Overcoming a Logistical Gauntlet: Space Efficiency Key to Delivering North Sydney’s Tallest Building
A tightly-bound worksite in a busy commercial area. Strict deadlines. Strong winds. Bushfire smoke. A global pandemic. The construction of One Denison presented many serious challenges. Yet through strict, efficient planning, Northern Sydney’s tallest building was ultimately delivered on schedule in late-2020.
Building commenced on the 39-storey, $1.2 billion commercial office tower in 2017. After terminating its contract with Grocon, developer Winten Property Group hired Multiplex to take over work in January of 2018.

“Prior to our commencement the extremely tight program was critical for the success of the project,” says Multiplex Project Manager, Michael Notley.
“The logistics had to be strictly controlled to allow us to complete the build while maintaining access for all adjacent parties.”
Considering the worksite was situated essentially boundary to boundary between Denison Street, Spring Street, and Little Spring Street, this was no easy task. These narrow streets are home to other large commercial buildings, restaurants and popular parking facilities. Office workers, local residents and visitors to nearby hotels move through the area at all times of day and night. Developing methods of construction that allowed for uninterrupted work while maintaining the safety of the public would be crucial to ensuring the project was completed on time.
There was no time to waste. Anchor tenant Nine Entertainment Co signed a 25,000-square-metre leasing deal in April 2019, and the company wanted to move in early. That meant delivering over one-third of the building’s net lettable area within a small window of time.
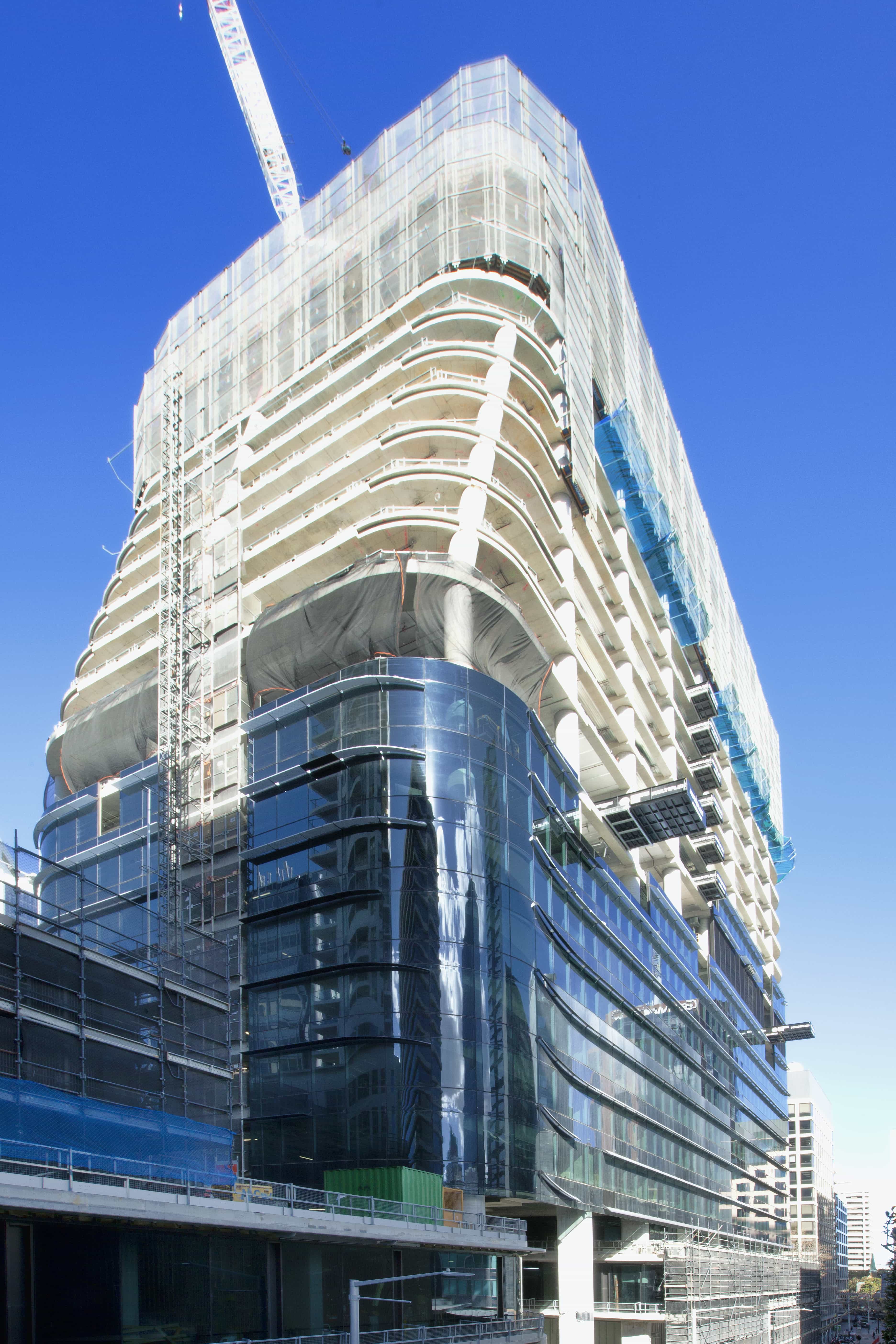
The innovation and efficiency that made the project such a success began on basement level two. The concrete core raft slab of the building was constructed on a rock shelf at this level, despite three more levels of basement still being required below. The implementation of scaffolding and a cantilever protection deck allowed ground work to continue at the same time the jumpform was being installed. This decision saved valuable time as delivery goals grew closer.
