These Prestressed Steel Trays Allow Rapid Construction of Low-Mid Rise Buildings
An Australian company has developed a construction system for rapid mid-rise construction using lightweight, prefabricated steel columns and trays. The company, called PT Blink, says the process can reduce construction programmes by up to 50%.
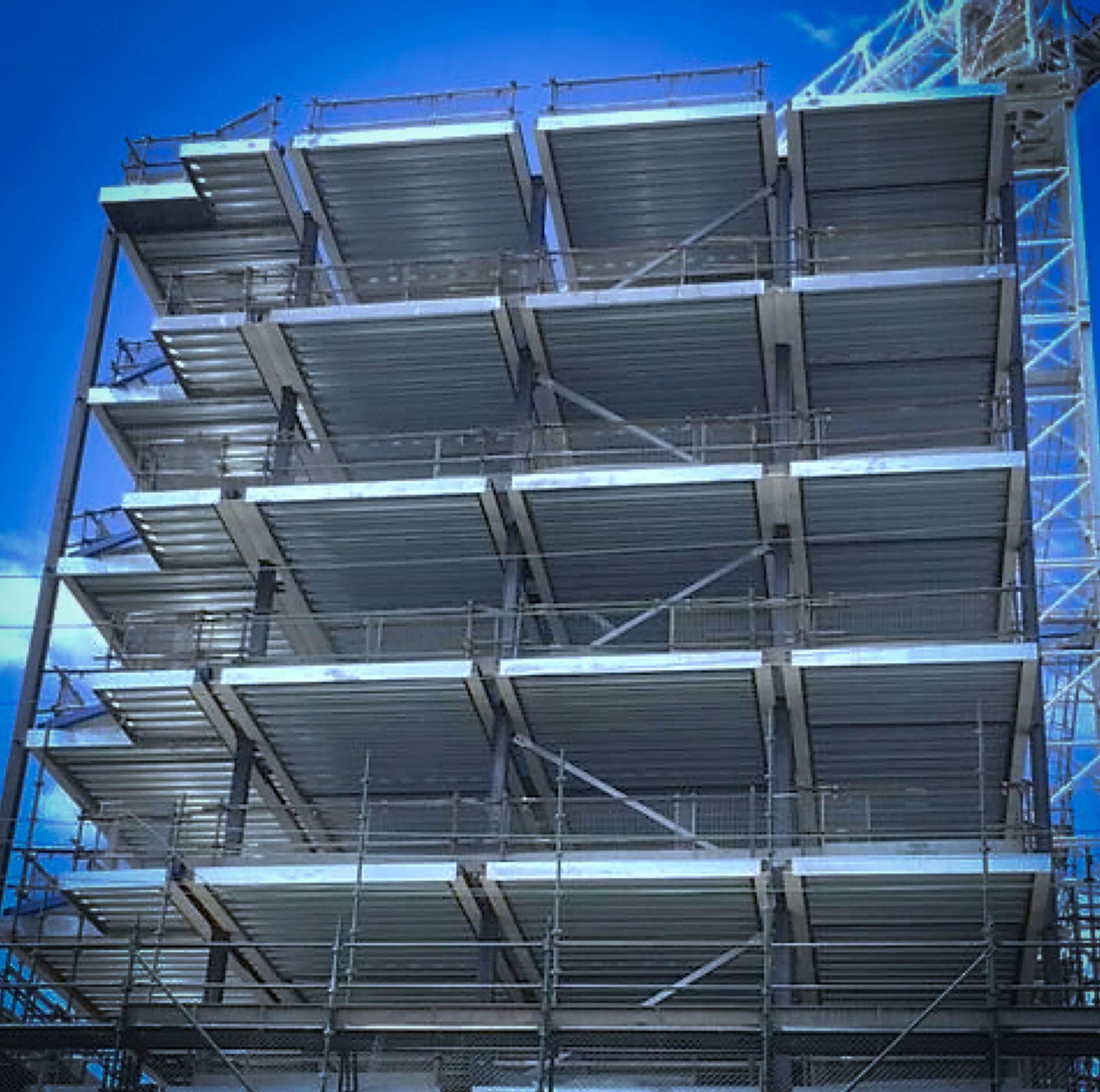
Their construction system uses steel trays and columns which act as permanent formwork to create composite slabs and columns. The trays comprise prestressed steel, which means they contain steel cables that are stressed in the factory to ‘reverse camber’ the steel and counter loads introduced after concrete is poured.
“The prestressing also makes the trays self-supporting, eliminating the need for falsework and formwork – providing immediate access to each floor after concrete is poured,” says PT Blink’s Director of Manufacturing, Wayne Larsen.
