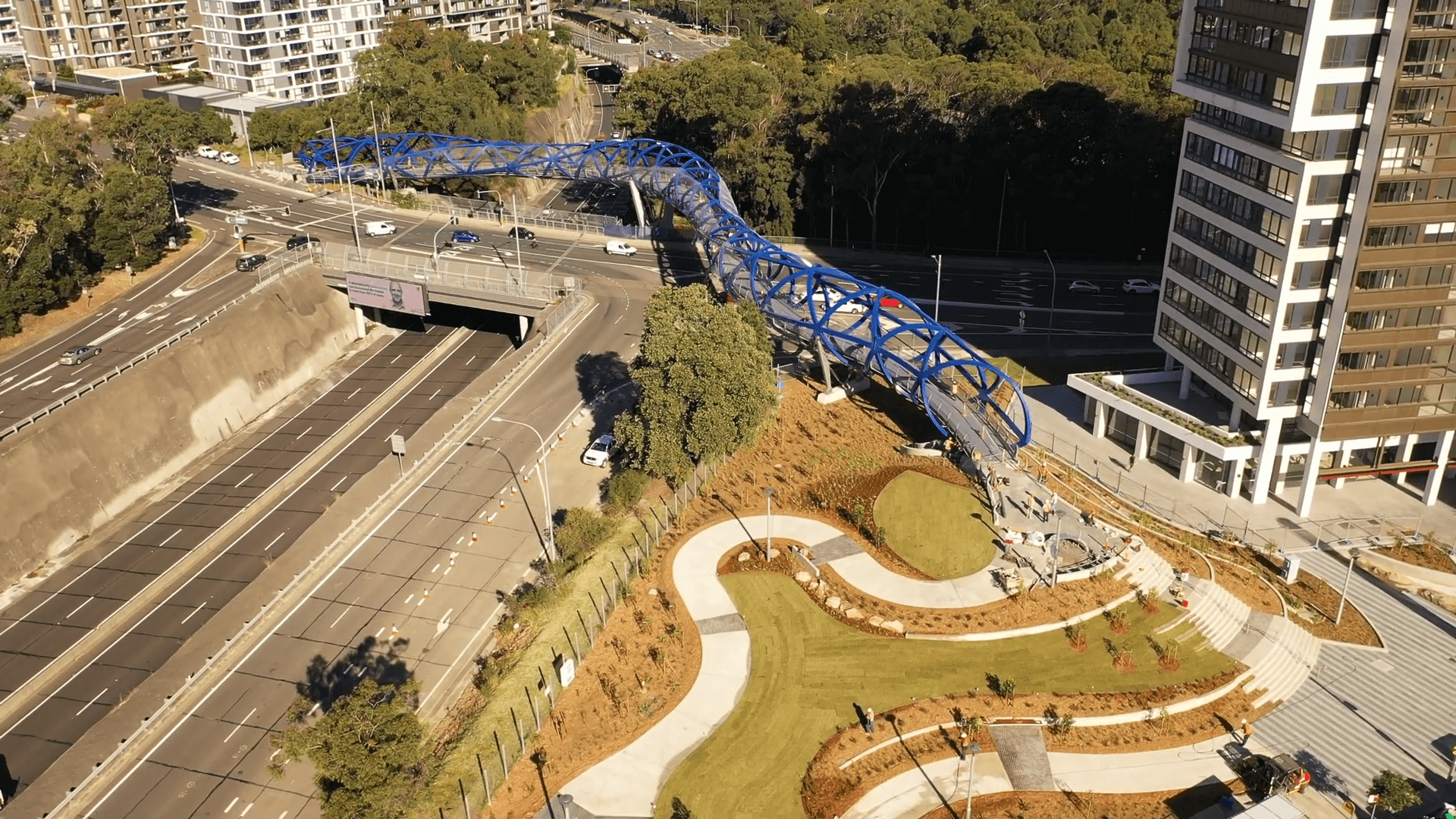