As the scope of the work expanded, Multiplex turned its attention to other logistical challenges presented by the tight site and adjacent work zones. Ultimately, the company implemented four initiatives critical to overcoming these constraints.
- Diligent pre-planning and prioritisation of all plant and equipment for efficient space utilisation.
- Just-in-time deliveries to minimise storage of excess material.
- Substantial consultation and pre-planning with North Sydney Council to implement road closures and ensure the safety of workers and the public.
- High-risk workshops undertaken prior to work commencing to ensure comprehensive planning for all critical risks was undertaken.
As the building rose higher, and handovers were met, a new challenge awaited: the installation of One Denison’s iconic, inclined, Bates Smart-designed facade.
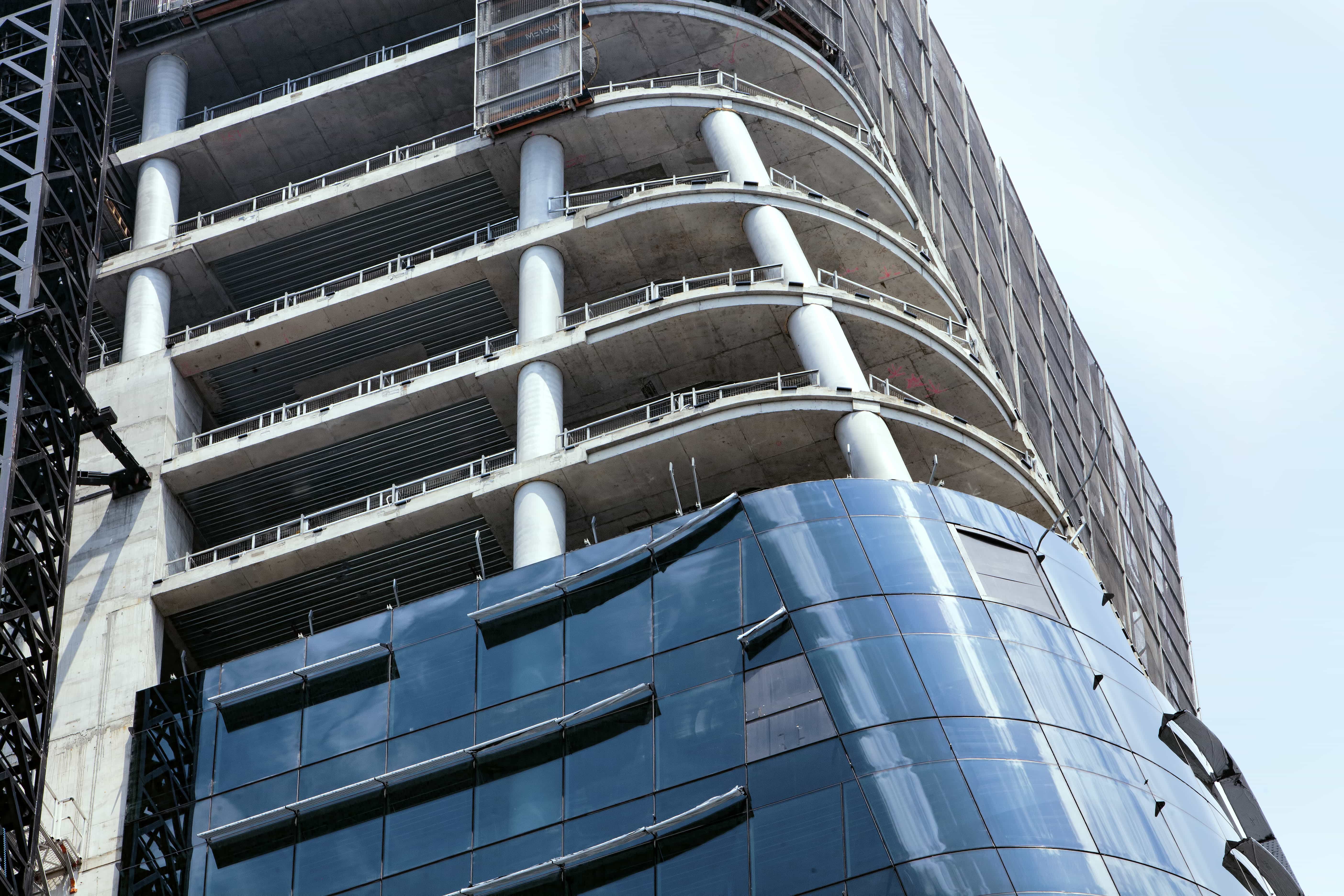
“The curved crown facade required extensive modelling and detailed design,” explains Notley. “Each individual tube has a different radius as the facade curves in two directions.