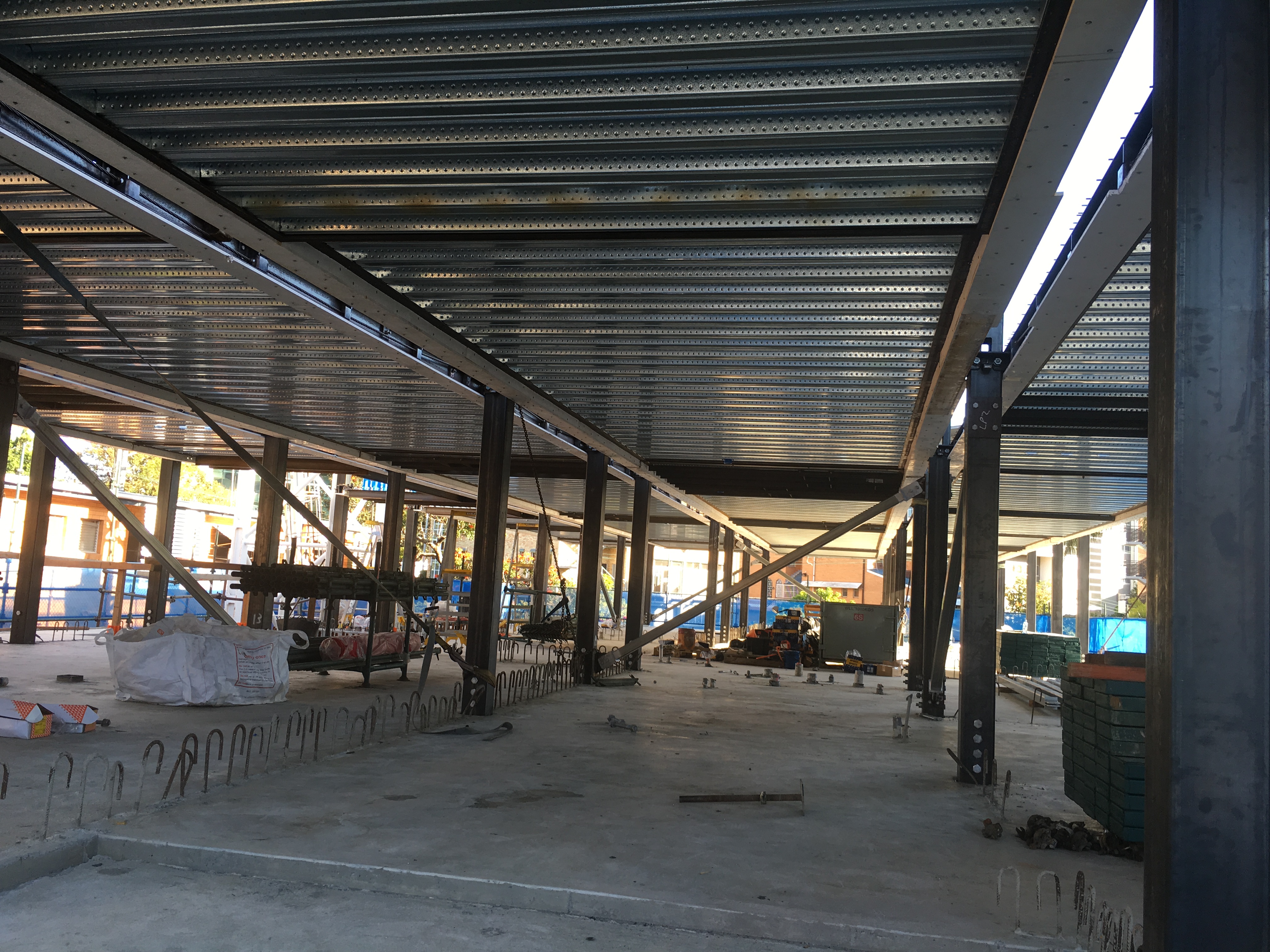
The trays are delivered to site fitted with reinforcement so concrete can be poured into the tray after being lifted into place. This eliminates two major elements from the critical path: formwork and steel fixing.
“The stressed cables are encapsulated by concrete, and the result is a post-tensioned composite slab that is lighter and has larger spans than a typical post-tensioned or conventional slab,” says Larsen.
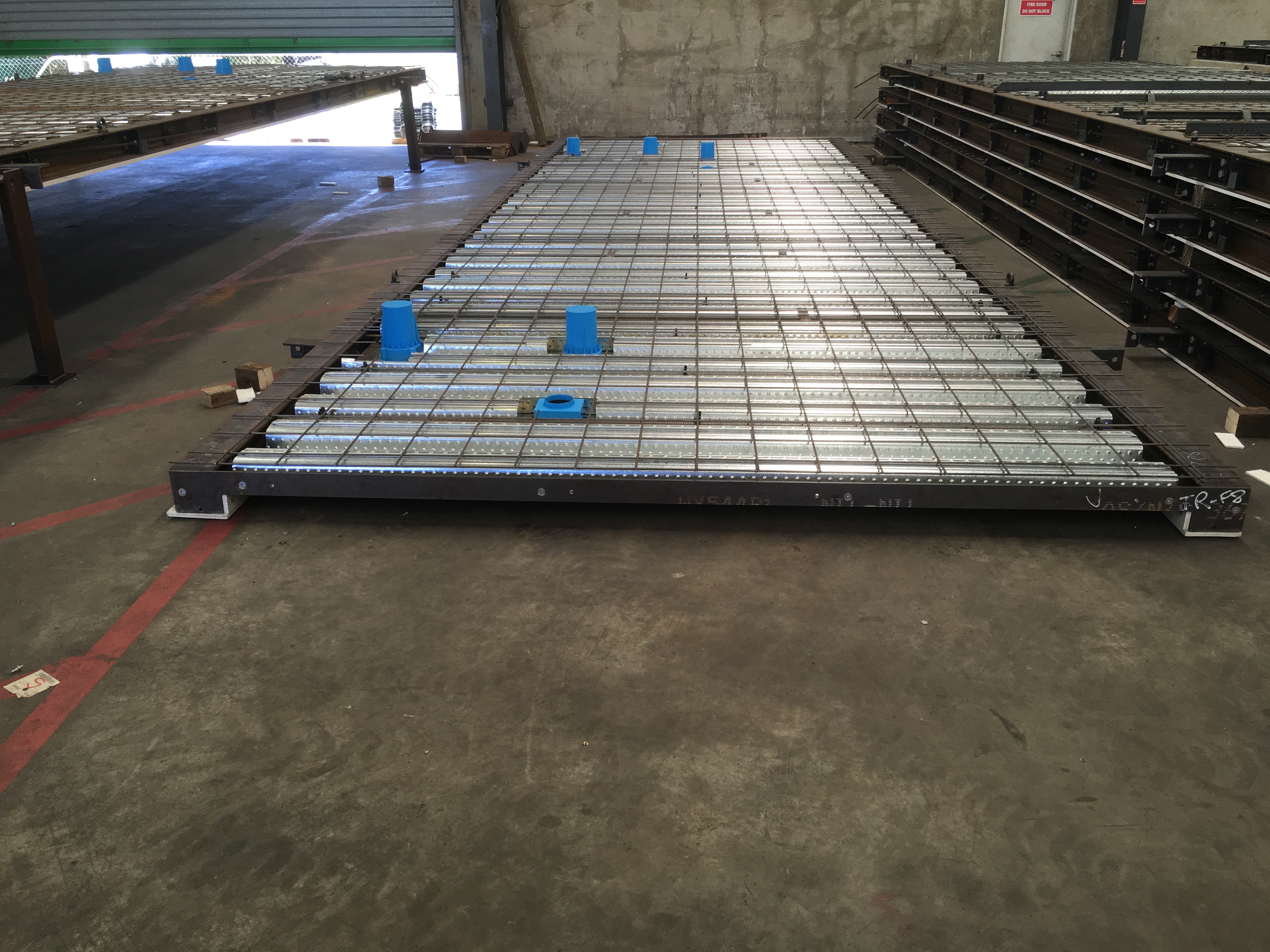
The company claims use of its components reduces construction of the superstructure by up to two thirds. The added benefit is that the lightweight steel ‘backbone’ makes for simple transport and erection without sophisticated cranage.