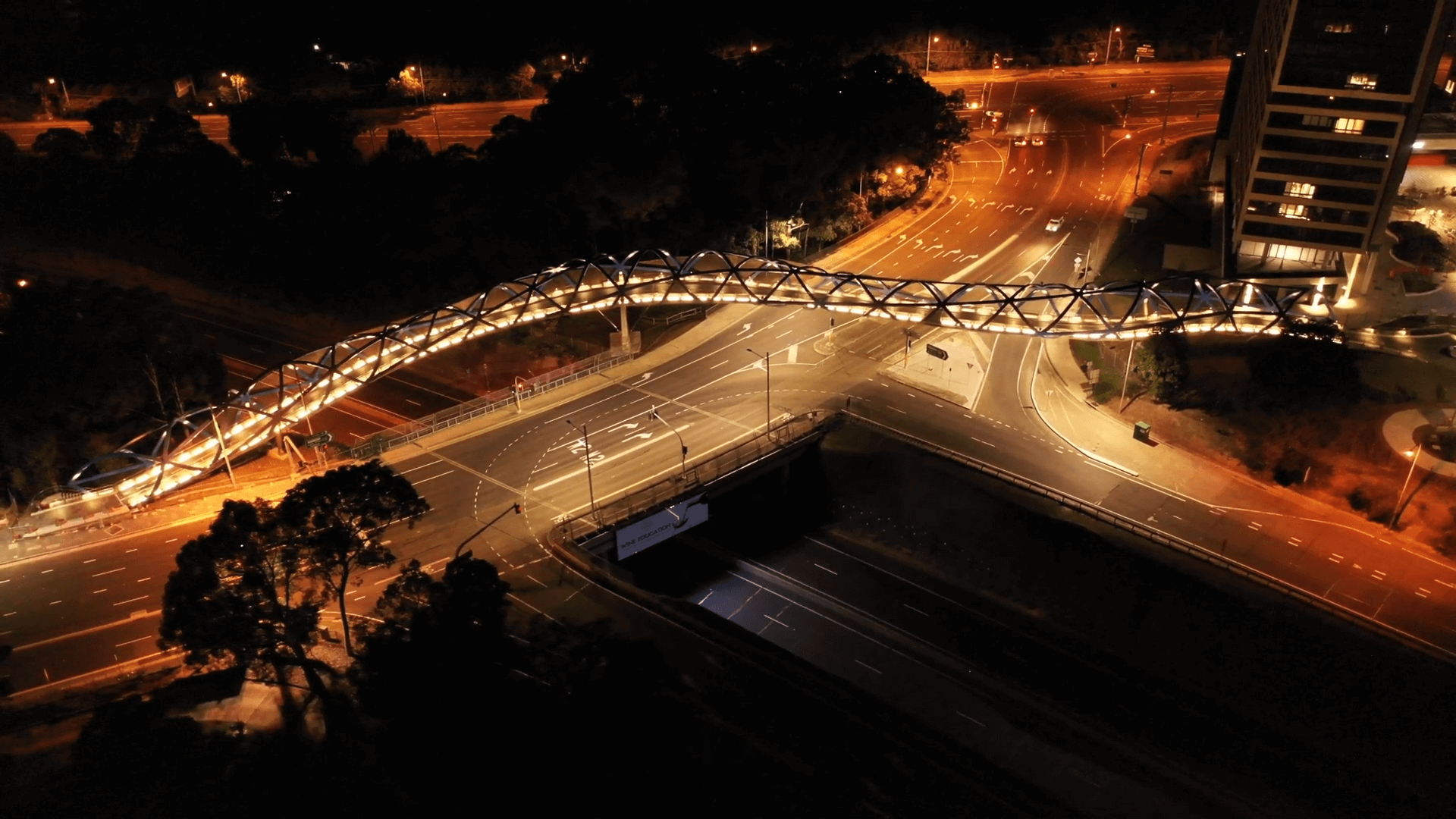