“We assembled a 20-panel visual mockup to validate the design and facilitate the signoff process. All this detail then needed to be communicated to international supply partners through 3D drawings and checked by our project team and specialist consultant.”
Fabricated in China, each curtain wall panel is approximately 3750mm tall x 1800mm wide. They consist of an aluminium frame and two pieces of double-glazed unit glass structurally glazed into the frame.
Not only is the design of the panels simple yet striking, it complements the team’s goal of creating a tower building with minimal impact on the amenity of its neighbours. By tapering the upper 75% of the tower to the south, the skyplane was increased for adjacent buildings, One Denison’s bulk was minimised and the outdoor terrace received a more spacious outlook.
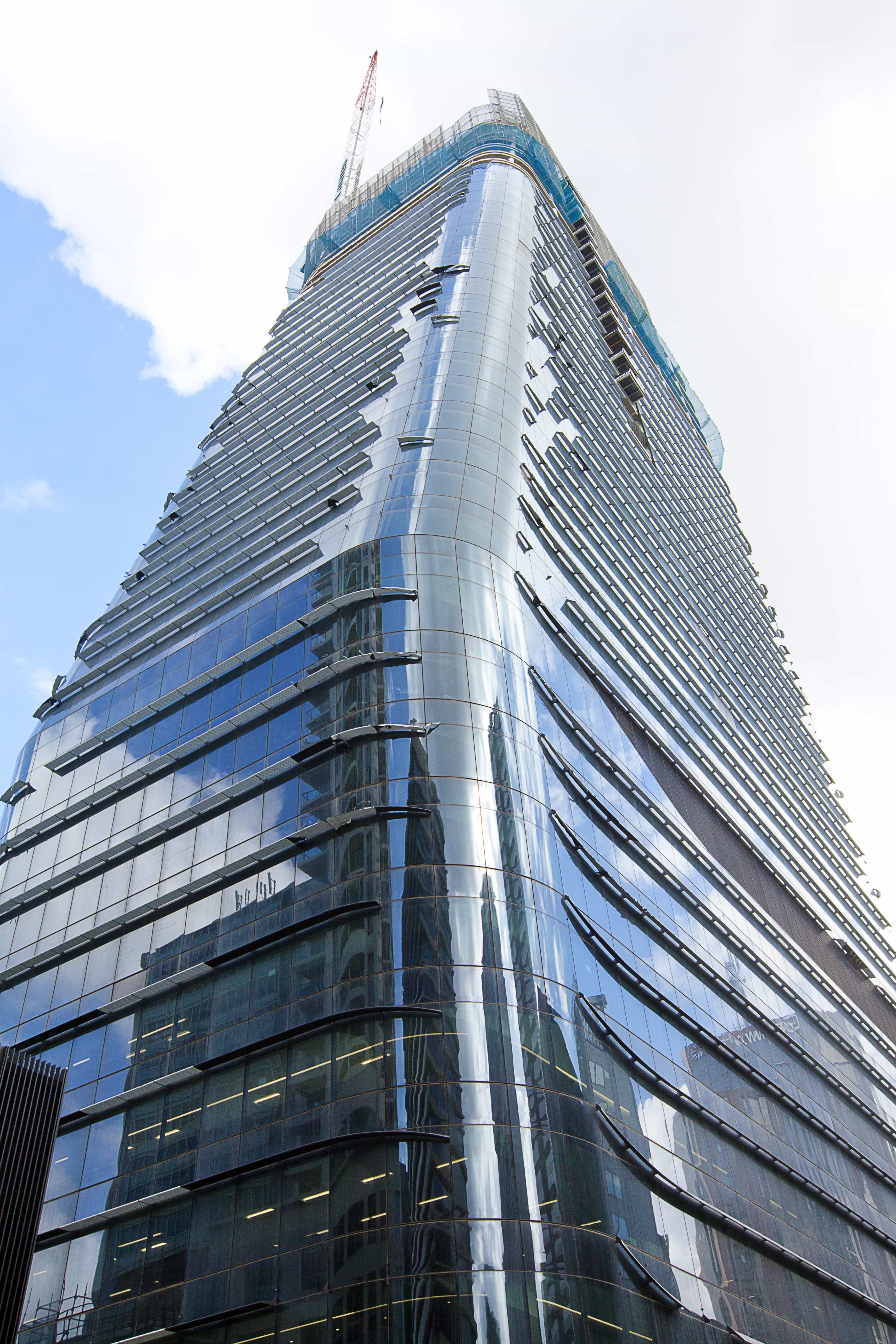
Notley describes the intricate process of installing the panels.