The design is conceived and modelled in Tekla Structures BIM software. This informs component fabrication which is undertaken by automated robots with +/- 5 mm accuracy.
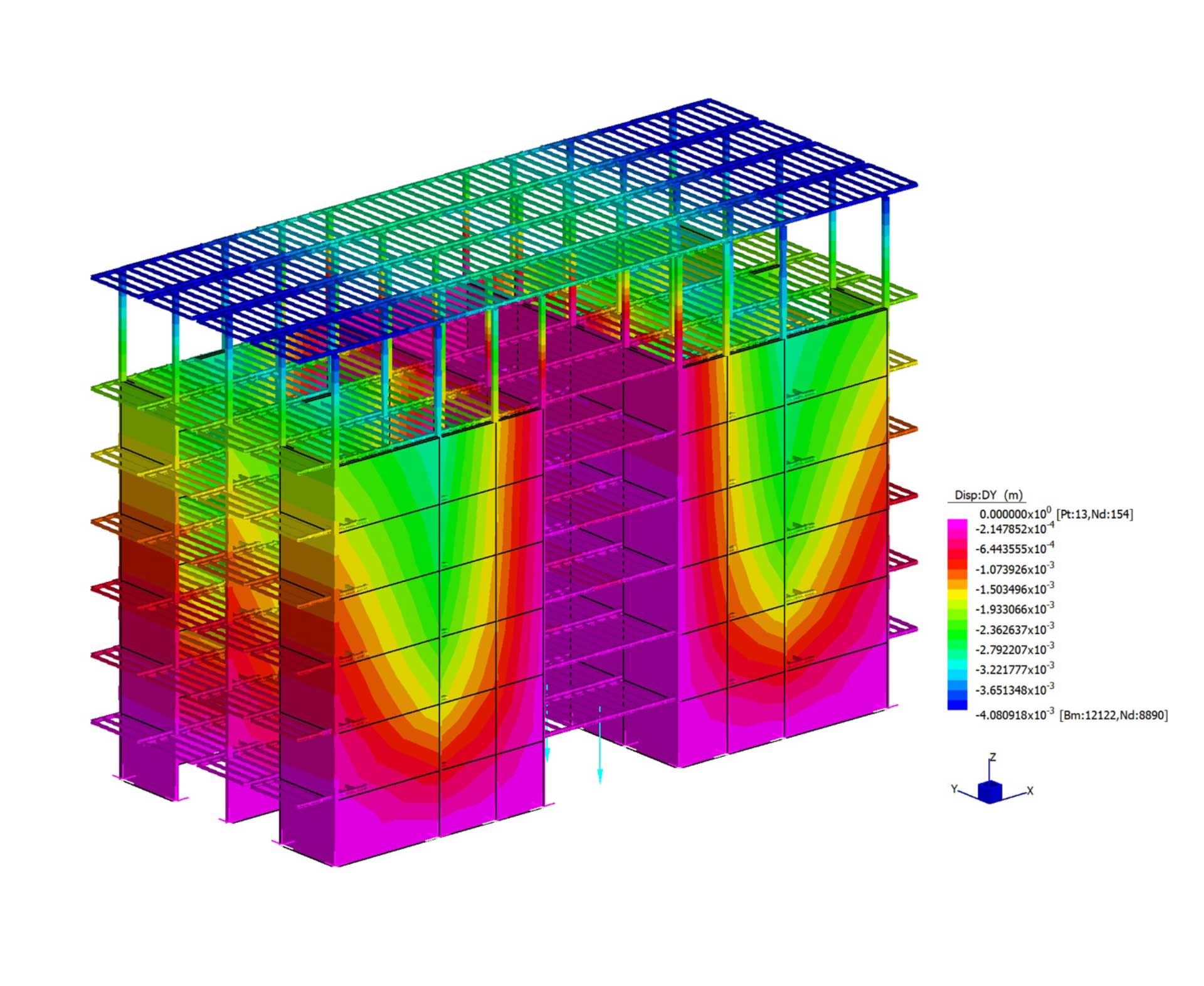
So far, the technology has been used by several developers and builders, albeit skeptical at first.
“Anything new and different in the construction industry is always going to be met with hesitation at first, but we’ve now successfully completed several projects including a residential building in Spring Hill, which was erected in 11 days and achieved a 10 mm variance over 8 storeys.”
So what’s the catch?
The company says the build cost remains comparable to conventional construction, largely due to higher upfront material costs. They say the main benefit lies in the time-savings for developers and owners, allowing them to start generating an income sooner.
Nonetheless, builders also realise advantages through a less congested, safer site with higher accuracy and enhanced quality control. It is also less disruptive for difficult sites, such as when building over occupied premises.
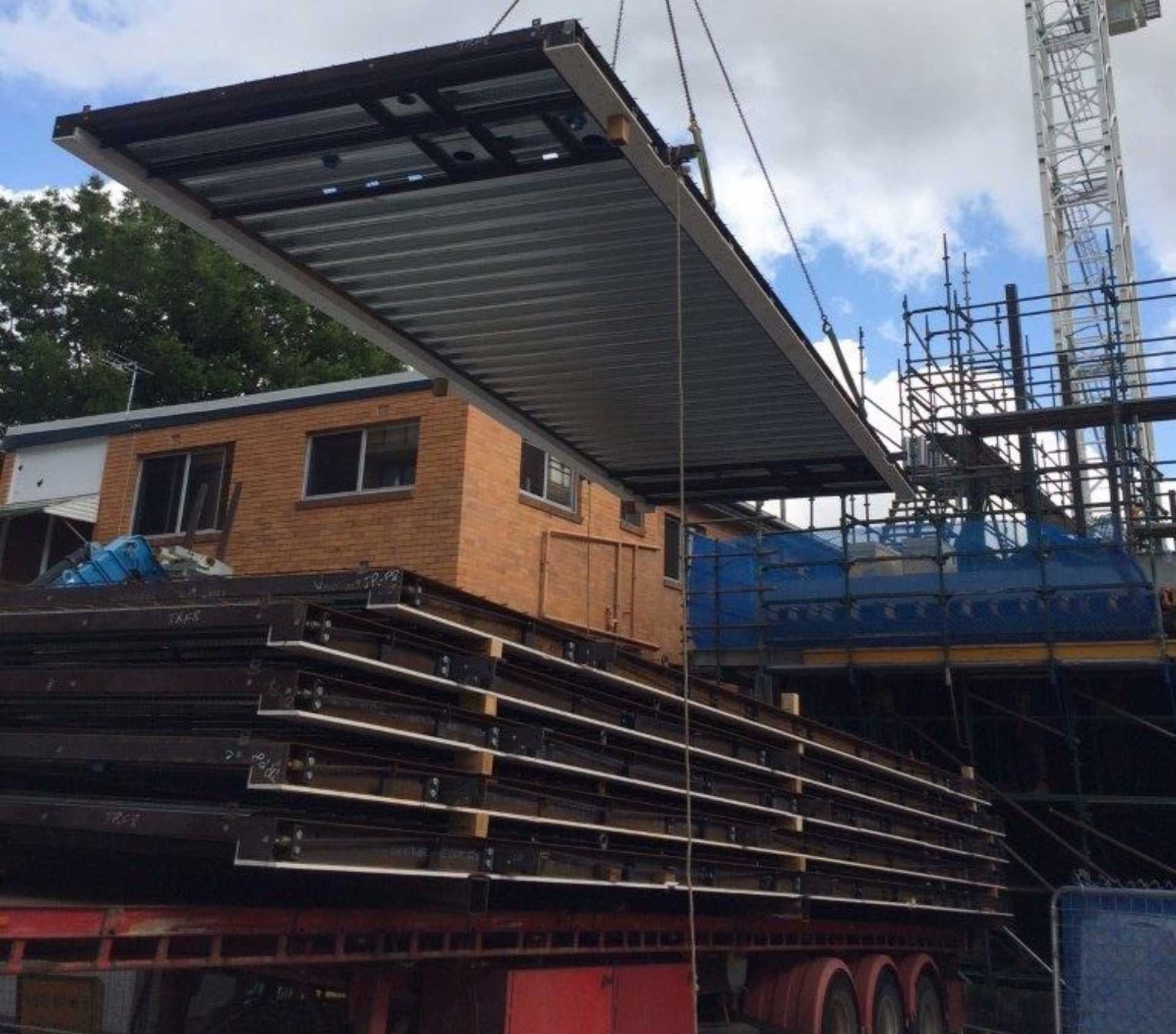
“The sweet spot for our technology is multi-level projects ranging from around 5 storeys and higher, also building over existing structures and land uses. For example building above a government utility or ground corridor without disturbance, unlocking the value of unused airspace” says Larsen.
This ‘tray-and-pour’ construction method, whereby a lightweight prefabricated steel tray is delivered to site and dropped into place ready to receive concrete, is similar to a couple of other systems previously reported on by This Is Construction. The InQuik bridging system allows rapid installation of small to medium-sized bridge decks using preformed trays fitted with reinforcement.
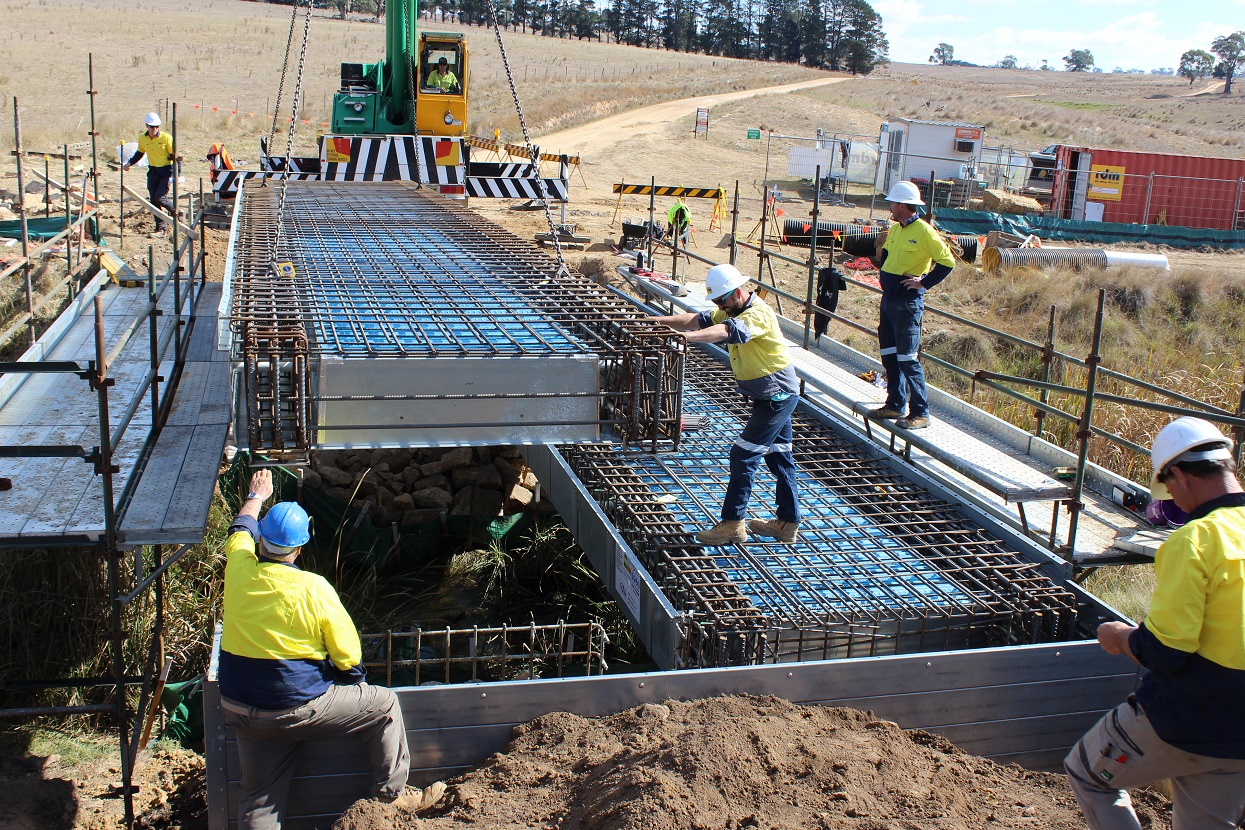
Vienna University of Technology’s (TU Wien) ‘umbrella bridge’ also applies the tray-and-pour method for installing large bridge girders on difficult sites.