“The curtain wall patterns are fixed to the concrete slab using engineered brackets and installed with a small crane by being ‘launched’ out the side of the building.” As for the inclined panels, they were designed as straight panels to be installed on a lean.
Natural conditions at times threatened to slow construction down. Strong winds were an obvious concern for North Sydney’s tallest building. Thick smoke resulting from the horrific ‘Black Summer’ bushfires of 2019 and 2020 made working outdoors or in poorly-ventilated areas difficult. Then there was COVID-19, which forced the construction industry at large to make operational shifts.
A less-efficiently planned project may have suffered significant delays considering all these challenges. One Denison, however, reached each of its delivery goals on or ahead of schedule, thanks to Multiplex’s thorough planning. The benchmark project serves as a reminder that constantly asking how the building process can be made more efficient and streamlined can result in a range of benefits for everyone involved.
One Denison has already established itself as an icon in the region. Nine, along with multinational software company SAP, moved into the building in 2020. Microsoft Australia is set to follow in April 2021.
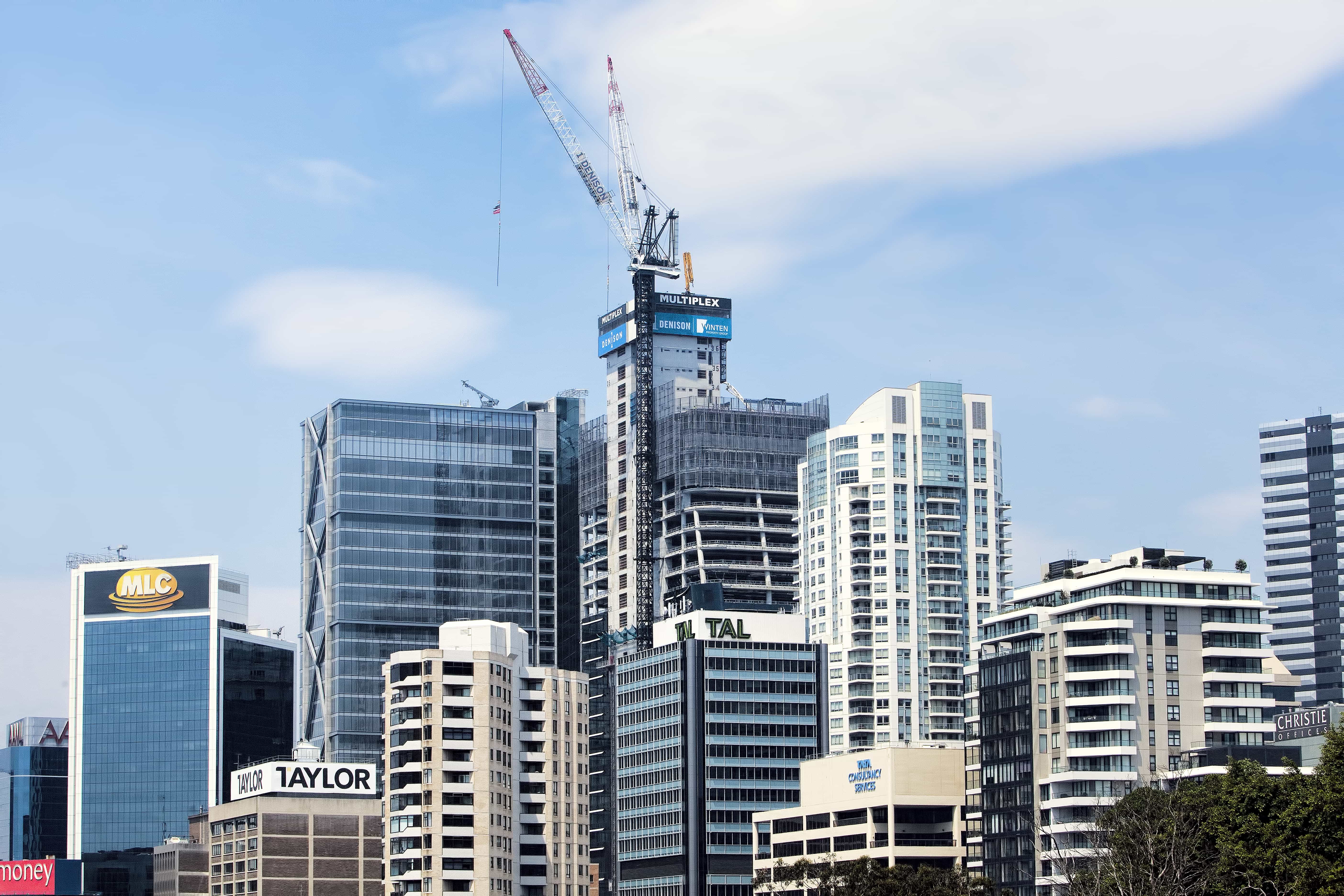
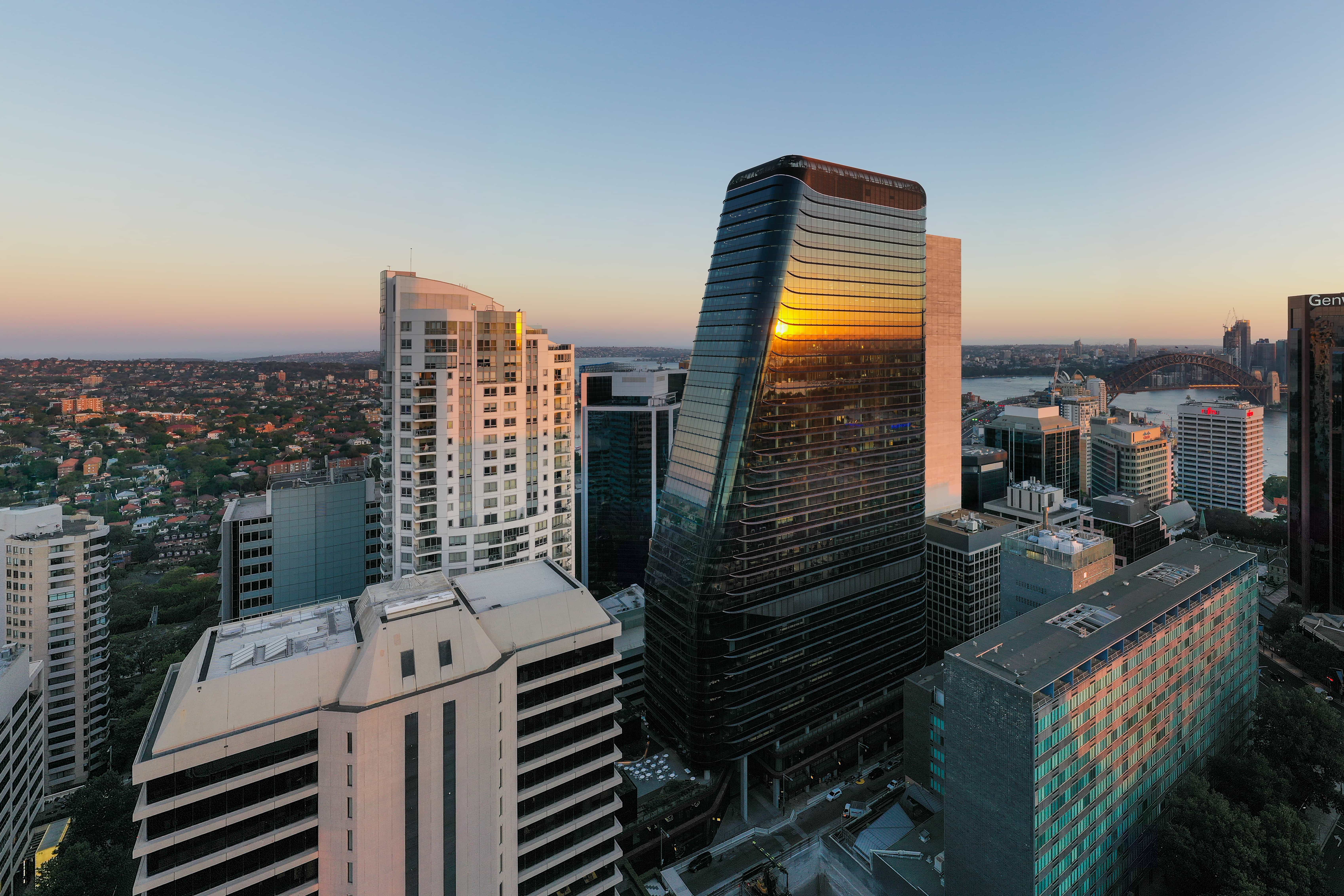
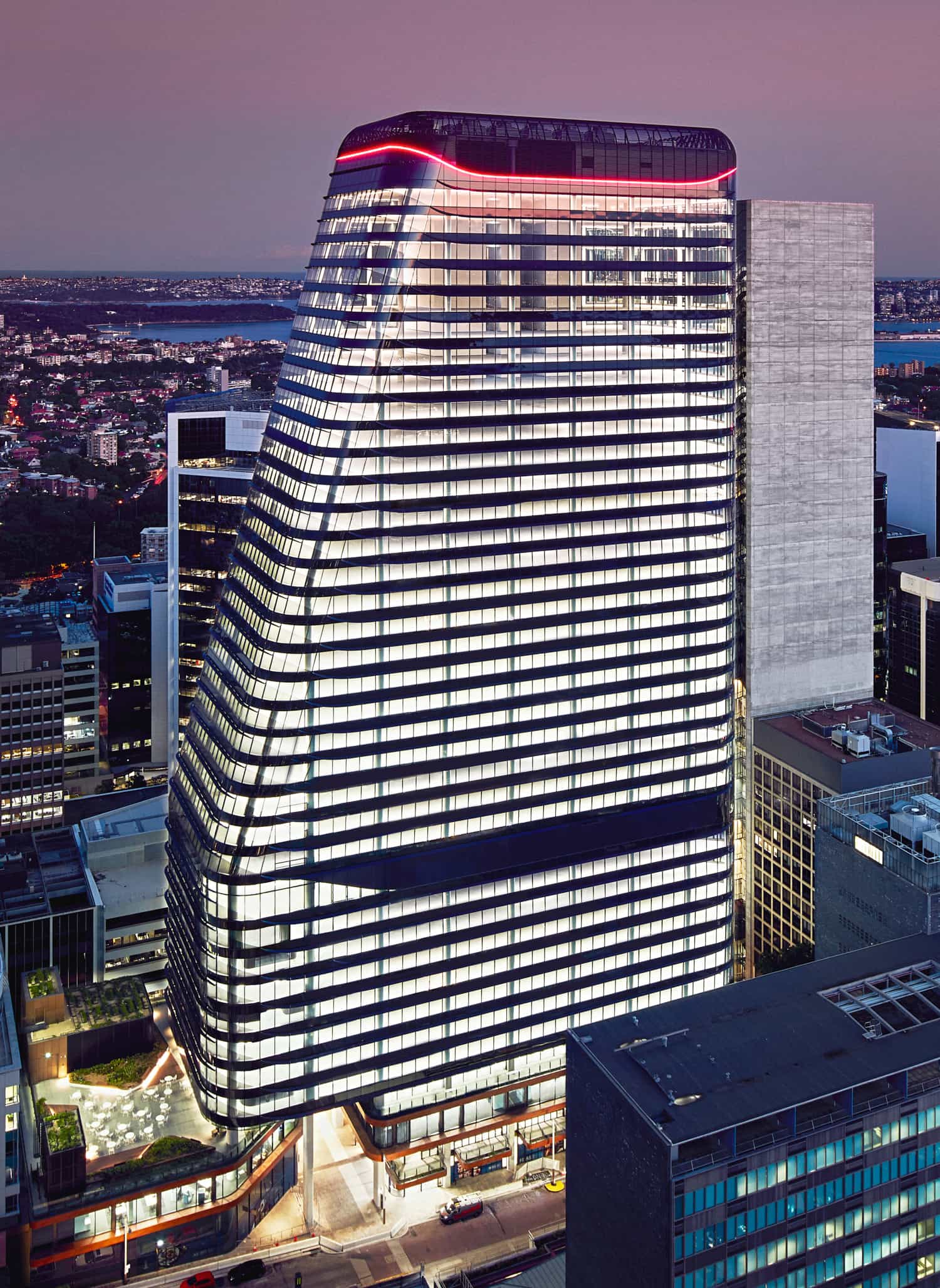
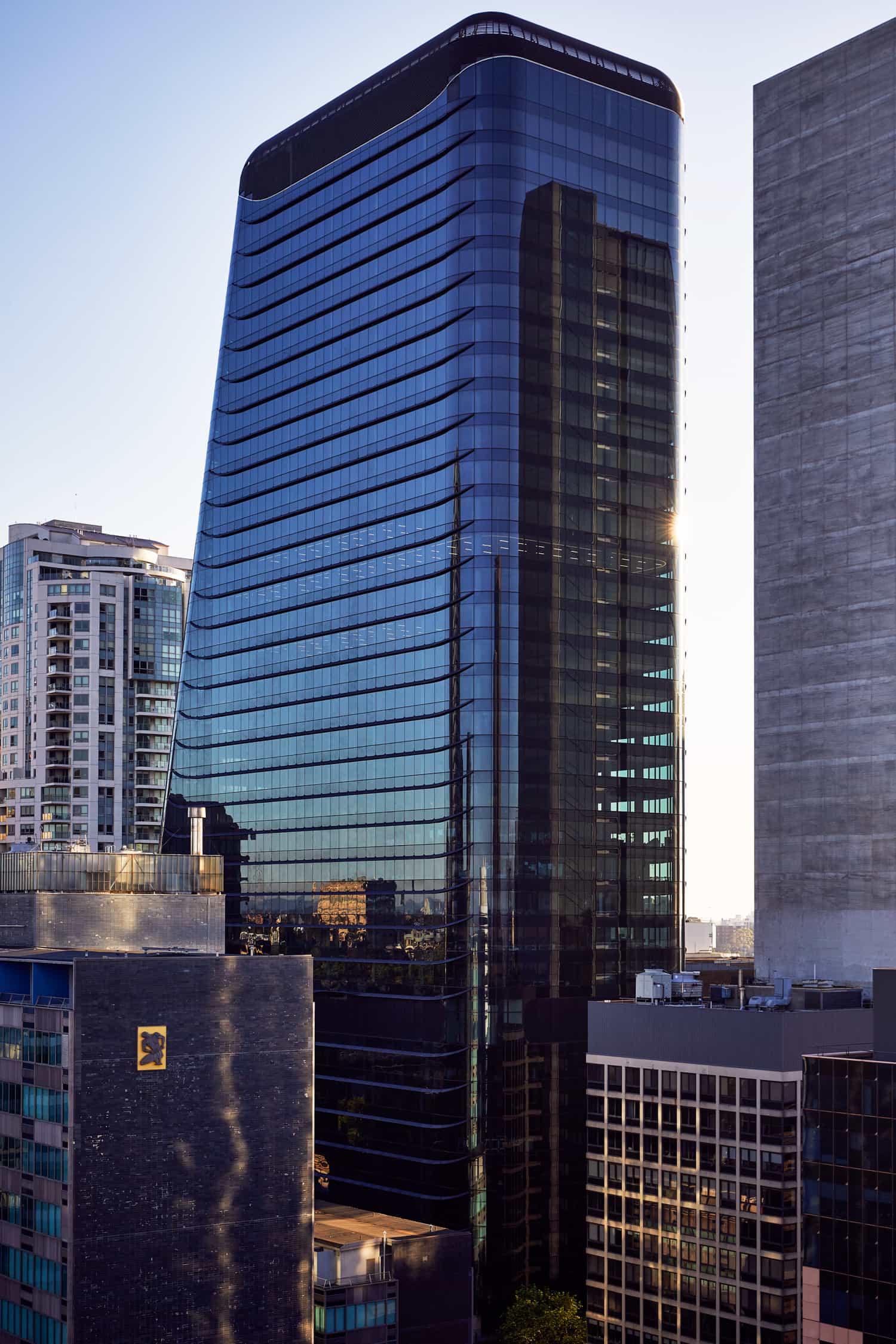
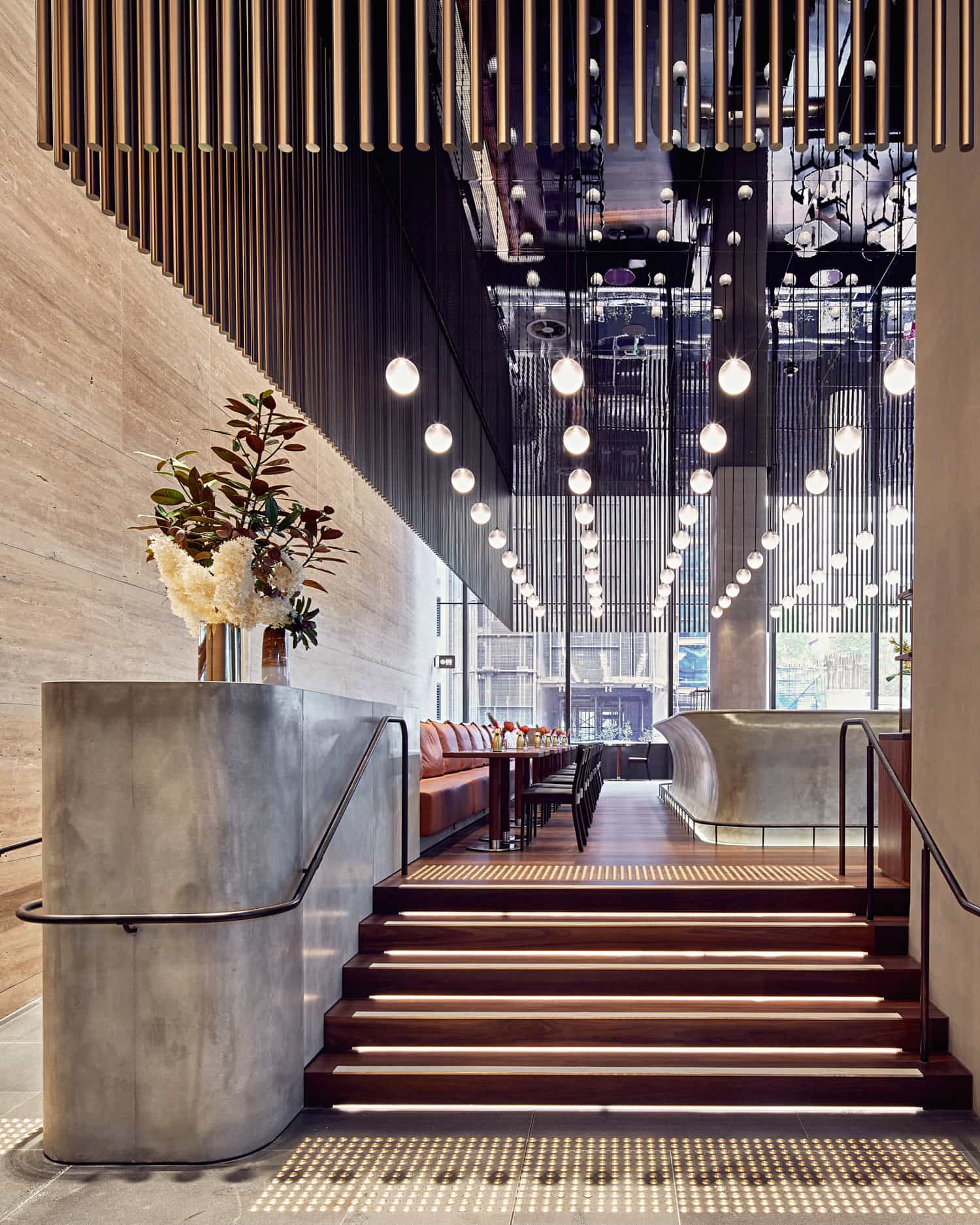
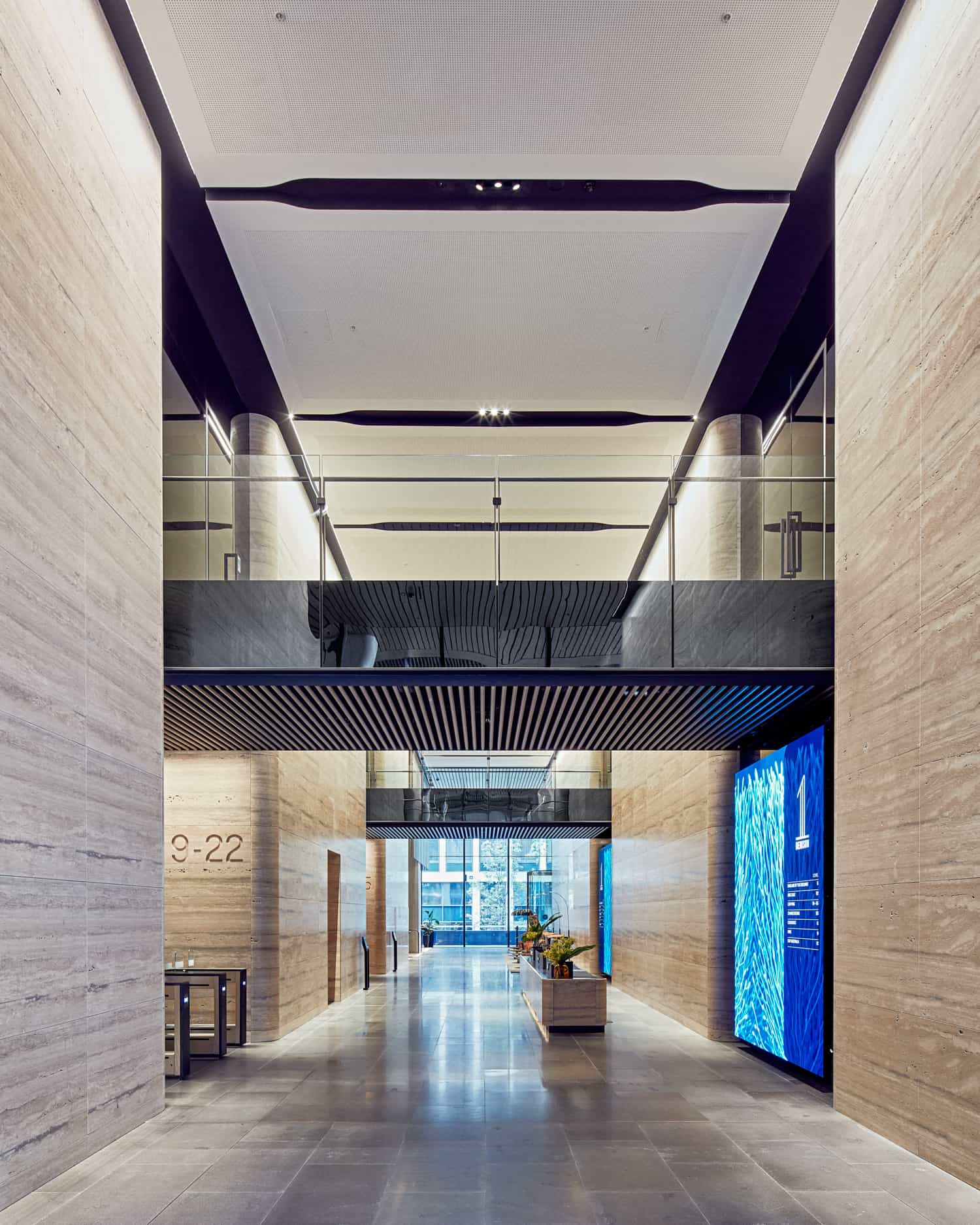