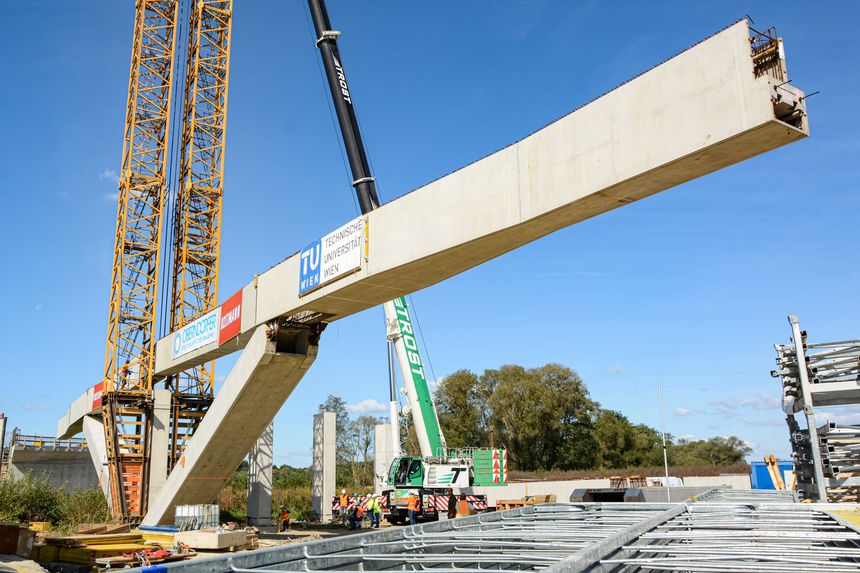
These systems have the potential to make a significant mark on the construction industry. They take conventional permanent formwork options such as Bondek and Condeck and injects them with steroids. They combine the speed of prefabrication and convenience of insitu to meet somewhere in the middle.
There isn’t a requirement for extensive transportation and cranage that precast demands, because the trays are designed to be stackable and lightweight. They eliminate all the temporary works associated with insitu because the reinforcement is designed to support the trays until concrete is poured, making them an attractive option for difficult sites or where speed is highly important.
.jpeg)
But long-term, PT Blink says it is positioning itself as a tech company rather than a construction systems supplier. It plans on licencing its IP to a range of manufacturers to allow boundless adoption. Instead their primary role will be to provide an online platform for which prefab structures can be designed and sourced from a range of suppliers and manufacturers.
The company says that its technology can be adapted to most conventionally designed buildings already but flexibility in design will improve as the platform grows.
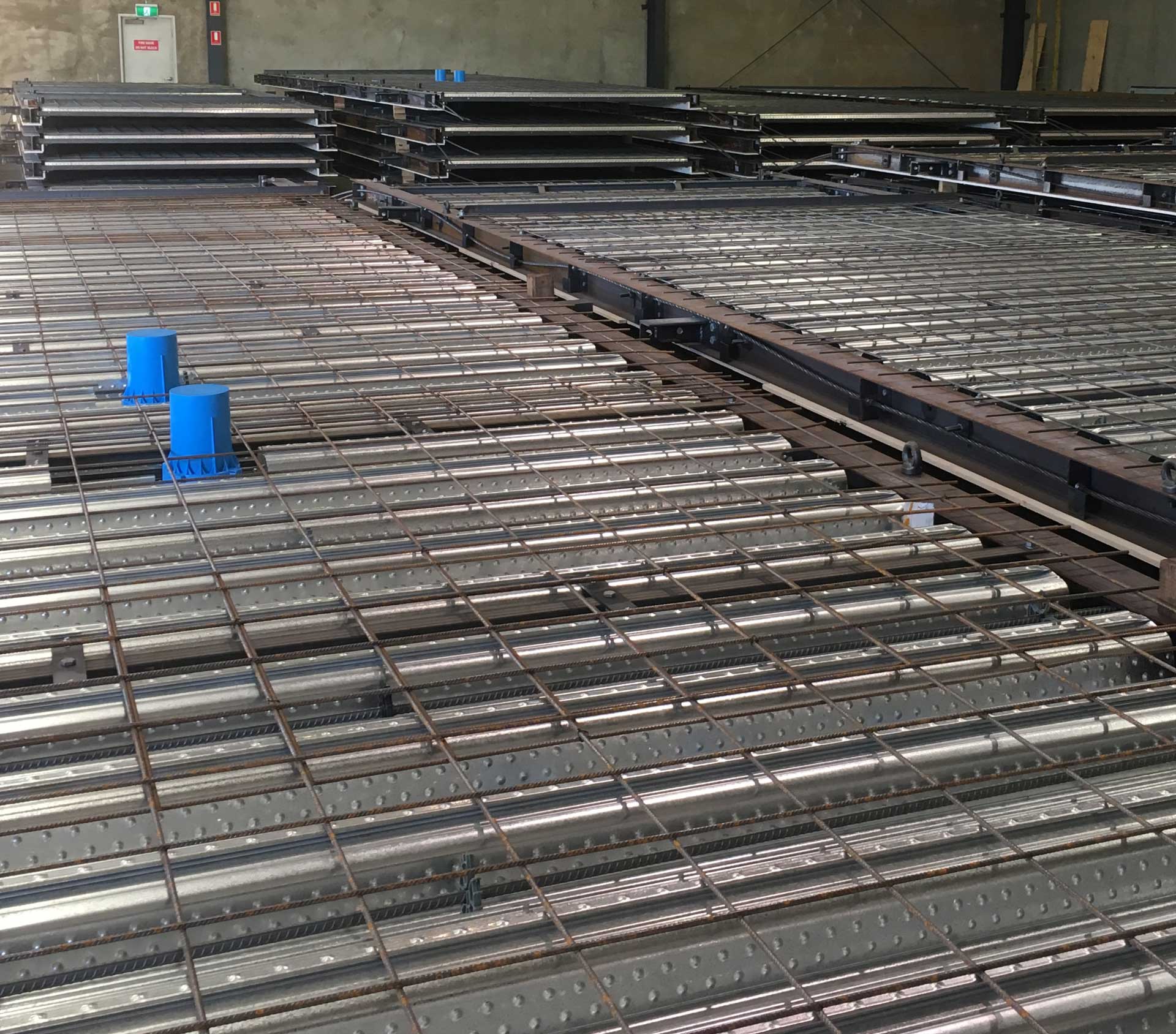
PT Blink was founded around 4 years ago off the back of founder and CEO Murray Ellen’s expertise in large-span structures, such as hangers and stadiums. In 2018, PT Blink raised $250,000 in 6 hours in a crowdfunding campaign.
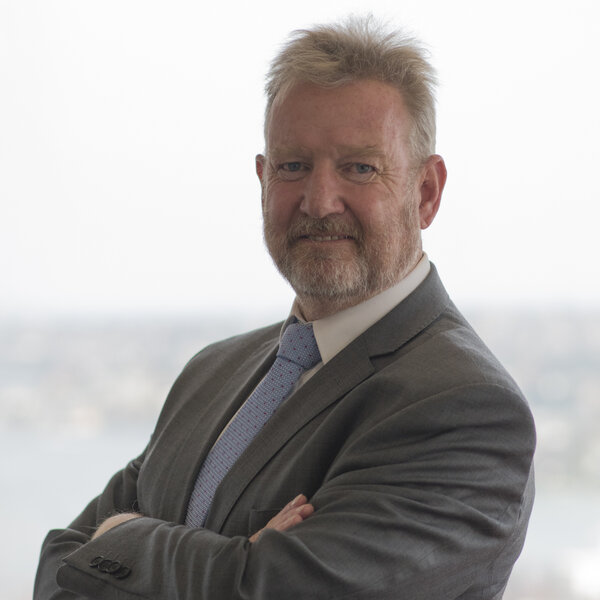
The company is eyeing down the $10 trillion global construction market for their marketplace and patented construction system, with the company saying their biggest barrier is the availability of highly competent manufacturers to licence their IP.
The company says their Design-Manufacture-Integrate (DMI) approach can be likened to the automotive industry:
The car is meticulously designed by engineers, all the components are then manufactured by various suppliers, and finally the car components are integrated to complete the car assembly.
“The Design-Manufacture-Integrate approach will allow property developers to source components for their project from a range of prefab manufacturers, whether that’s the structural backbone, bathroom pods, stairs or facades, and use that information in a completely integrated ecosystem.”
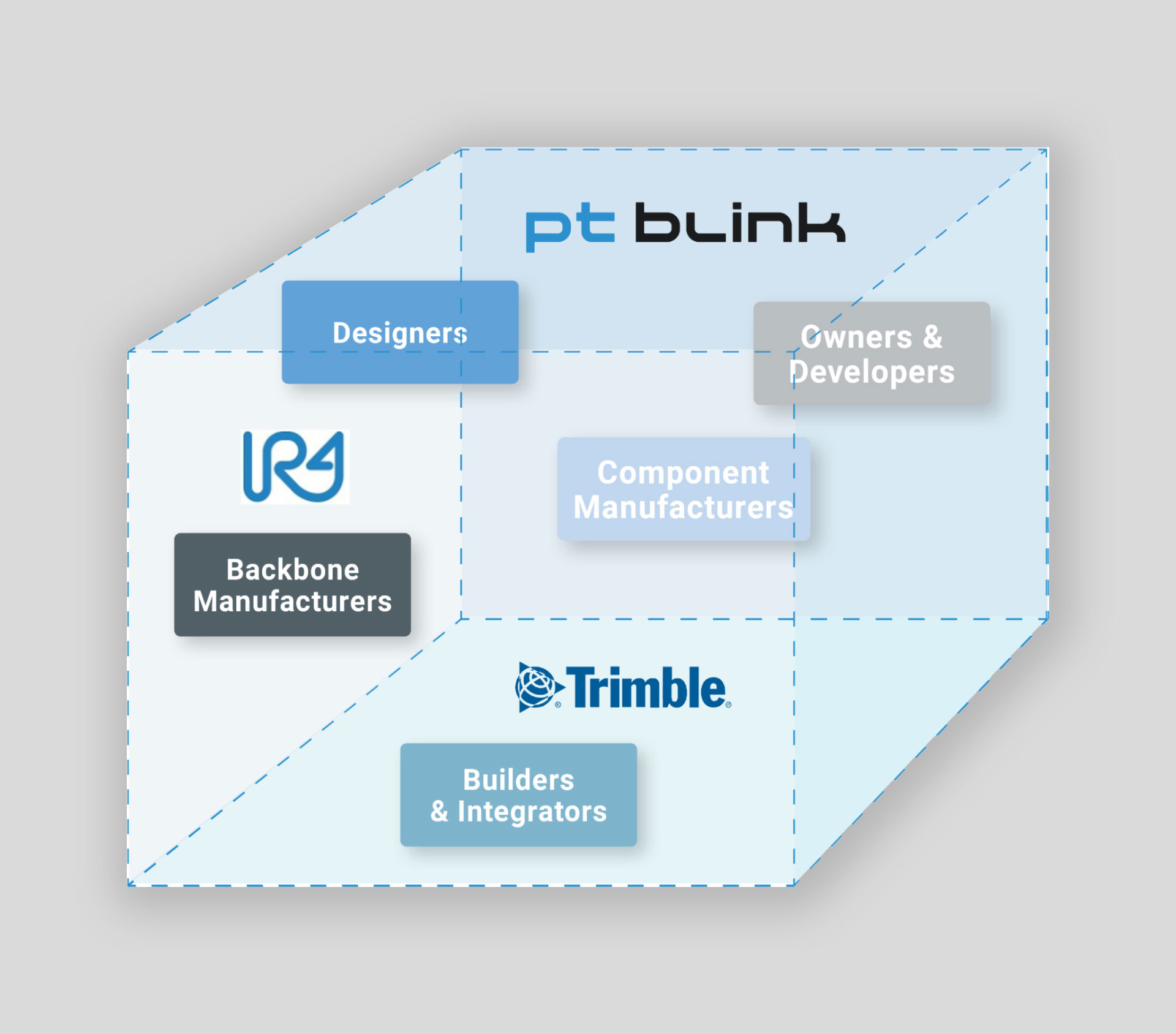
PT Blink’s prefab marketplace utopia seems like a logical next step to reduce a currently very segmented prefabrication market made up of a range of designers, manufacturers and contractors.
By aggregating these elements into one space, the barriers to sourcing various components and incorporating them during the early stages of the design process are significantly reduced. This will provide greater incentive for owners and developers to choose this path from the outset, particularly on complex sites or where time constraints pose feasibility issues.
Ultimately, it creates a more streamlined process for the delivery of prefabricated buildings, opening up a world of prefab possibilities.

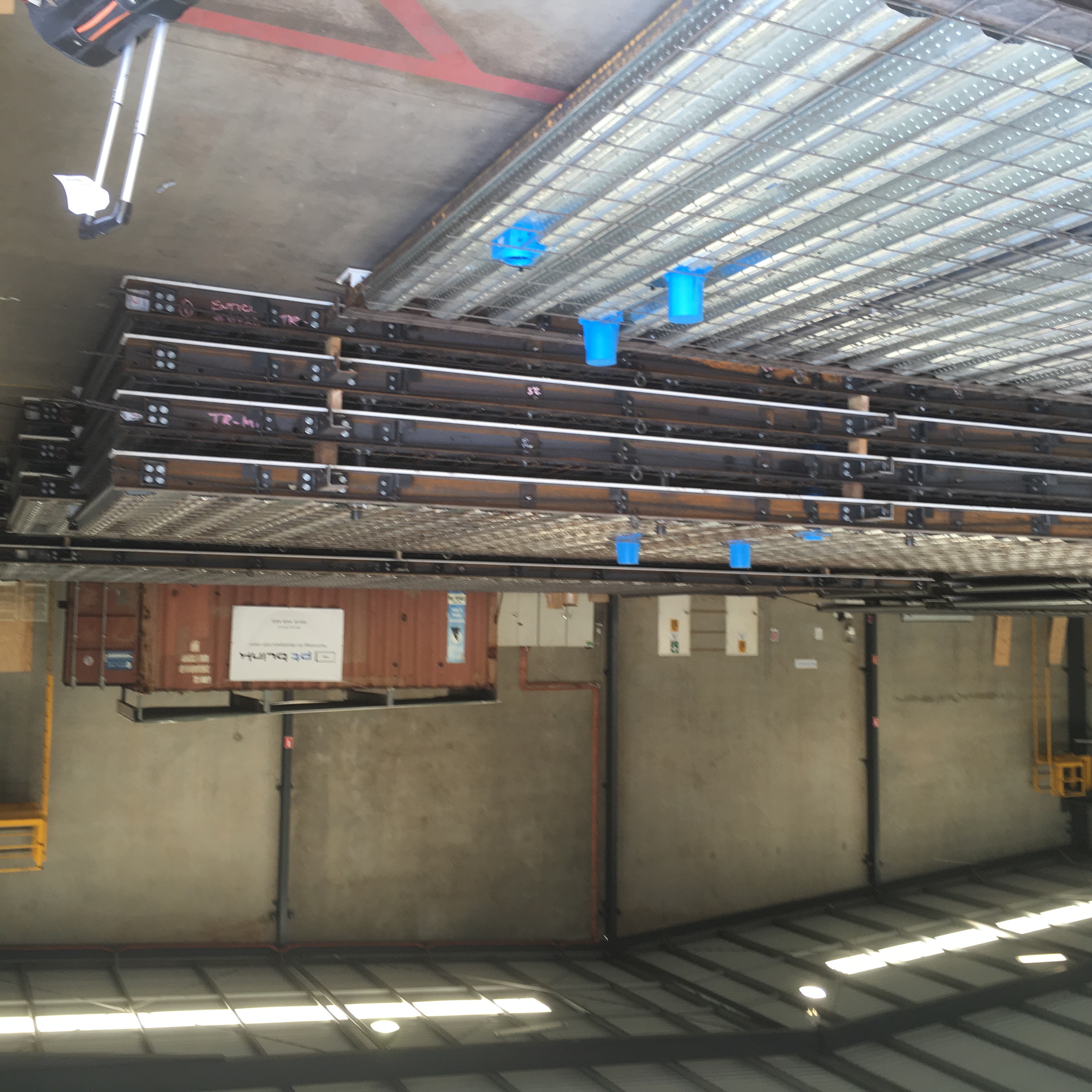
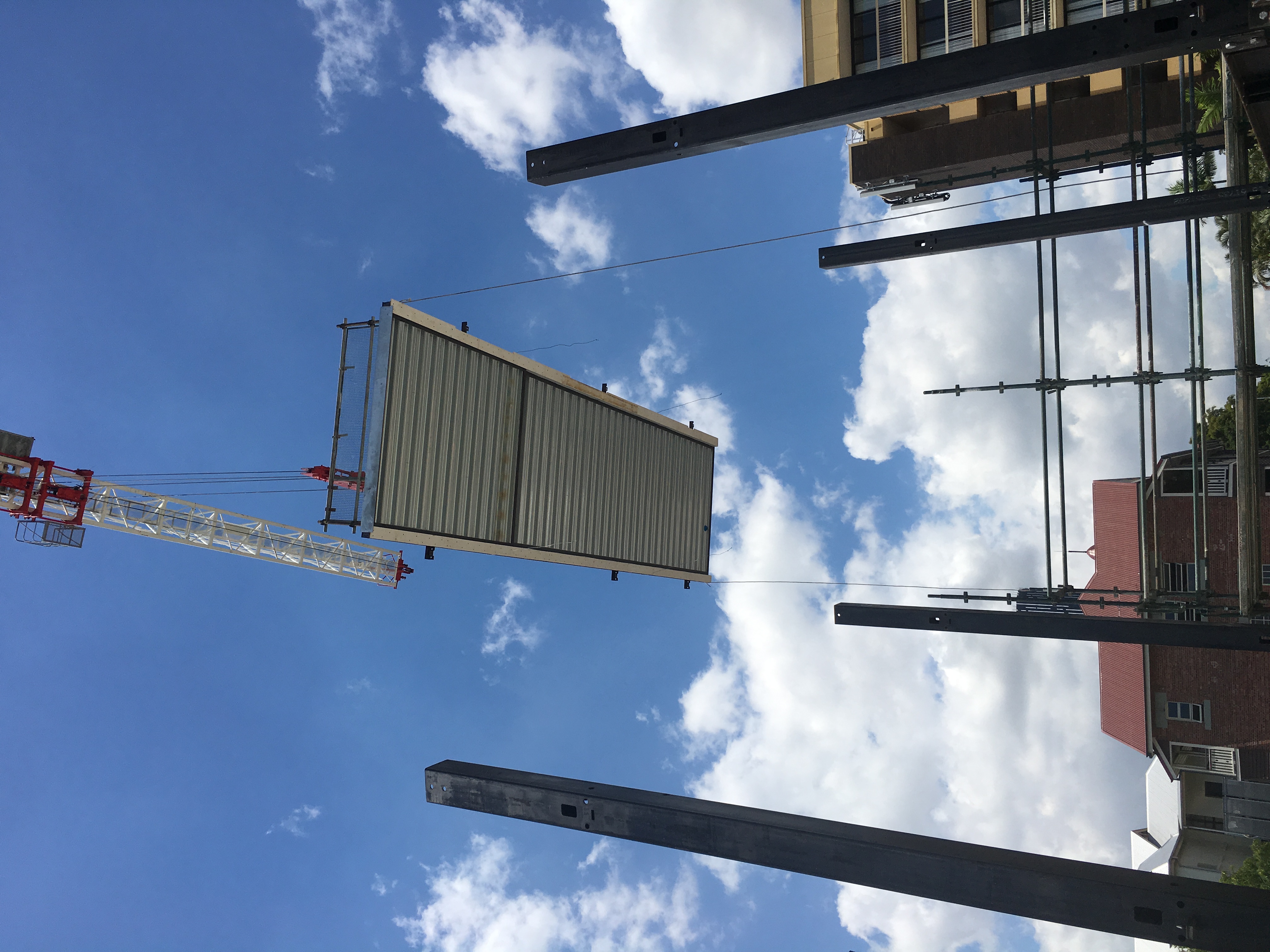
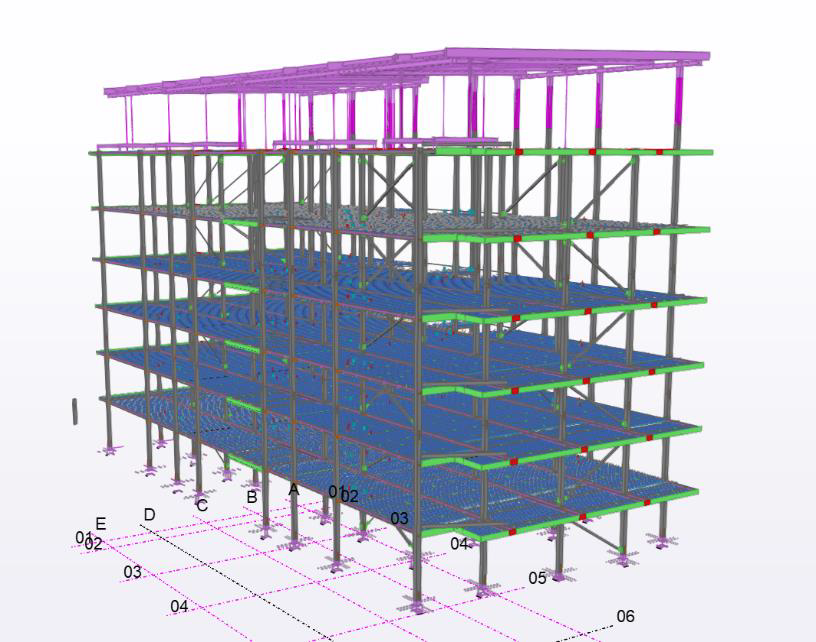